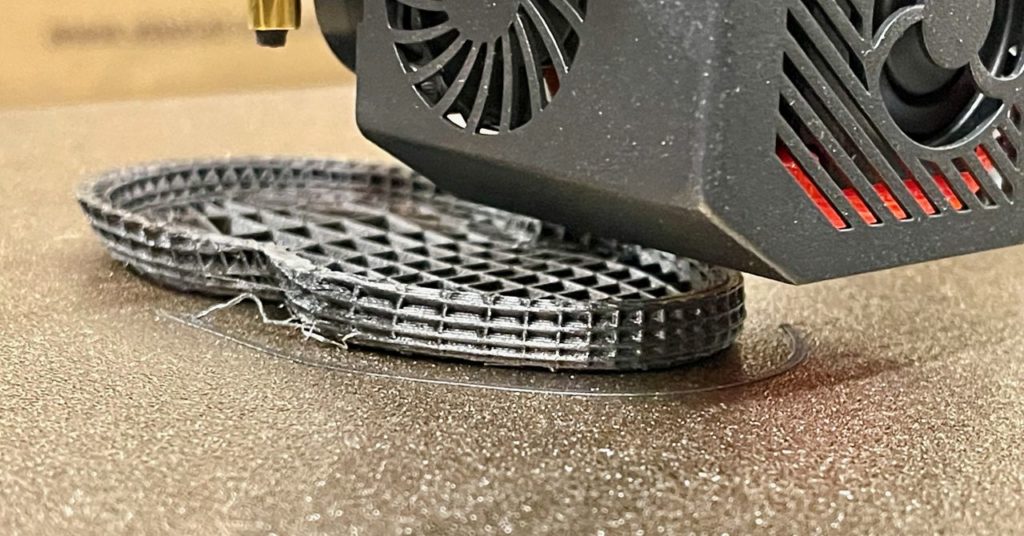
There is an ongoing quest to achieve faster and faster 3D print speeds on FFF equipment. But there are a number of challenges.
Typical desktop FFF 3D printer print at speeds between 40-80mm/second, and while this very often produces excellent quality prints, it is also very slow. A fist-sized object might take 5-7 hours to complete.
That might be sufficient for casual 3D printing, where jobs can run overnight without issue, but it’s definitely a problem for anyone contemplating doing any type of volume production.
Time is money, as they say, and it’s also true with 3D printing. Imagine a 3D printer able to produce three of those fist-sized objects per day, or about 1000 units per year if operated continuously. If a year is the useful lifetime of the machine, and so you’d have to defray the machine cost over its output of 1000 units. For a US$2000 machine, that would be US$2 per part.
But what if your machine could 3D print far faster? What if it could produce ten parts per day instead of three? Over a year, the cost per part on that machine would only be US$0.54. The parts are cheaper to produce, and more could be sold.
So there is a clear financial advantage to faster 3D printing.
But is it as simple as cranking up the print speed in the slicing software? By no means! There are a number of technical issues to overcome first.
Momentum
The first and perhaps biggest challenge is momentum. As the printhead flies around the build chamber at ever-increasing speeds, there is a problem when it needs to change direction. The motion system must be designed to handle such abrupt changes through either more robust components, and / or sneaky firmware that attempts to recognize and adjust for dramatic directional changes.
If this isn’t handled properly, the forces involved might cause the stepper motor to skip a step or two, creating a misaligned print. Some 3D printer manufacturers working on high speed devices avoid stepper motors because of this and instead use servo motors that can accurately keep track of their true position.
Viscosity
All materials have different characteristics, and one of them is the viscosity at different temperatures. It may be that even though a particular material can be successfully extruded at a given and optimal temperature, the viscosity might be too high when attempting to push the soft material through at higher speeds. This could create jam.
This is one factor that has led to some materials providers developing “high speed filament” that might overcome some of this effect.
Temperature
Temperature is another concern, and there’s two problems here.
First, a filament moving more quickly through a hot end has far less time to heat up. This means at the same set temperature it may not sufficiently soften by the time it emerges from the nozzle. Some high-speed 3D printer manufacturers have overcome this barrier by developing wild hot ends that are extremely long. This allows the rapid-moving filament to be exposed to heat for a longer period of time and thus gain sufficient softening.
Another solution might be to raise the hot end temperature. Wouldn’t this make sense? More heat during a shorter time might meet the softening needs? Or does it?
It turns out this is not a good idea. That’s because the machine is not always printing at high speeds. For example, it may be doing some detail movements at a relatively slow speed, and now your filament is over-exposed to the heat. In the worst cases the filament may burn or decompose if exposed to the wrong temperature for too long.
Designers of high-speed 3D printers must be very careful with temperatures.
Composites
Composite materials pose an additional problem. These are polymer filaments that are mixed with another material to create a somewhat stronger composite material. Typical additives include chopped carbon fiber, glass fibers or other strong substances.
At slow speeds these composites flow naturally through the hot end and nozzle. Occasionally you may get a jam when the mixed fibers clump up at the nozzle. I’ve personally had this experience with wood-filled filament a few times, even at slow speeds: the fibers tangle up and plug the nozzle.
At higher speeds this phenomenon is even more likely to occur. Should the fiber content of a segment of filament be wrong, then you might all of a sudden get an instant jam. This suggests that high speed composite filament requires very special quality controls.
Capacity
High speed 3D printers eat filament like salty peanuts. While a normal 3D printer might take a couple of days to run through a 1kg spool, this is far shorter on a high speed machine, perhaps only hours.
To avoid the requirement for constant spool swaps, the high speed 3D printer must be able to accommodate larger-capacity spools. It’s possible today to purchase 2kg, 5kg or even 8kg spools, which would be ideal for high speed operation. However, many of today’s machines would literally tip over if an 8kg spool was mounted on them.
High Speed 3D Printing
The notion of 3D printing at very high speeds is indeed possible, but not so much on machines that are not designed to do so. You can tweak them slightly to gain a bit of a speed advantage, but don’t expect miracles unless you’re prepared to get a true high speed device.