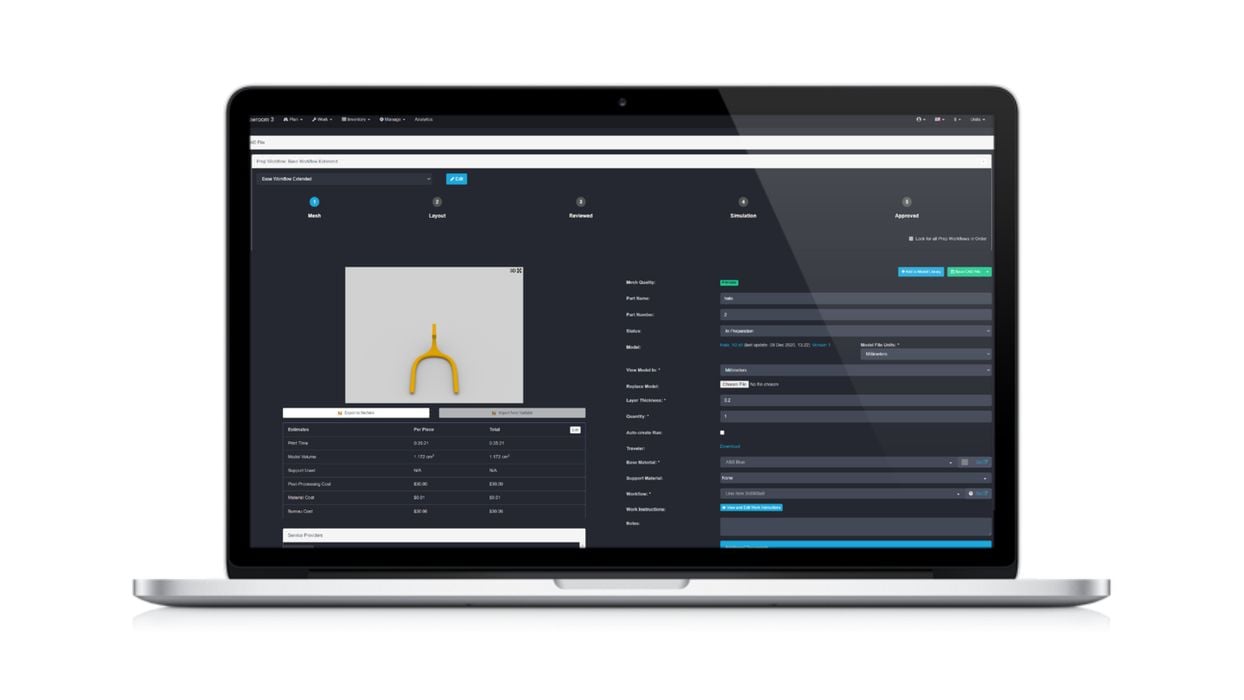
Authentise announced a new “RFQ Responder” feature for their ever-expanding additive manufacturing workflow system.
The Philadelphia-based company has been developing a highly sophisticated workflow system that can provide a variety of functionality for additive manufacturing operations. Their “Flows” system is capable of accepting orders, planning production, maintaining a parts library, dispatching work, monitoring results and reporting on quality control.
The system operates within a complex set of rules that can be specified by operators.
Why have such a system? It’s essential to those using 3D print technology for production, because the game is to keep those machines running as much as possible to recoup their cost and generate profits. If they’re idle because of paperwork, that’s bad. A workflow system can coordinate all activities together to ensure optimum machine usage.
On the front end of that sequence is the interface with the requestor. Typically customers send in a part design and require a quote for the work to produce it. This is a critical step, because if the quote is too low, effort will be expended for less profit (or even a loss) in subsequent steps in the workflow. If the quote is too high, then the customer might head elsewhere.
That’s likely the reason why Authentise decided to implement a new feature, the RFQ Responder.
Authentise explains how it works:
“With RFQ Responder, teams can quickly gather full requirements through configurable interfaces for both customers and staff. It provides key design data and prices automatically as a baseline, which can then be adjusted based on templatized workflows and Authentise’s unique Guideline recommendation engine. It is the additive industry’s only tool that can do so for assemblies. The baseline can be edited collaboratively by a team to identify the right technology and production process, communicating through chat and tracking tasks in the Pre-Production Workflow Manager. In doing so, they can build on historical experience through both the Build and Model Libraries. The resulting quotes are easily configurable to allow work items to be hidden, discounted, or excluded.”
As you can see, responding to a quote is not a simple matter. One might think that it would simply be the case to analyze the part geometry & material, and then compute the cost. But there are far more complexities to the equation, and that’s where Authentise’s solution shines.
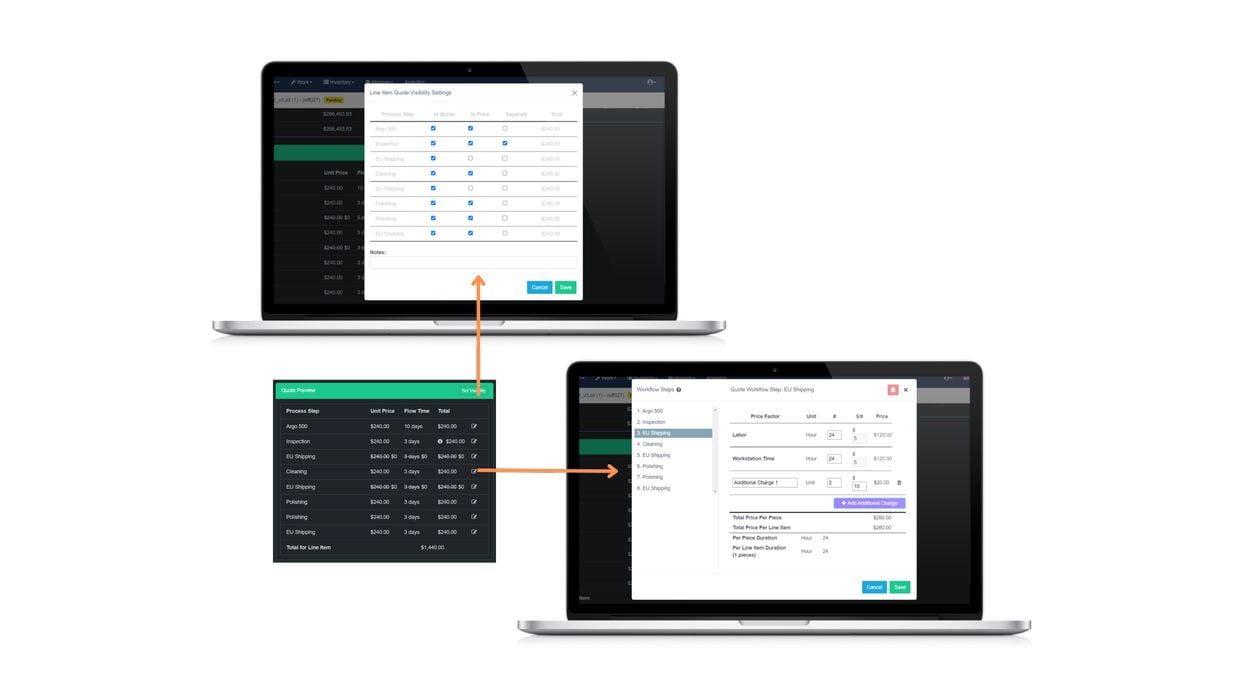
Authentise CEO Andre Wegner explained:
“Responding to RFPs for complex parts requires collaboration between many stakeholders, especially if they’re moving towards production rate. They’re not quoted in instant online portals. Experts consider a range of factors, not least the standards required in production. This can take weeks. With our recent release of Guidelines and the collaboration and quoting tools previously only available through Flows, we’re in the prime position to help make companies more reactive to incoming inquires. We’re delighted to bring this third spin-off product from Flows to market, next to Materials Management and the Digital Design Warehouse.”
Of particular interest is its ability to handle assemblies of parts. Customers certainly desire the assembly, not a pile of parts. The RFQ Responder treats them as an assembly, and that’s the right way to do it.
Of course, the RFQ Responder integrates directly into Authentise’s Flow workflow system, making the entire process more complete.
Companies like Authentise are paving the road ahead of the increasing number of additive manufacturing operations that will be building our future.
Via Authentise