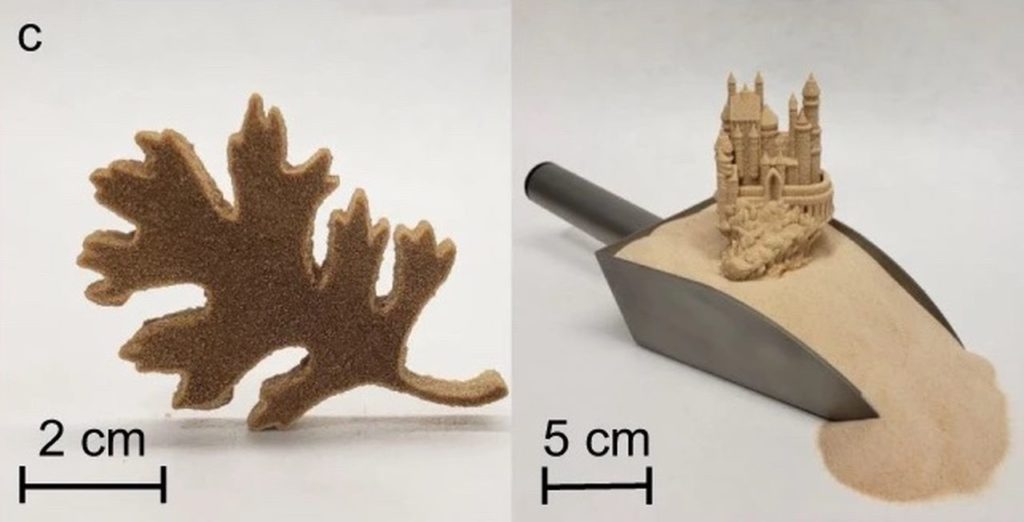
Researchers have identified a technique for 3D printing sand with great strength.
Materials are a key factor in determining the cost of an additive project, particularly if the part being produced is large. Doubling a dimension means the cube of the material is required. This is the game when 3D printing large objects with construction 3D printers.
Currently the de facto standard construction 3D printing process is concrete extrusion. However, there was a time long ago when it was not, and researchers experimented with a variety of techniques.
One in particular I recall was D-Shape. Almost ten years ago this company, founded by Enrico Dini, attempted to build a building-sized sand 3D printer. While the venture never proceeded much further, they did use a binder jet style of solution: a layer of sand would be pushed over an area, and then an arm would pull a toolhead over top to deposit a binder. Repeating this layer-by-layer generated a huge sand object that would have to be dug out of loose sand when complete.
One of the issues with that approach was that the resulting object just wasn’t very strong. Now that problem may have been overcome by researchers at the Oak Ridge National Laboratory. They’ve found ways to dramatically strengthen 3D printed parts made from sand and binder.
This process was developed for use with standard silica sand, found all over the planet.
The process involves using a polyethyleneimine binder. This binder, when used to fuse silica sand, was found to more than double the strength over conventional binders. They explain:
“We report the discovery of a versatile polyethyleneimine (PEI) binder for silica sand that doubled the flexural strength of parts to 6.28 MPa compared with that of the conventional binder, making it stronger than unreinforced concrete (~4.5 MPa) in flexural loading.”
Note this is for unreinforced concrete. Reinforced concrete would obviously be stronger, but so can sand objects made using the new polyethyleneimine binder.
The researchers also found a way to make the sand part even stronger. They explain:
“Furthermore, we demonstrate that PEI in the printed parts can be reacted with ethyl cyanoacrylate through a secondary infiltration, resulting in an increase in flexural strength to 52.7 MPa.”
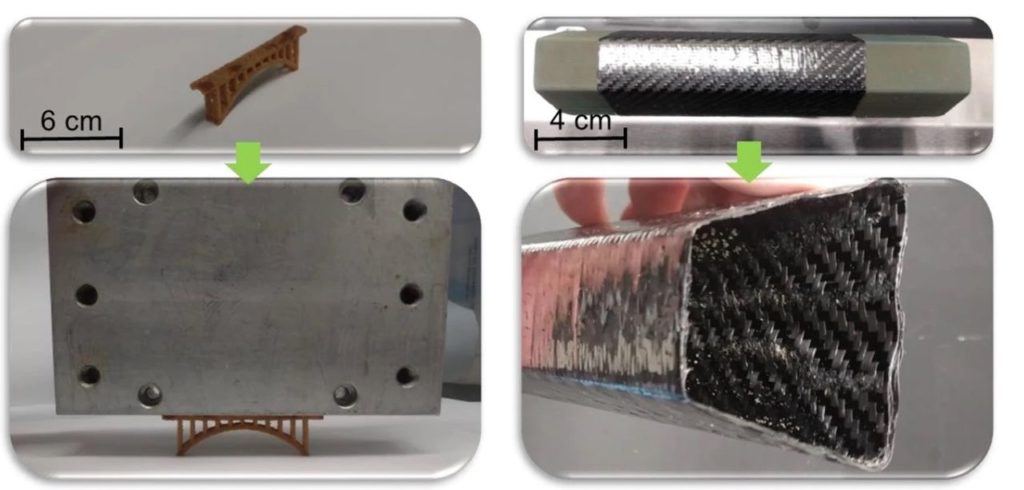
At first glance you might think this development might change the equation for construction 3D printing. That is, if the cost of binder and infiltration agent are sufficiently low to enable competition with the more popular concrete extrusion approach.
However, that’s unlikely to be the case, because the binder actually dissolves in water! An application of water disrupts the hydrogen bonding on the binder, causing it to degenerate.
So what use is this material, then? Plenty, it seems.
While this new binder shouldn’t be used for construction 3D printing due to the danger of water infiltration and catastrophic collapse, it could instead be used for molding.
Imagine 3D printing a large sand mold with a very complex design. The design is sure to be maintained through the molding process due to the strength of this sand part. Strong materials could be cast in such a mold, and then easily removed through a water wash.
If commercialized, this binder could open up more possibilities for larger-scale sand 3D prints for casting applications.
Via Nature