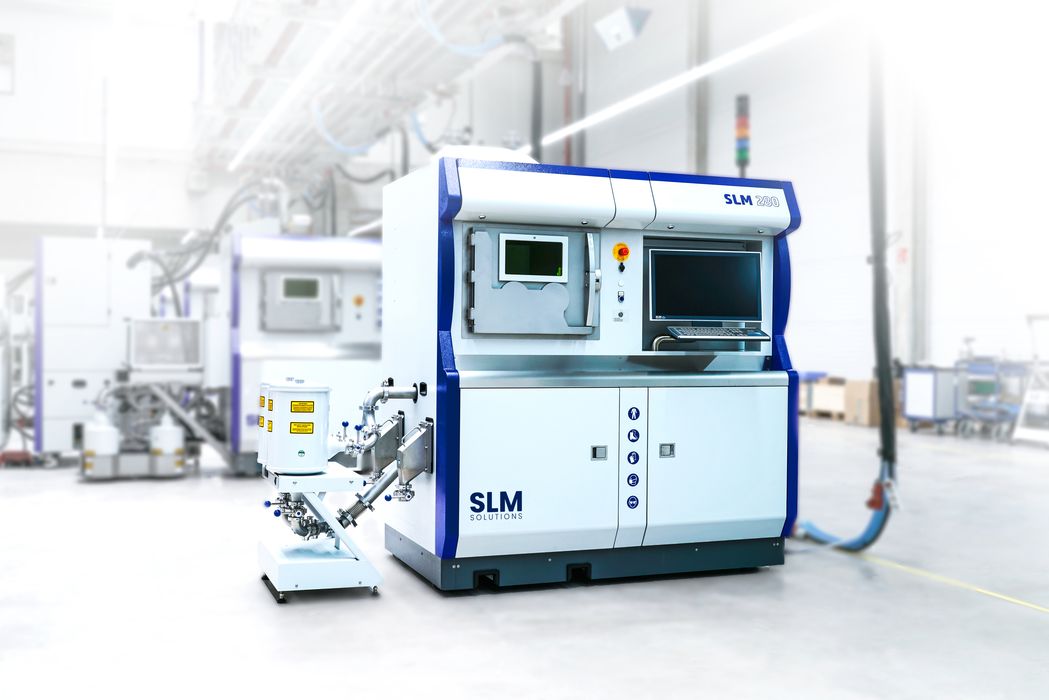
The battle for metal 3D printing supremacy continues, with an interesting move from SLM Solutions this week.
Metal 3D printing is one of the biggest growth areas in the additive manufacturing industry in recent years. It all began with a major breakthrough in the aerospace industry some years ago, when it was clearly demonstrated that better, more radically-designed parts could be extremely effective in aerospace applications.
That has led to vastly increased levels of AM adoption in the aerospace industry, and the attention is washing over other industries as well.
Challenges in Metal 3D Printing
That’s all good news for metal 3D printer manufacturers, which are set to sell many more systems to new clients as a result of the increased interest.
However, there’s a problem: as new industries continue to get involved, there are new challenges in materials and print quality due to different industry and application requirements.
This requires significant investment by operators to identify the optimal print parameters for their specific application, and that’s challenging. Not only is it technically challenging, but it’s also HR challenging because it’s hard to find staff that have sufficient expertise to do so.
Simplifying the Path for New Metal 3D Printer Operators
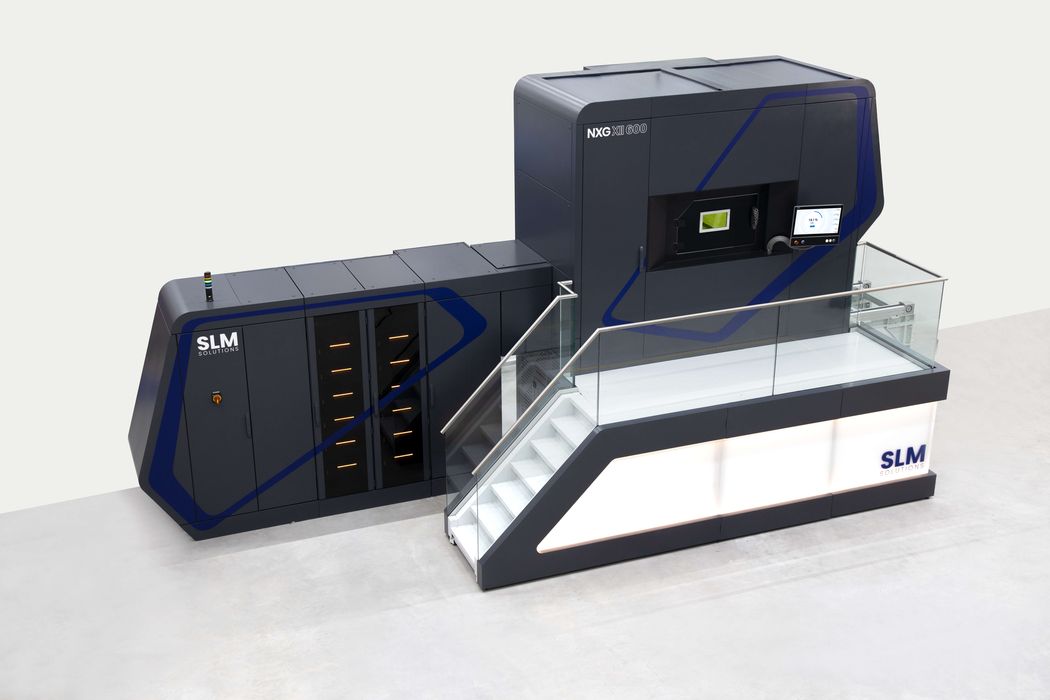
Because of this tension some metal 3D printer manufacturers have been working on methods of simplifying the path for these new customers.
One was seen earlier this week, when EOS announced their new Smart Fusion system that can apparently tune their equipment in real time.
Now there’s another approach, this time by SLM Solutions. They announced an important partnership with the Danish Technological Institute. The intent of the partnership is to develop “outstanding” print parameters for using SLM Solutions’ equipment with selected metal materials.
Developing Parameters for Popular Materials
Specifically, the DTI will work developing parameters for 316L stainless steel and CuCr1Zr copper alloy, two very popular materials. SLM Solutions explains:
“With their recently acquired SLM®280 2.0, DTI is developing faster process parameters for stainless steel 316L and copper alloy CuCr1Zr to support cost-effective production, taking advantage of SLM Solutions’ importance of open architecture. The material development collaboration will create new application opportunities for advanced components, where electrical and thermal conductivity are crucial, and sturdy components out of stainless steel can be manufactured with lightning-fast processes.”
Interestingly, this work will not just increase print quality and reliability, but could actually open up new potential metal 3D printing applications. SLM Solutions explains:
“The development allows the copper alloy CuCr1Zr to be printed in varying layer thicknesses and creates new business cases where AM will be used for advanced components where electrical and thermal conductivity are important. With up to 92 % IACS after heat-treatment, CuCr1Zr still features very high electrical conductivities at up to 300 MPa ultimate tensile strength. SLM Solutions’ stainless steel 316L, on the other hand, is an austenitic high-chromium steel with excellent processability on SLM Solutions’ additive manufacturing machines. 316L is often used in applications requiring good mechanical properties and excellent corrosion resistance, especially in chloride environments. DTI will develop faster process parameters for stainless steel 316L, enabling the possibilities of printing components at a lower price.”
Improved Environment for Metal 3D Printer Customers
The result of all this is that metal 3D printer customers could find themselves in an environment that is quite a bit easier to work within, and at the same time producing better parts for more applications. All good news, especially for those operating the gigantic SLM Solutions NXG XII 600 metal 3D printer.
Via SLM Solutions