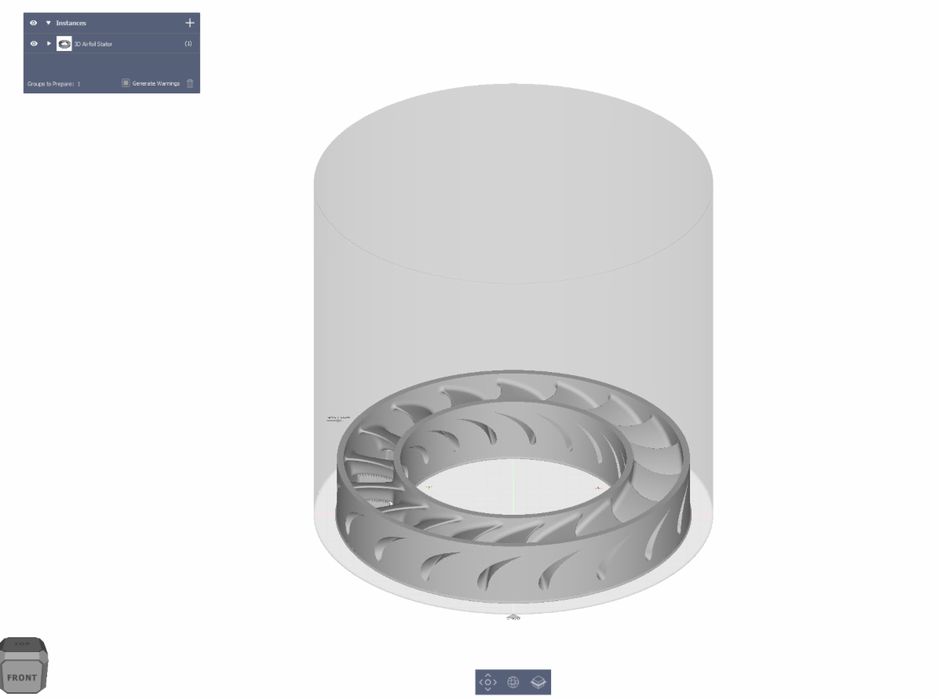
Velo3D announced a new version of their flagship software product, Flow, which happens to include a very interesting DfAM feature.
Velo3D is the producer of high-end metal 3D printers that seem to do the impossible by printing (mostly) without support structures. This was achieved by extreme tuning of their system’s hardware, software and materials.
The software part of the equation is handled by “Flow”, a proprietary software tool designed to prepare and execute print jobs on their Sapphire metal 3D printers. Like most 3D print management software tools, Flow will “slice” a 3D model into layers that are successively printed on the equipment.
This week the company announced a new version of Flow, version 3.0, and it includes several new features, as you might expect. One, for example, is the ability to handle larger parts that would fit into the company’s latest and much larger device, the Sapphire XC. Velo3D said the parts can be 400X larger.
In addition the Sapphire XC contains an amazing eight 1kW lasers, which can now be integrated into Sapphire print jobs with Flow 3.0.
But the most interesting new feature from my standpoint is a kind of automated DfAM process that is now integrated with the software.
DfAM stands for “Design for Additive Manufacturing”, a discipline that has recently arisen to address the peculiarities of AM part production. While traditional parts were typically designed with the constraints of traditional making processes, many of these part designs are now being 3D printed. Unfortunately, the design constraints of traditional making equipment can be quite different from today’s additive systems.
The solution is to apply a DfAM process in which a designer reviews the 3D model and makes changes to accommodate the new AM production constraints. This can be quite expensive to do, as it requires a skilled 3D designer knowledgeable in DfAM techniques, and also familiarity with the target 3D printer’s specifications.
Flow 3.0 seems to get around at least some of this expense by including a way to automatically perform some of these modifications. Apparently designers simply need to upload a CAD file — as opposed to a mesh (STL or 3MF) file — to Flow and the software takes over from there.
How exactly does Flow know what to do? Velo3D explains:
“Flow 3.0 accomplishes this by utilizing a generalized set of recipes to precisely prescribe and simulate the layer-by-layer build for the desired part. The software’s composer detects geometric features and applies the corresponding process to achieve that desired outcome. Unlike other software offerings, Flow 3.0 uses information from previous layers to inform the print strategy for subsequent layers, resulting in better parts and greater design freedom.”
This is quite interesting, as I am unaware of other slicing tools that perform this level of automated design.
The presence of this feature could mean that older part designs that were not immediately printable can suddenly become viable. In many cases it is likely the cost of tweaking the old designs for AM production weren’t worth doing, but now perhaps they can be attempted using Velo3D’s solution.
Another unusual feature of Flow 3.0 is a method to simplify overly complex mesh files. Sometimes the transition from CAD to STL generates massively huge files with hundreds of millions of triangles, as the export attempts to fit the complex design with a mesh skin. This is usually unnecessary as the details often exceed the capabilities of the target 3D printer. These huge files can be difficult to handle, and often choke typical 3D print software tools. Now Flow 3.0 has a way to fix this issue. Velo3D explains:
“With Flow 3.0, the print preparation software can reliably generate and leverage meshes of models containing up to hundreds of millions of triangles. The capability is made possible by offloading the computation of larger files to Amazon Web Services. The customer sends a CAD file and receives back a compacted file that can be used on any printer to build the part.”
These features will surely be welcomed by Velo3D customers, particularly those with the new and large Sapphire XC system.
Meanwhile, the rest of us are seeing some very powerful features that we all would like to see in our own slicing software.
Via Velo3D