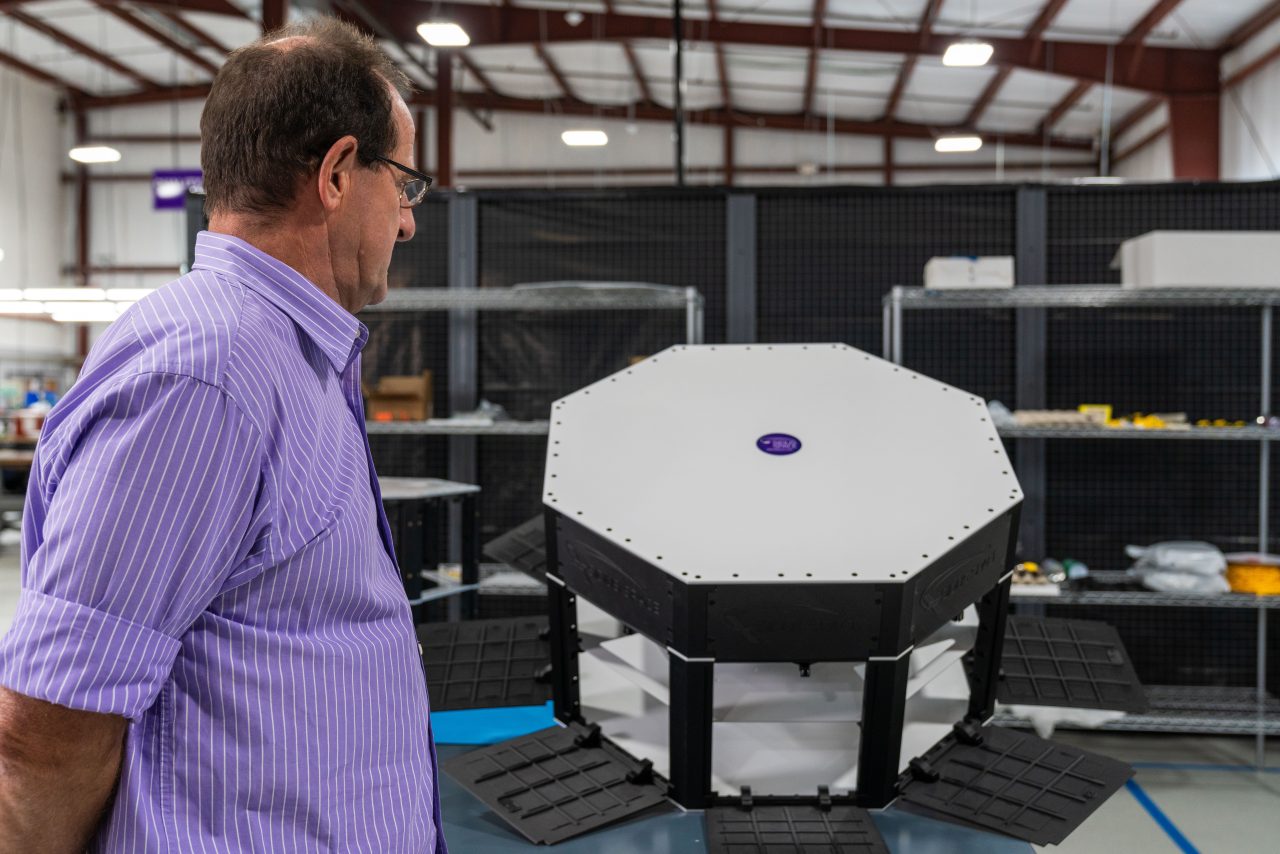
Markforged 3D printing solutions were used to develop a radically new style of satellite.
The 3D printer manufacturer collaborated with Sidus Space, a ten-year-old company providing space and defense service solutions. They worked with Markforged to help devise their new satellite concept, which heavily leverages additive approaches.
Challenges in Satellite and Aerospace Design
The issue with satellite (and aerospace) design is all about weight and function. To put vehicles and devices aloft, they must be as light as possible. However, it’s not easy to remove components and material while ensuring that the system still functions properly.
The space environment, in particular, is rather hostile. Systems are subjected to extreme temperatures and thermal gradients: in sunlight, surface temperatures can exceed 100C, while shadowed surfaces might be -100C. In addition, there are severe radiation hazards to endure.
To protect the vital internal systems, satellites have traditionally been designed with a lot of metal to withstand these environmental factors. However, metal is heavy, and that makes for a problematic situation. Every gram of metal added represents a gram of payload that can’t be used. The purpose of the system is really to take payload aloft, so you want to maximize the payload and minimize the structure supporting it. The weight of the payload and its supporting structure must always be within the carrying capacity of the rocket that’s to launch it to orbit.
Redefining Satellites with 3D Printed Components
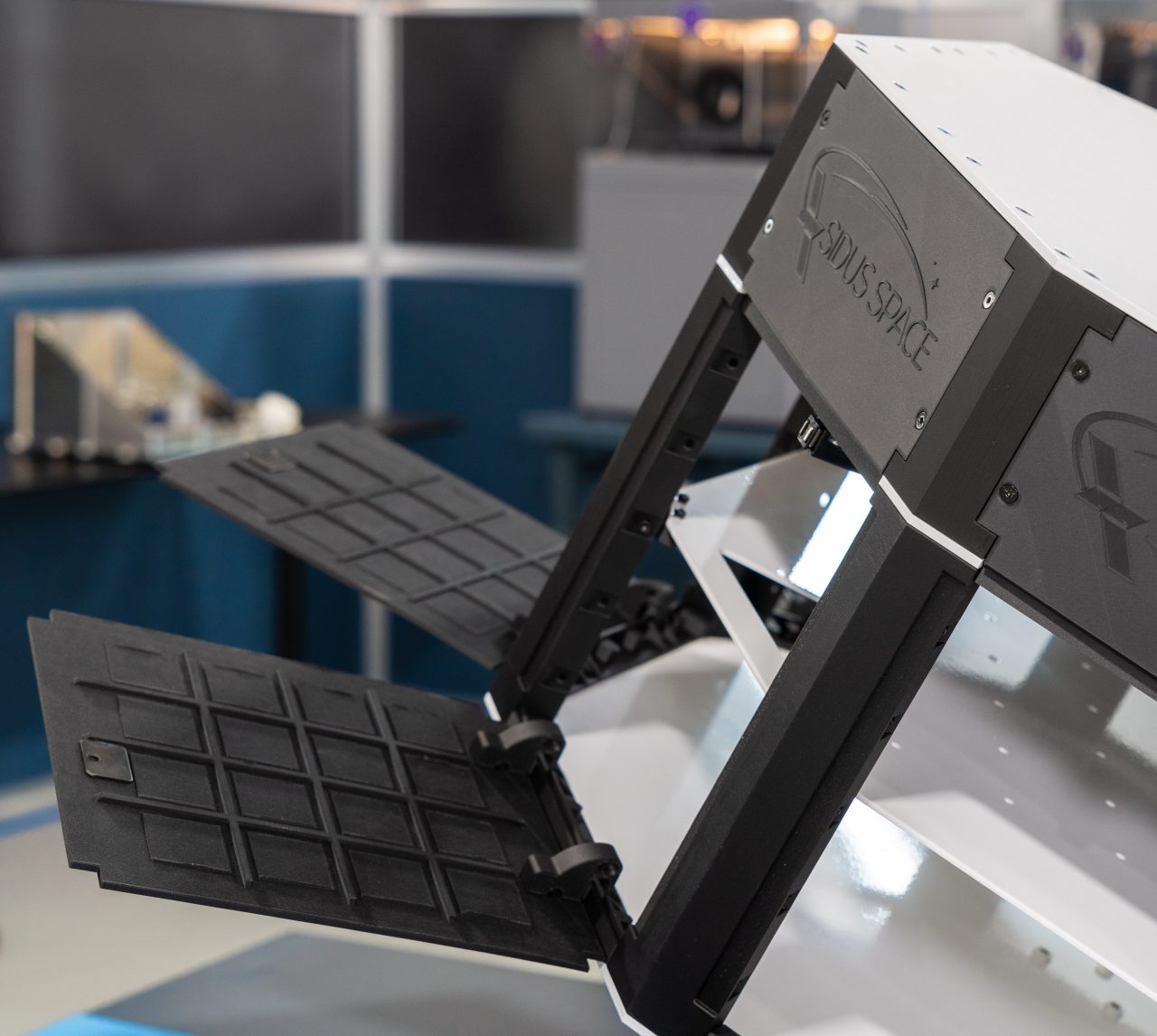
Sidus Space designed a satellite that addresses these challenges by replacing many of the metal components with 3D printed polymer equivalents. They made use of Markforged’s Digital Forge Platform to 3D print major components using the company’s Onyx FRA material, a polymer providing sufficient strength and thermal resistance. In addition, they used Markforged’s nylon Onyx, which includes continuous carbon fiber reinforcement.
These strong components were used to create major portions of the new satellite, which is now significantly lighter than a metal equivalent. Evidently, Sidus Space was able to save even more weight by eliminating many bolts and fittings by designing the parts to snap together. That’s something you cannot do as easily with metal components.
The Impact on Space Design and Future Applications
This project could be a milestone in space design, using additive techniques for a considerable portion of the parts. We’ve seen this approach previously with Relativity Space’s wholly 3D printed rocket, Terran-1. The approach enabled that company to implement many similar design advances. Perhaps Sidus Space was inspired by Relativity Space’s approach?
Either way, the future could see an increase in 3D printed satellite components. If it is demonstrated that this approach truly works when the satellite flies, we could see the use of 3D printed satellite designs become widespread. This development would undoubtedly lead to lighter, more efficient, and cost-effective satellites that could revolutionize the space industry.
Via Markforged