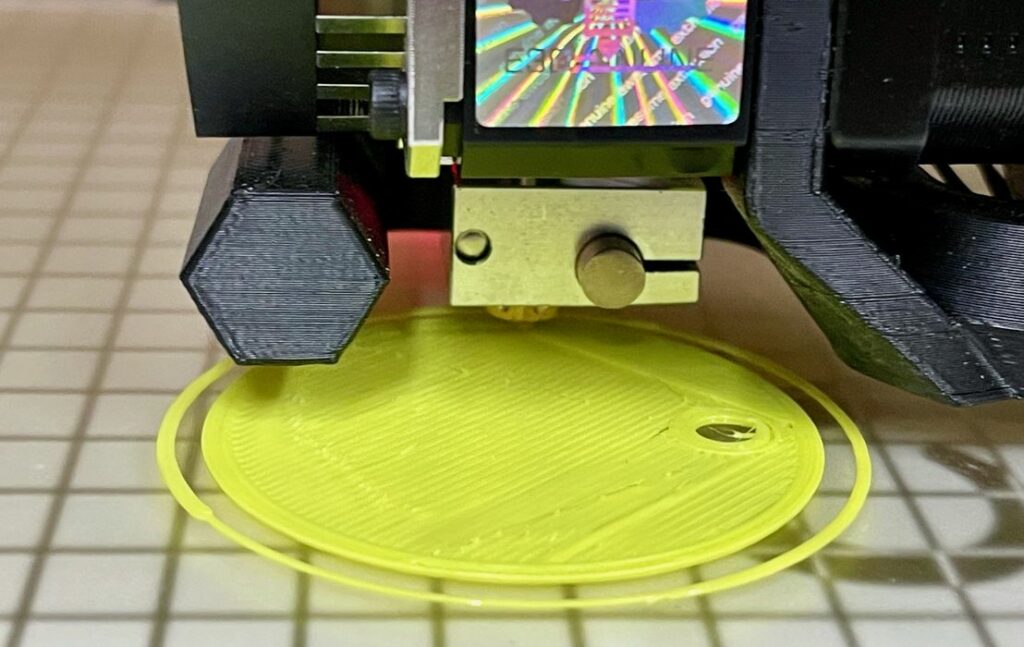
Frequent readers of this publication likely know quite a bit about 3D printing, but there are new readers that could use some more basic information about the technology.
This post is for those readers, and will provide a very basic introduction to the current state of 3D printing.
3D printing is a relatively new method of making objects, and it comes today in many forms.
3D Printing Concept
Most people are familiar with the notion of making something, but usually that’s with what we could term “subtractive technologies”. These are making methods that remove material to “reveal” the desired object.
Examples of this are sawing, drilling, sculpting, etc, where you’re taking away material.
3D printing is the opposite. Instead, you start with absolutely nothing and add material to form the object, much like building a structure out of bricks.
This is why the technology is also referred to as “additive manufacturing”, but that term tends to be used mostly for industrial applications.
3D Printing Benefits
Why use additive instead of subtractive techniques? It turns out there are multiple advantages in doing so.
First, you’re adding material, so there is far less wasted material. Imagine a chunk of expensive titanium metal, and you carve away 70% of it to get your object. That’s a significant waste of material, and that doesn’t happen in 3D printing.
Another major advantage is that you can build objects in any geometry (“geometry” in this world means the “shape” of the object.) Many conventional making processes have severe constraints on what you can build because you’re coming at the material “from the outside”, rather than building bit by bit. Injection molding has similar but different issues: the geometry must be able to be released from the mold.
Finally, another advantage is that a 3D printer can print any design sent to it immediately. This is very different from conventional manufacturing where it can take weeks or months to set up a production line. Meanwhile, 3D printers can print right away without the need for significant setup.
3D Printing History
You might be surprised to learn that 3D printing that we use today first appeared back in the 1980s. Then two companies, Stratasys and 3D Systems, invented the basic two processes: FFF and SLA, respectively.
FFF, or fused filament fabrication, involves heating a filament of thermoplastic until it is soft, then squeezing it out in strands layer by layer to build up an object. Most desktop 3D printers of today use this process.
SLA, or stereolithography, involves firing a laser at a vat of liquid photopolymer resin that solidifies when it absorbs enough energy. By aiming the laser precisely, it’s possible to build objects layer by layer.
Current 3D Printing Processes
While those were the two initial 3D printing processes, many more have been developed since.
In fact, there are so many unique processes it’s hard to list them all, but it’s important to know that each has advantages and disadvantages. The result is that engineers must select the right 3D printing process for the job.
Current processes can use materials that are solid, liquid or powder. Materials include thermoplastics, thermosets, concrete, metals, ceramics, food and even living cells in some cases. However, for each you must select the matching 3D printing process and printers.
Problems With 3D Printing
Some may believe 3D printing is like the famous but fictional Star Trek replicator, but they’re nothing like that. While objects do literally appear out of thin air, there are issues.
In spite of the numerous 3D printing processes, there are still significant constraints on the types of materials that can be printed.
The duration of 3D print jobs can be quite long. For printing a fist sized object, it can take several hours. It’s not uncommon to have jobs take more than a day or two to produce a single large object. That can be too slow for production needs.
Most 3D printers of today can print objects in only a single material. A few can print in different colors and some with maybe two or three different material types. When the technology advances to truly allow mixing of unlike materials, many more applications will be enabled.
The cost of 3D printing can be excessive. While the cost of plastic for printing small items can be low, it’s far more expensive to produce metal objects, or those in unusual engineering materials. The cost of metal powder for 3D printing can be hundreds of dollars per kilogram, and the equipment can cost much more. The extreme costs of some types of 3D printing have relegated the use to prototyping, low volume production or production parts for expensive industries like healthcare or aerospace.
Users of 3D Printing
What companies make use of 3D printing? While the list always grows, here’s most of the basic user categories:
- Bioprinting of living cells for research or healthcare applications
- 3D printing of scanned human organs for education or surgical simulation and training
- Printing of lightweight aerospace parts
- Temporary replacement parts when normal suppliers can’t deliver
- Hobby items, like plastic dragons, household items, etc.
- Engineering prototypes
- Low volume production of items that can’t justify mass production approaches
- Human implants, like hip cups or bone replacements
- Customized apparel, like eyeglasses, shoes and fashions
- Artwork and sculptures
- Architectural elements to be affixed to a building
- Large concrete structures, including homes — but only the concrete parts
- Parts with embedded electrical wiring
And there’s much more. Basically anything that can’t be made using other processes, or items in low volumes, and especially customized items that fit an individual are all likely candidates for 3D printing applications.
The Future of 3D Printing
As we continue into the future, it’s very likely we will see new 3D printing processes emerge with more powerful capabilities.
New processes will inevitably allow use of more types of materials, multiple materials, faster printing and lower costs.
One technology to watch is called volumetric 3D printing, where a vat of photopolymer resin is subjected to reverse CT scan images. This causes the object to appear in the vat in only seconds or minutes. There are no printers on the market doing this quite yet, but several are under development.
It may be that at some point in the future there will be so much 3D printing taking place that we will all assume that items we purchase will be perfectly sized for our use, as opposed to today’s assumption of a few sizes to choose from.