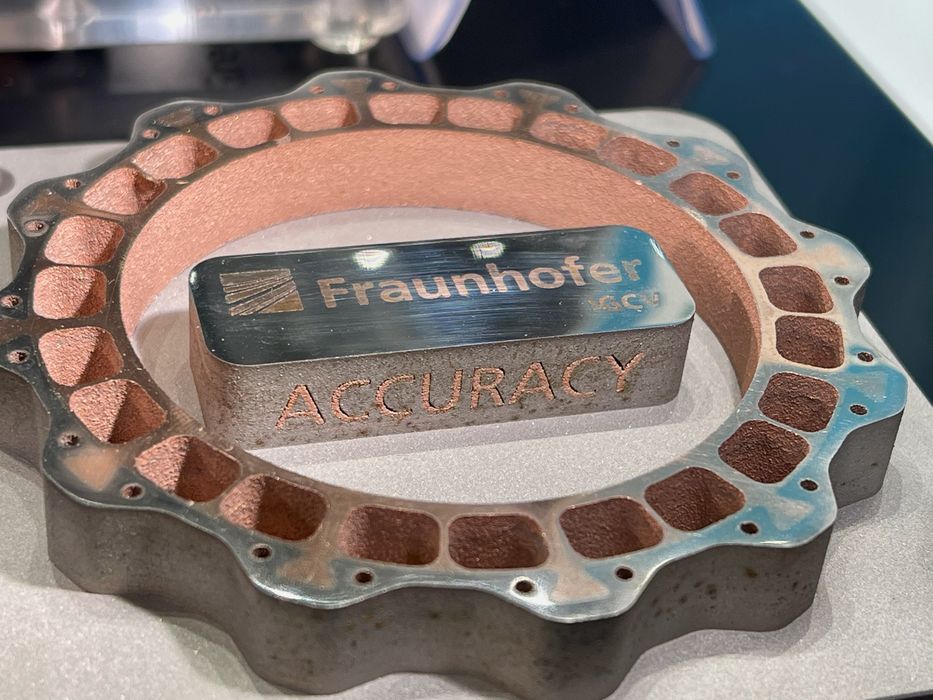
Our post describing a new approach for multimaterial powder recoating generated some discussion.
The post was triggered by a discussion at Formnext with Fraunhofer IGCV researchers who have developed a way to perform multimaterial recoating within powder-based 3D printing processes. Normally, recoating is simply a blade pushing a pile of homogenous powder across the print surface, so only one material is possible.
This is why virtually all powder 3D printers are “monomaterial”, be they metal or thermoplastic.
The only exception to this is Desktop Metal’s Aerosint technology, which can selectively deposit a handful of different metal powders, enabling multimaterial SLM prints.
The Fraunhofer IGCV approach uses electrostatic forces to selectively pick up powder onto a plate, which then when positioned over the opposite-charged print surface, releases the powder. This process can repeat with a number of different powders to fill out the layer with multiple materials.
Bill Steele contacted us via Twitter about this development. Steele, if you don’t know, is an early explorer of “infinite-Z” belt 3D printers, and in 2014 launched a Kickstarter for the Ultra-Bot 3D printer.
Steel pointed out that this is not new, having been patented by GE back in 2015.
But looking at that patent shows an electrostatic recoating system that uses a rotating drum, much like you’d see on a photocopier or laser printer. The electrostatic part is pretty much the same, but the delivery is different: drums versus plates.
I believe the plate approach would be notably slower, but also more flexible. It would be substantially easier to organize a system with a much larger number of materials using plates than it would with a high speed drum system. It would be a tradeoff between material choice and speed, but there are no doubt applications that would make use of such a system.
Bram Nerick, Manager of Sintered Application at Aerosint, pointed us to a paper at ACS, of which he was one of the authors.
The paper, entitled “Powder Deposition Systems Used in Powder Bed-Based Multimetal Additive Manufacturing”, which reviews the issues surrounding multimaterial powder deposition. The paper provides an objective survey of the state of the technology for a variety of approaches, including:
- Split recoater blade & vacuum system to deliver two different materials
- Selective powder deposition using pipettes
- Electrostatic selective deposition
- Selective deposition for single material processes
- Drum-based selective powder deposition
The latter is the approach used by Aerosint, which apparently doesn’t use electrostatic forces. The paper explains:
“The drum-based recoater system as developed by Aerosint is another selective powder deposition with some similarities to traditional printing technology. Compared to Sintef’s ap- proach, the Aerosint selective powder deposition system is based on purely mechanical forces to hold the powder on the drum and subsequently release it at the desired location.”
This is an excellent paper if you want to get a quick understanding of the several different approaches that have been investigated by researchers. The paper concludes:
“The research in multimetal L-PBF has long been dominated by a small number of groups due to their efforts in developing systems allowing selective deposition of multiple powder in a single powder layer. Most of these groups also developed their own approach for using multiple metal powders in a single AM machine. These solutions have recently been joined by the first commercial, but still R&D focused, multimetal platform. Each of these multimetal approaches has its own strong and weak points, which we tried to discuss objectively in this paper. To decide which of these are critical for real life multimetal parts to become a commodity, extensive process and materials research is needed.”
Needless to say, the work undertaken by all of the above will at some point enable the widespread use of sophisticated multimaterial powder-based 3D print systems for both polymers and metal materials.