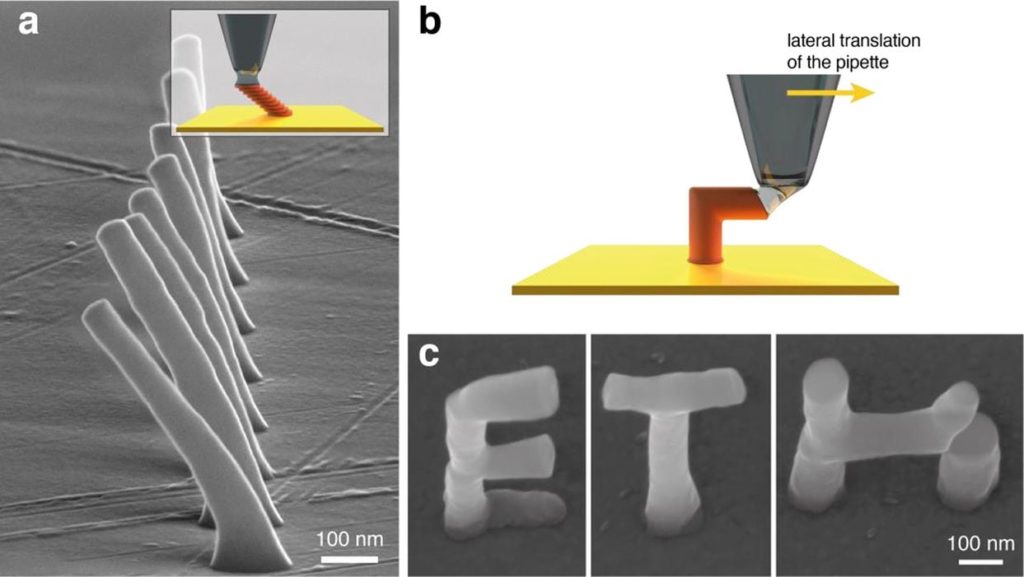
Researchers have devised a system using a 1.6nm nozzle to 3D print incredibly tiny objects.
Nanoscale 3D printing is of increasing interest to industry, where multiple new applications can be enabled. While there is interest in optical, electric and antenna applications, perhaps one of the most important could be battery printing.
The smaller the resolution possible, the more applications can be achieved. The ability to miniaturize a component has increased in importance for mobile applications where weight is critical.
The ETH Zurich researchers examined a number of existing nanoscale 3D printing processes and found the highest resolution practically achieved so far was with two-photon stereolithography systems, where voxels can be made as small as 65nm (note: this is equal to 0.000065mm — very, very small.)
They explain:
“We demonstrated an approach to achieve nanoscale resolution in electrochemical 3D printing, that allows manufacturing of metal structures with dimensions <100 nm, unattainable by other electrochemical methods.”
However, the issue with that process is that it has a rather limited set of materials to work with: the photons must travel through a resin transparent to their wavelength. Instead, the researchers hoped to expand the material possibilities of nanoscale 3D printing by using an electrochemical approach similar to electroplating.
Their approach was to use a “meniscus-confined electrochemical AM” process. The idea here is that an electrolyte solution will form a curved geometry as it emerges from a tiny nozzle due to surface tension.
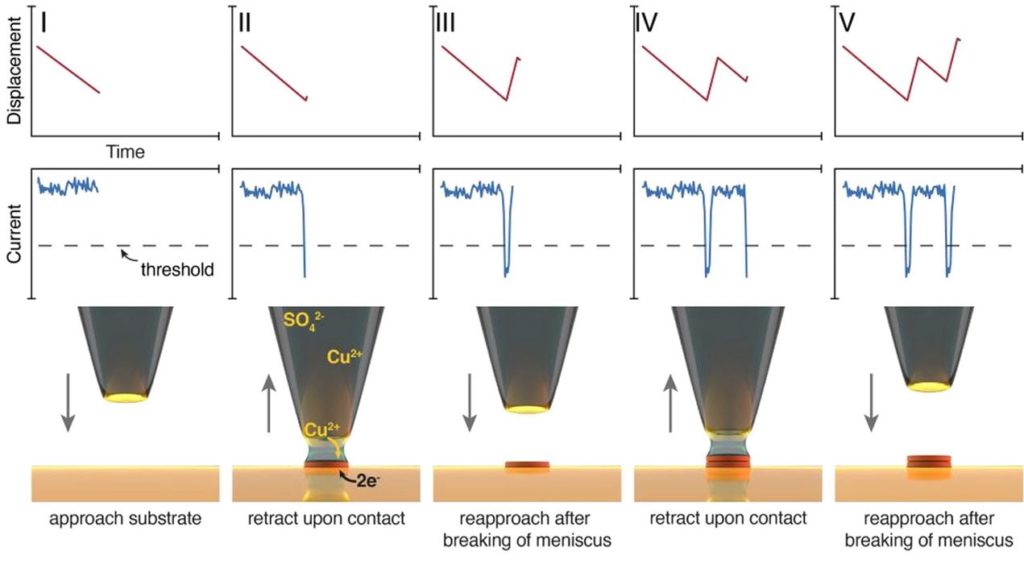
This bubble, if precisely controlled, can touch a conductive surface and achieve a deposition. This chart illustrates how the process works:
Incredibly, the nozzle for this system is only 1.6nm wide (0.0000016mm), allowing the creation of extremely tiny depositions.
The major challenge for the researchers, however, was not the deposition, but instead the ability to precisely move the nozzle. Without precise movement, control of the meniscus deposition could not happen properly.
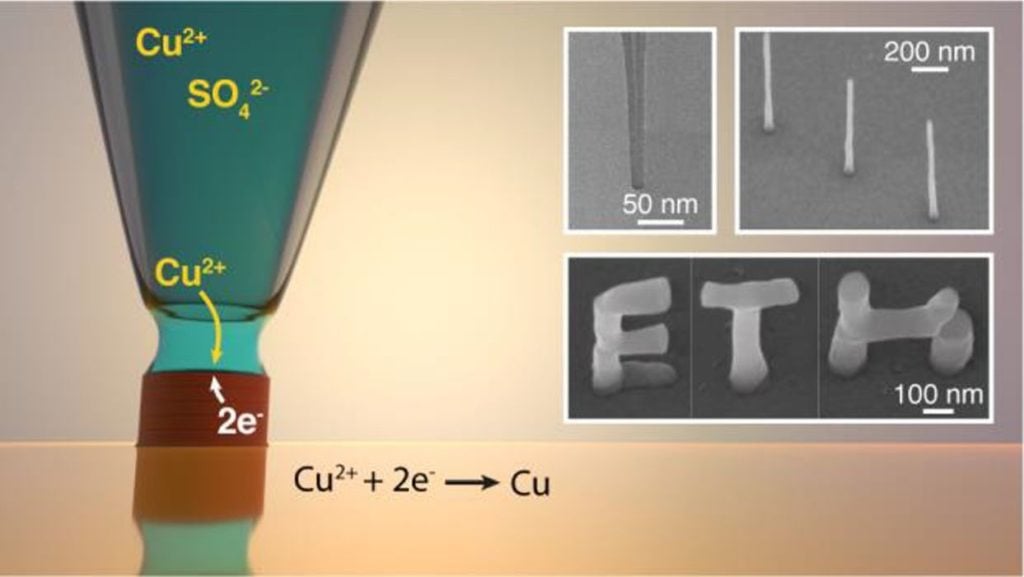
Their motion system was designed using piezo-electric positioners, which provided the necessary accuracy at this incredibly small scale.
They explain the deposition control:
“Interestingly, the feature size strongly depends on the electrodeposition parameters, namely, the printing voltage and the faradaic current (feedback threshold). These determine the quantity of metal deposited at each cycle of the process.”
This effect meant they were able to control the voxel size dynamically during the print process, something larger 3D printers normally cannot do.
A very interesting development is that they were able to 3D print overhangs, up to 89 degrees. This could be due to the limited effect of gravity on the extremely tiny material amounts and the strong bonding between layers.
While most of their experiments used a 45nm nozzle, the research team decided to push the envelope and tested the process using 2nm and 1.6nm nozzles.
They were able to print columns with a diameter of 25nm, perhaps the smallest objects 3D printed. However, they found that at this scale the prints were highly affected by even slight vibrations, resulting in geometric faults in the print.
Their smallest print had features of only 14nm, but their paper said this was “irreproducible”, suggesting it was a fluke. However, 25nm structures appear quite possible and repeatable.
Could even smaller features be achieved? They believe so, but with a different approach:
“In principle, this could be achieved by reducing the quantity of metal electrodeposited in a single printing cycle by about 3 orders of magnitude. This small amount of charge would approach the level of several attocoulombs (10–18 C), which is equivalent to only a few electrons transferred onto metal ions during a printing cycle. This miniscule amount of charge that should be equivalent to almost atom-by-atom fabrication, which is difficult to control at high acquisition rates (∼kHz) required for reliable printing. Thus, electrochemical AM at this scale would require a drastically different approach, where the printing feedback will operate at fundamentally different (not based on faradaic current measurement) physical principles.”
This is an incredible achievement that will no doubt be commercialized and enable future product designers to achieve possibilities previously impossible.
Via ACS