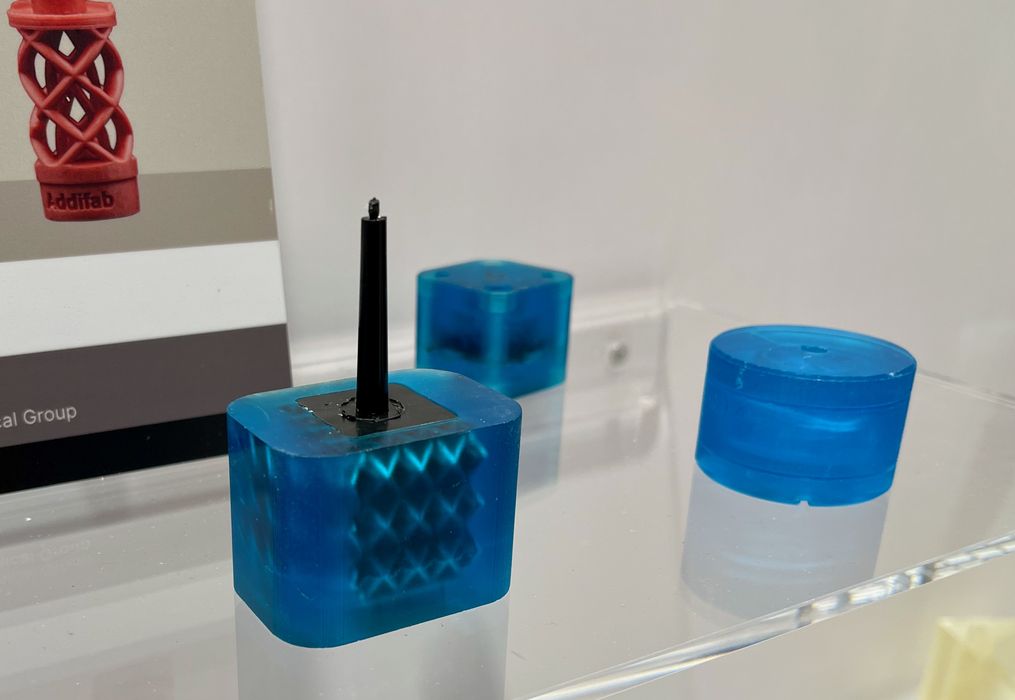
I had an interesting conversation with AddiFab recently, and it pointed out what might be a new trend in 3D printing.
AddiFab’s Unique Method for Dissolvable Molds
AddiFab is the producer of a unique system that involves a multi-step printing process. The idea is to 3D print a dissolvable mold, into which is injected almost any standard injection molding material. The mold is then dissolved, revealing a part that’s made from everyday materials.
The trick is that the geometry of the part can be extremely complex, which isn’t allowed in the normal injection molding process. Typical injection molds require draft angles, no embedded structures, and a clear way to remove the part from the mold.
That drastically constrains the geometry of parts, and is one of the main reasons 3D printing became popular: it doesn’t have such geometric limitations.
However, most 3D printers are pretty severely constrained in the types of materials they can use. Some machines are even locked into proprietary materials catalogs from machine manufacturers, but even those with “open materials” equipment find there isn’t all that much choice in materials.
The story has been getting better. When I got into this technology 16 years ago, the choice was basically “what color of ABS would you like? White, Black, or Beige?” Nowadays there is far more choice, and you can get ABS in many different colors.
There has been an effect on 3D print usage, however.
A Growing Desire for Production-Ready 3D Printing
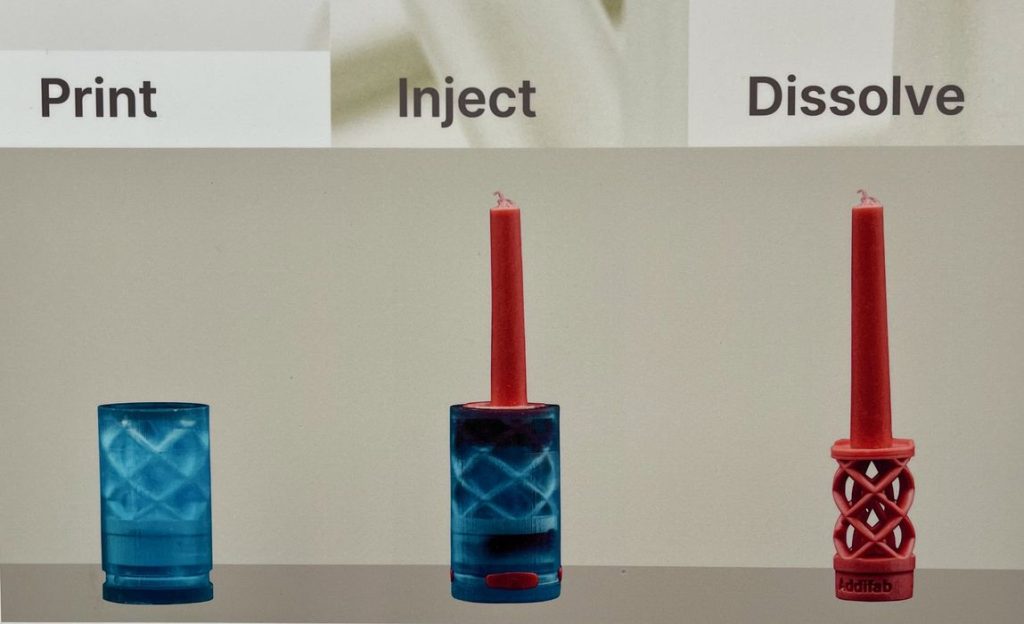
Because of the material constraints, engineers frequently found the ideal material for their end-use production part was not available for 3D printing on their equipment. This left them with the option to 3D print fragile prototypes that basically allowed look & feel and fit testing. Later they’d switch to the “real” material when going into full production.
That’s the typical part prototyping sequence that’s gone on for decades in 3D printing.
But in my conversation with AddiFab, CEO Lasse Stahl said something quite interesting:
“Customers are getting tired of test parts, they need real parts.”
That is a dramatic statement, and might indicate a new trend. It would seem that at least some 3D printer operators, having been given a slim taste of some production materials, want a lot more choice. It may be that the general acceptance of lousy materials over the past many years could be fading.
That’s good news for AddiFab, which provides a system where material choice is basically about as wide as injection molding itself. In fact, they’ve recently made an arrangement with Nexa3D to use the AddiFab system on Nexa3D equipment. Staal told me that this has been a “game changer” for AddiFab, as some Nexa3D customers are adding equipment just to gain access to the AddiFab technology.
But this trend may go beyond just AddiFab.
It may be a silent message to materials providers and 3D printer manufacturers to get more materials certified on their equipment, and fast.
That’s generally happening, but it’s at a relatively slow pace and is greatly hampered by the lack of interoperable print profile definitions, which tend to be walled gardens these days.
We will get more material choice eventually, however, as more become aware of this emerging trend.
Via AddiFab