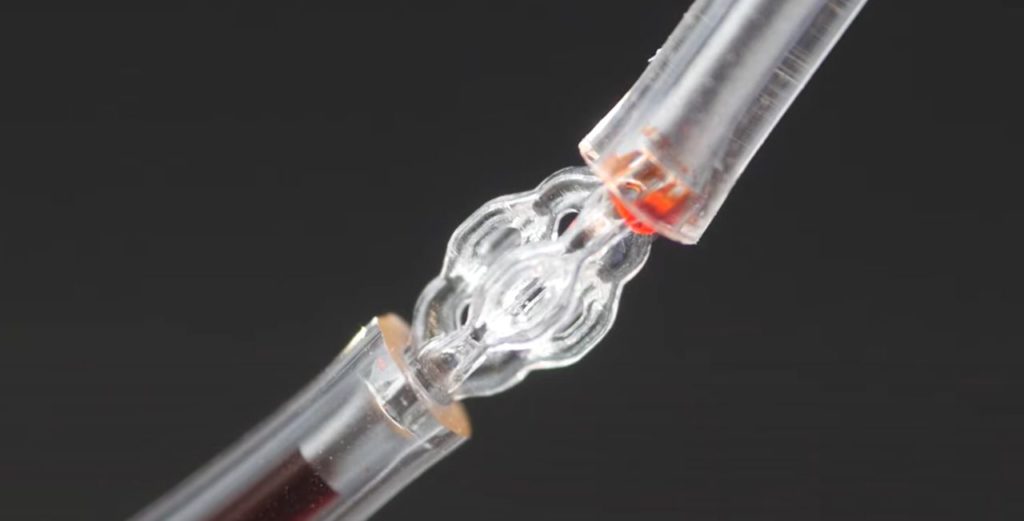
Researchers have found a way to 3D print glass objects almost instantly using a volumetric process.
Volumetric 3D printing is an experimental process currently being investigated by several institutions and a couple of commercial ventures. It is a revolutionary process that destroys the speed barriers of 3D printing by producing objects in only minutes or even seconds.
A volumetric process involves using a vat of clear photopolymer that is tuned to polymerize when a sufficient and predictable amount of energy is absorbed by its molecules. The cylindrical vat spins and is exposed to a digital light projector.
The projection is constantly shifted to a kind of “X-ray” view of the object as if viewed from each rotational position during the spin. Over time the appropriate molecules within the vat absorb the repeated energy exposures and polymerize.
In other words, the entire object literally appears at once; there are no layers as the object grows in all places simultaneously. This process can occur very quickly, hundreds of times faster than conventional 3D printing processes.
We’ve already posted several prior stories on volumetric approaches, of which there are several. Companies developing volumetric products include Xolo and Readily3D.
The latest development comes from the Lawrence Livermore National Laboratory in California, where researchers have adapted their “VAM”, or Volumetric Additive Manufacturing process, to 3D print glass objects rapidly. VAM has been under development for several years at this research facility.
Volumetric additive manufacturing microtubule structure
VAM uses a computed axial lithography (CAL) approach, and the researchers have improved VAM significantly by developing a “micro-CAL”, which apparently offers more intense illumination and at a finer resolution.
The Micro-CAL system was paired with a familiar material: glass resin from Glassomer. We saw this amazing material a few years ago, and the objects produced with it are essentially solid glass. It’s a clear liquid photopolymer resin that is actually made up of 60% glass particles. It can be used as a normal material in MSLA/SLA/DLP 3D printer, but in this experiment was used in the VAM system.
To use the Glassomer resin, one first 3D prints a “green part”, which is a mix of glass particles and solidified resin. This part is then transformed into a “brown part” by removing the binder with a heating process. Finally, the glass particles are fused together into a fully glass object with a final heat application. The Glassomer parts I’ve seen are, to the eye, no different from traditionally made glass objects — except they are 3D printed.
The result is quite amazing, and can be seen at top. They produced a glass object with features as small as 0.05mm, having a surface roughness of only 6nm.
The researchers believe that the low surface roughness will lead to many potential applications for the technology, which could include optical or fluid systems.
Team member Caitlyn Krikorian Cook explained:
“You can imagine trying to create these small micro-optics and complex microarchitectures using standard fabrication techniques; it’s really not possible. And being able to print it ready-to-use without having to do polishing techniques saves a significant amount of time. If you can eliminate polishing steps after forming the optics — with low roughness — you can print a part ready for use.”
While some research may never make it to commercial offerings, I have a strong suspicion that this technology certainly will.
Image by Adam Lau/Berkeley Engineering.
Via LLNL