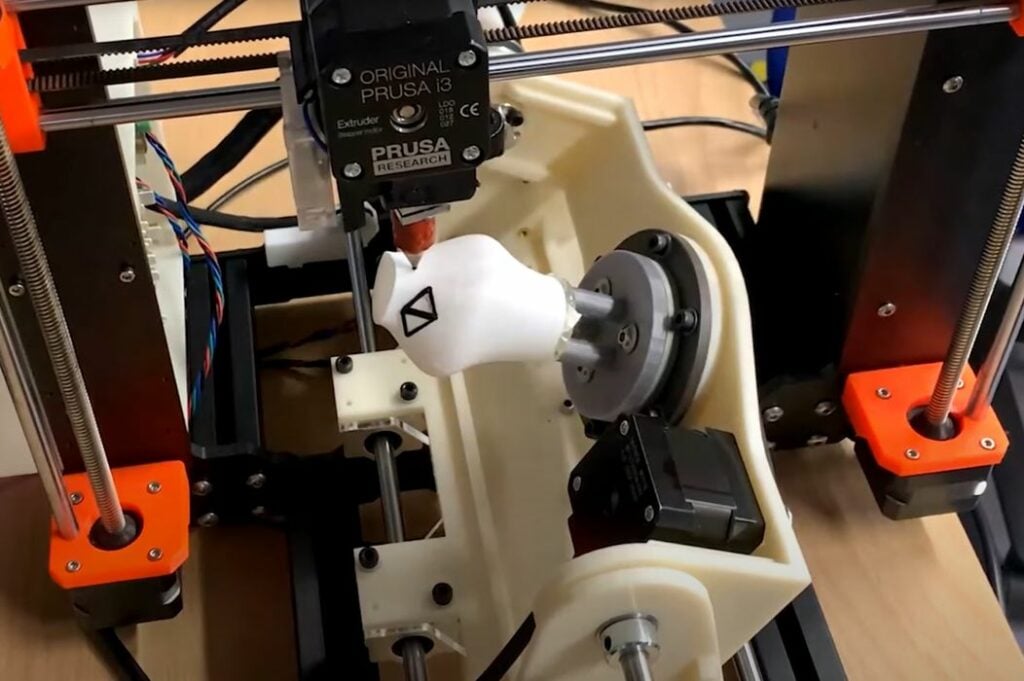
An open source version of a five-axis 3D printer design is being developed, and could soon take off.
The dream of five-axis 3D printers has largely been unachievable for years, with very few exceptions. A small handful of manufacturers have produced five-axis 3D printers, but their cost is far, far beyond affordability levels of casual users and even small businesses.
The reason for the attractiveness of five-axis 3D printing is clear: it eliminates the need for support structures.
Most of today’s FFF 3D printers operate in a standard cartesian three-axis form. The print is produced in 2D X-Y layers that are stacked on the Z axis. This means there are often scenarios where overhangs require support from underlaying layers. The resulting support structures consume both material and labor as they must be removed after printing. They also tend to mess up the surface texture where they attached to the print.
Five axis 3D printing is different. Imagine a three axis 3D printer with two more axes of movement. The print could be, for example, rotated during printing.
This capability means it would be possible to turn an overhang upside down so that the overhang no longer exists at that moment during extrusion.
There’s another benefit, called “conformal deposition”. This is the process of depositing lines of polymer along the contours of the object in 3D paths rather than the usual 2D paths. This, if the toolpath is devised properly, can dramatically improve the surface quality and strength of a 3D printed object.
That may sound easy, but it’s most definitely not. The motion control is vastly more complex in five-axis 3D printing. Watch this video to see the Open5x system in action and pay attention to the movements:
You’d need a some very smart people to figure out how to make software drive five axes in such complex paths, and that’s exactly the situation here. Freddie Hong and his team at University College London published a paper on Open5x that is publicly available. Hong, a holder of a Masters degree in Computational Art, is an artist and researcher based in London with a clear interest in 3D print technology.
The paper describes how the team gutted a stock Prusa i3 3D printer and fitted it with a Duet controller with RepRap firmware and new mechanical components to implement two additional axes.
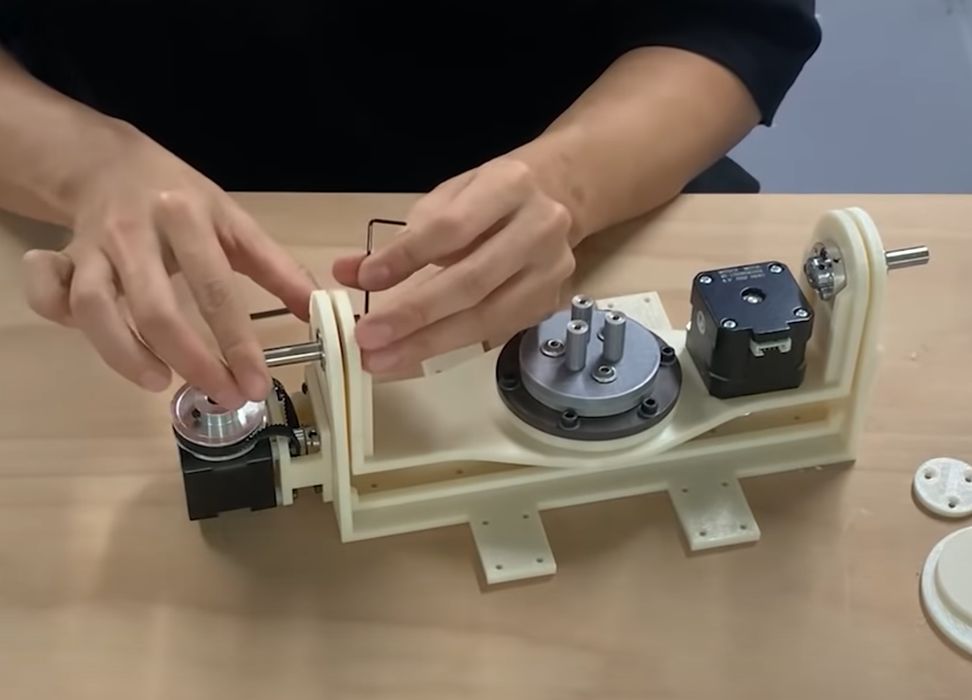
To prepare the highly unusual GCODE tool path required for the adapted 3D printer, they used Rhino’s Grasshopper scripting tool to generate the GCODE using a complex configuration. However, this meant that with a single environment, Rhino, an operator could not only design a 3D model, but also slice and produce five-axis GCODE. However, it sounds like the project intends to eventually create a specialized standalone software slicing tool.
The slicing code is quite complex and the mathematics behind it is even more complex. You’ll have to read the paper to gain a fuller understanding of it. Nevertheless, having created the scripts, they describe the software as now being “accessible” to the majority of operators.
The concepts outlined in the paper live on in the Open5x open source project, which is housed at GitHub. There, one can download the hardware plans and software, or even contribute to the project in different ways, all at no charge.
By no means is this project finished, it’s still at the early stages and there are plenty of issues and features yet to be developed. Here is a video showing the current state of the system and how to build the additional two axes:
This past week the Open5x prototypes were shown at ERRF, which will certainly raise the profile of this project significantly. It’s likely to attract a number of new players to the project and possibly provoke commercial activity.
Up to now the mysteries of five-axis 3D printing have been legend, kept within the walls of big companies that have been leveraging that knowledge in the marketplace. Now those walls could be broken down with the near certainty that the open source Open5x concept will be leveraged into purchasable products in the future.
Five-axis 3D printing for all!
Via Arxiv (PDF), GitHub and FreddieHong