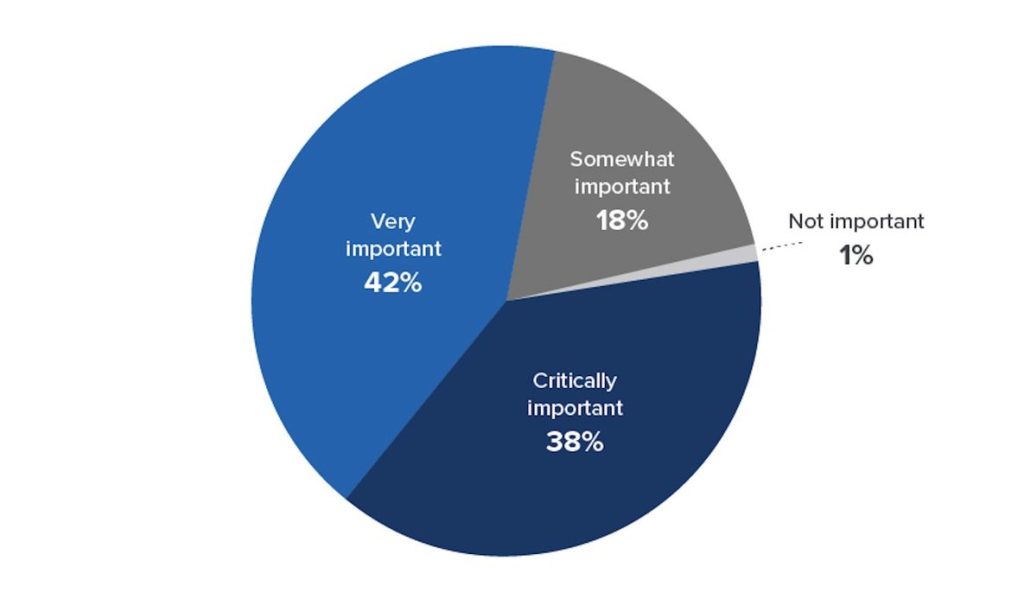
Essentium released the 2022 edition of their annual additive manufacturing survey.
The company has long focused on industrial 3D printing, and their annual surveys show them what their clients and prospects could be thinking. This helps not only Essentium, but everyone else in the additive manufacturing business understand how to direct resources and strategies.
There were many findings in the report, but a few stick out as fundamental in my view.
One is that it now appears that additive methods have taken a firm place with many manufacturers. For a long time AM was considered an “experiment” or “side thing”. Now, that’s no longer the case. Consider the responses to the question of usage of the technology:
- Manufacturing aids and tooling [74%]
- Complex and integrated prototyping [52%]
- Full production runs [44%]
Let’s put this in perspective: three quarters of respondents were using AM for production of jigs & fixtures. We all knew this was an important use case, but it now seems that the vast majority of respondents are doing so. It’s perhaps become a standard approach.
Also note the significant number of respondents that were doing full production runs, almost half. This is also quite significant, as for many years AM was considered a prototyping technology. That’s clearly not the case now, and at least half of these manufacturers know it well.
Another surprising finding is that apparently 80% of respondents deemed the certification of materials for production to be “very important” or “critically important”, with the latter hitting a huge 38%.
This is quite important for the materials industry and 3D printer manufacturers, as “production” is where the bulk of material sales will take place. With this finding, it’s clear that if you want your material to be considered in the lucrative production space, you’d better be certified.
I expect this finding alone will drive a considerable amount of material certification in the coming months and years. Ultimately, it may be that ANY material to be used on production-class 3D printers should be certified.
Apparently one third of respondents said their organization has become “more open to change and innovation” as a result of exposure to additive technology. This is not too surprising because the technology quite literally opens up many doors for new and innovative design. However, the cultural effect on companies is very significant.
Many manufacturers are “steady state” operations where change happens slowly. That’s one reason progress in society is not always rapid, but evidently AM usage is able to break down that barrier. It may be that we see a surge of new and innovative products in coming years simply caused by culture change.
Regarding which areas require more work in AM, respondents focused on two disciplines: post processing and software, and both were higher than materials and printers.
It seems that the raw technology is now considered “good”, and the focus is on scaling up. It’s easy to run a single 3D printer, but far more difficult at scale: the labor required for post processing is significant, and now manufacturers recognize this. In addition, the paperwork required to properly track, dispatch and control AM work requires sophisticated software that is of equal importance.
Expect new innovations in post processing and software to not only speed up operations, but also integrate manufacturing steps together to create more optimal processes.
Via Essentium