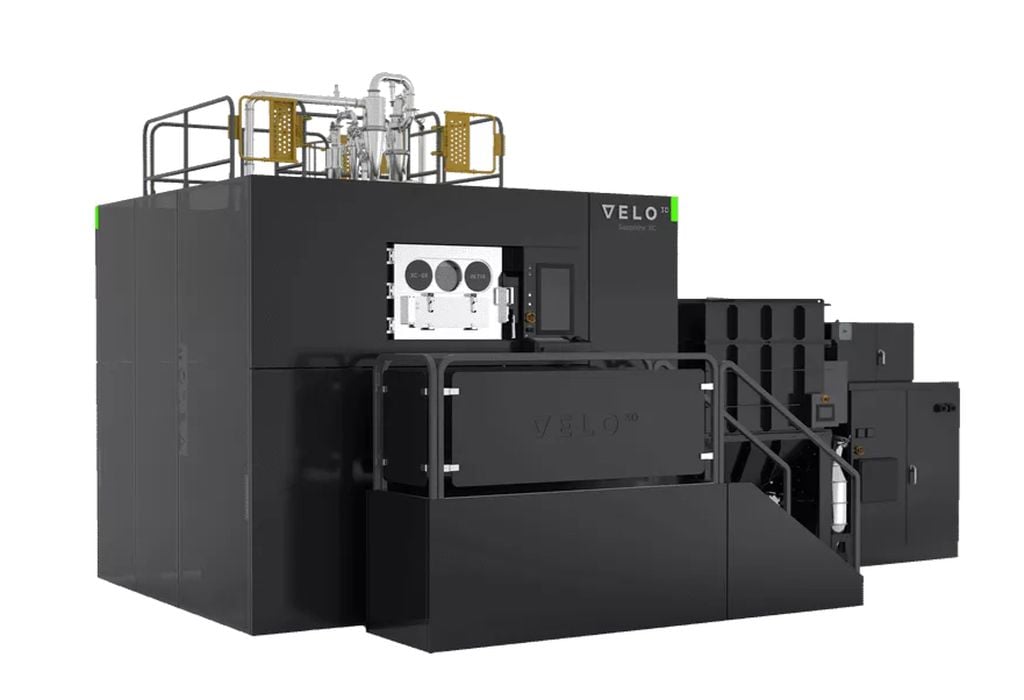
Velo3D announced a new 3D printer, their largest: the Sapphire XC 1MZ.
This complements their existing three models, the Sapphire XC, Sapphire 1MZ and original Sapphire. Velo3D perfected their technology with the original device, and then propagated it to the newer models.
Their technology is quite interesting, although at first it may seem they produce just another powder bed laser metal 3D printing system. The difference is that they have significant real time closed loop melt pool controls that tighten up all the operational tolerances, resulting in greater quality and reliability. There is also sophisticated simulation software that can assist in ensuring prints will succeed.
The other key part of their metal 3D printing technology is a unique recoating system that is termed “no contact”. This prevents the recoater blade from accidentally impacting the partial prints, and therefore increases job reliability.
The combination of all this technology is a metal 3D printing system that can do things no other metal 3D printer can do: successfully 3D print fine detail metal objects with little or sometimes no need for support structures.
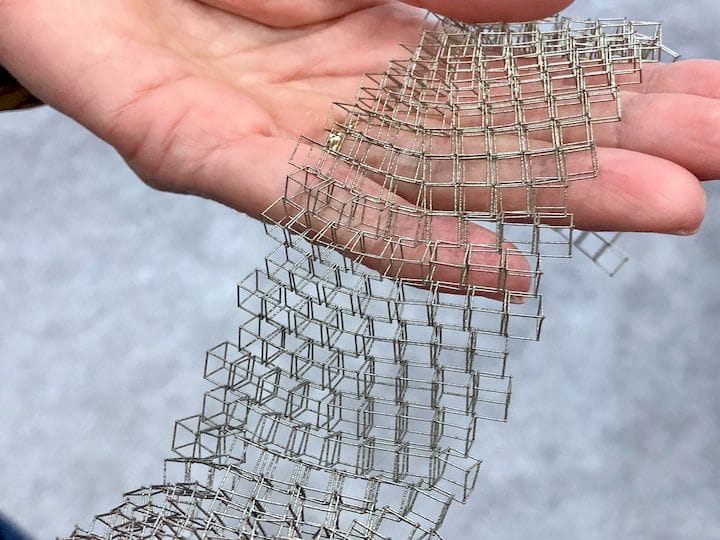
That is a considerable advantage, because it simplifies thermal analysis required for support structures, as well as eliminating the vast amount of tedious post processing required by other systems.
While this technology is quite desirable, the initial knock on Velo3D was that their build volume was a bit small, at only 315 diameter by 400 mm tall (Velo3D uses a cylindrical build volume).
That was solved when the company introduced their Sapphire 1MZ 3D printer, which simply took the original build volume and extended it. Well, I shouldn’t make it sound so straightforward, as there were challenges for Velo3D. This announcement allowed Velo3D to address customers requiring longer parts.
The company then announced a wider version of the system, the Sapphire XC. This device has a build volume of 600mm diameter and 550mm in height. This announcement allowed Velo3D to address customers with bulkier parts.
Now we turn to the new Sapphire XC 1MZ, which as you might suspect from the product name, is a stretch version of the wide-body Sapphire XC. The Sapphire XC 1MZ has a build volume of 600mm diameter and a full 1m height. And yes, they can now address customers requiring bulky and tall parts in a single machine.
The Sapphire XC 1MZ is able to use all of the metal powder materials available to other Velo3D equipment, including: Aluminum F357, Amperprint 0233 Haynes 282, GRCop-42, Hastelloy C22, Hastelloy X, Inconel 625, Inconel 718, Scalmalloy, and Titanium 6AI-4V Grade 5.
This is quite important for the company in my opinion, as it literally opens up additional markets. There are manufacturers that produce parts that simply won’t fit into any of Velo3D’s prior devices. In spite of the attractiveness of the Velo3D process, these potential clients cannot use Velo3D equipment.
Until now.
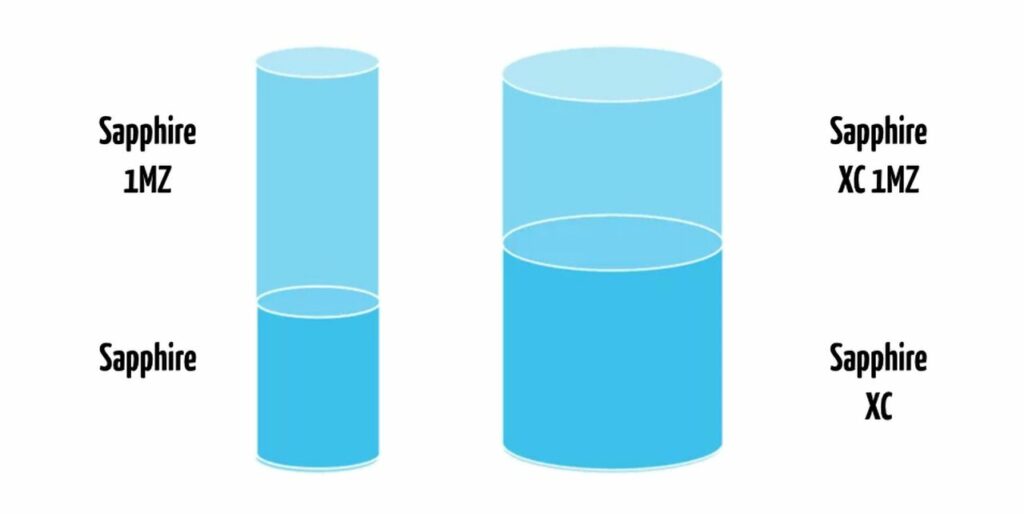
The Sapphire XC 1MZ will instantly turn on a new batch of potential clients that have been waiting for an opportunity to use the technology.
Readers may recall that Velo3D has been having some difficulties in their valuation over the past year. As seen on our weekly leaderboard, Velo3D’s value has been consistently dropping week after week, in spite of their sophisticated technological solutions.
I’m wondering if the new machine announcement will have an effect on Velo3D’s valuation, as it should directly increase their potential market in a big way.
Via Velo3D