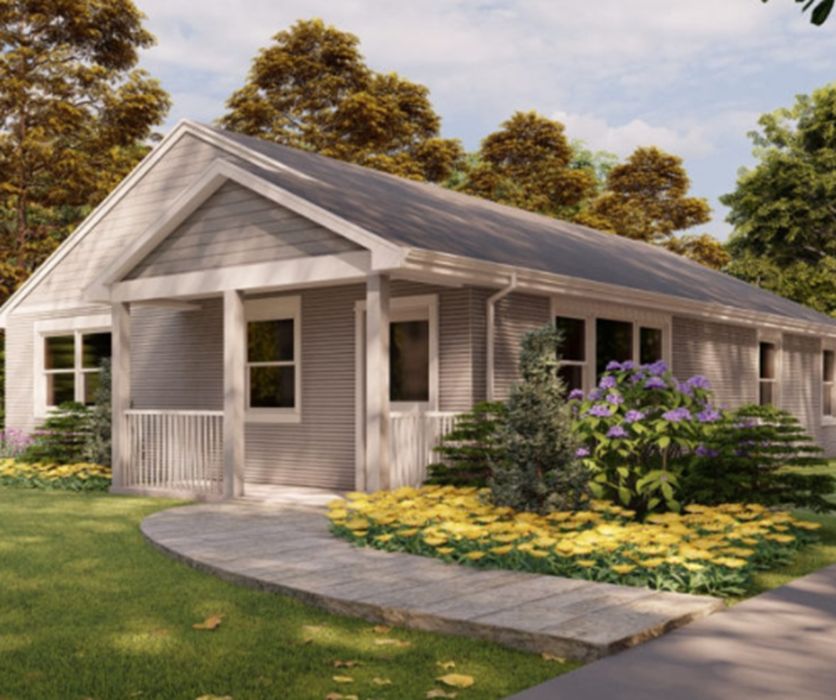
Charles R. Goulding and Joseph Castine interview Kirk Anderson, COO of SQ4D, a construction 3D printer company.
Since the dawn of time, one of the basic three necessities in life is shelter. As a result of the pandemic, the United States finds itself in one of the largest housing bubbles since the recession of 2007. The Case-Shiller U.S. National Home Price Index has risen by 18.6% in the twelve months preceding September 2021. In addition, the rental pricing has continued to increase over this period making it harder for people to seek alternate forms of housing.
With these shelter prices at highs, many people are having difficulty finding places to live at an affordable price. That’s where SQ4D plans to meet the need in the market, by 3D printing concrete houses at more reasonable prices, so that the everyday person can afford to have a place to live.
Kirk Andersen, Chief Operating Officer of SQ4D has previously tried his hat in several disciplines including graphic design and engineering. Having always been good with his hands accompanied by his interest in the architecture and design industry, Kirk found himself in the construction industry. During his time in the construction industry, Kirk began to branch out due to his interests in additive and subtractive manufacturing by purchasing an entry-level 3D printer.
With this 3D printer, Kirk mainly tinkered around printing shapes and building out small model 3D printed homes. After seeing an article on a group of guys who had built and put concrete through a 3D printer Kirk was able to link up with his business partner Enzo Pagani, and he now finds himself as part owner of SQ4D.
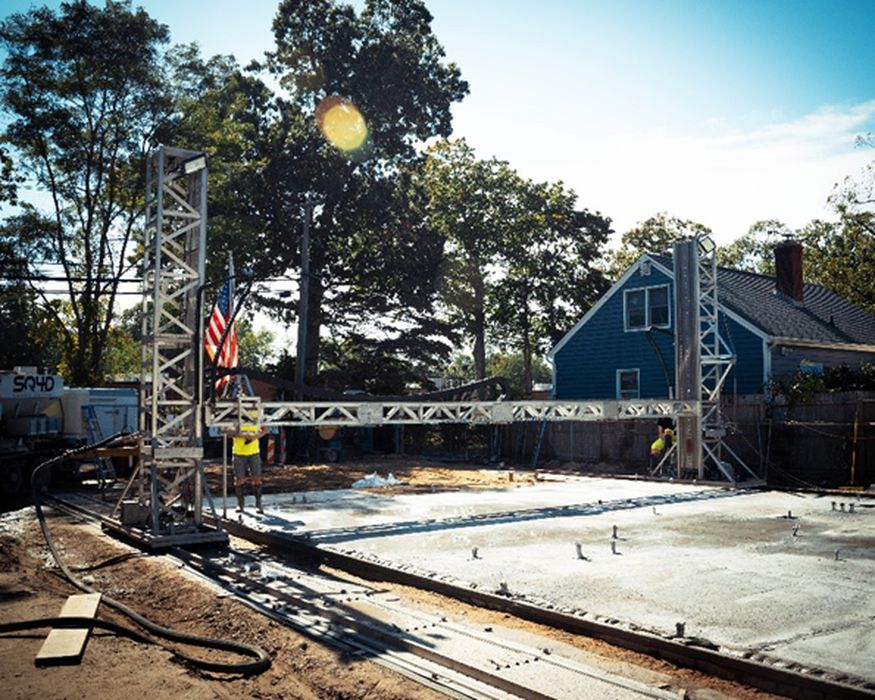
SQ4D aims to leverage its additive manufacturing system to develop and build affordable homes at a lightning-fast pace compared to conventional construction means. One of the main goals of the minds behind SQ4D was to originally eliminate the need to confer with building departments which are often very bureaucratic. Especially in the Long Island, NY metropolitan area, municipalities are very particular about building code and energy code standards.
Using his construction background Kirk and his team were able to design and construct the concrete system 3D printer which SQ4D currently utilizes. In developing this gantry system Kirk, and the team at SQ4D aim to eliminate the need to speak with people, and rather replace those communications with a robot that is programmed based on design specifications, which can reduce miscommunication that leads to the halting of projects.
The first proof of concept structure that was constructed was a 500 ft2 non-permitted structure in front of their office building in Patchogue, NY. After this proof-of-concept, SQ4D was able to speak with some municipal officials in Riverhead, NY who understood the 3D printing technology and ultimately gave them a permit to build a 1900 ft2 concrete house in a cement yard, which at the time in 2019, was one of the largest 3D printed structures in the world.
This was able to further illustrate SQ4D’s concepts and proved important in educating real estate agents, bankers, insurance companies, and other vested parties in home purchasing. Throughout the pandemic, SQ4D put in the groundwork to get permitting and paperwork done for a residence in Riverhead, which sold for US$299,000 that recently completed printing and is undergoing utilities and roof installation.
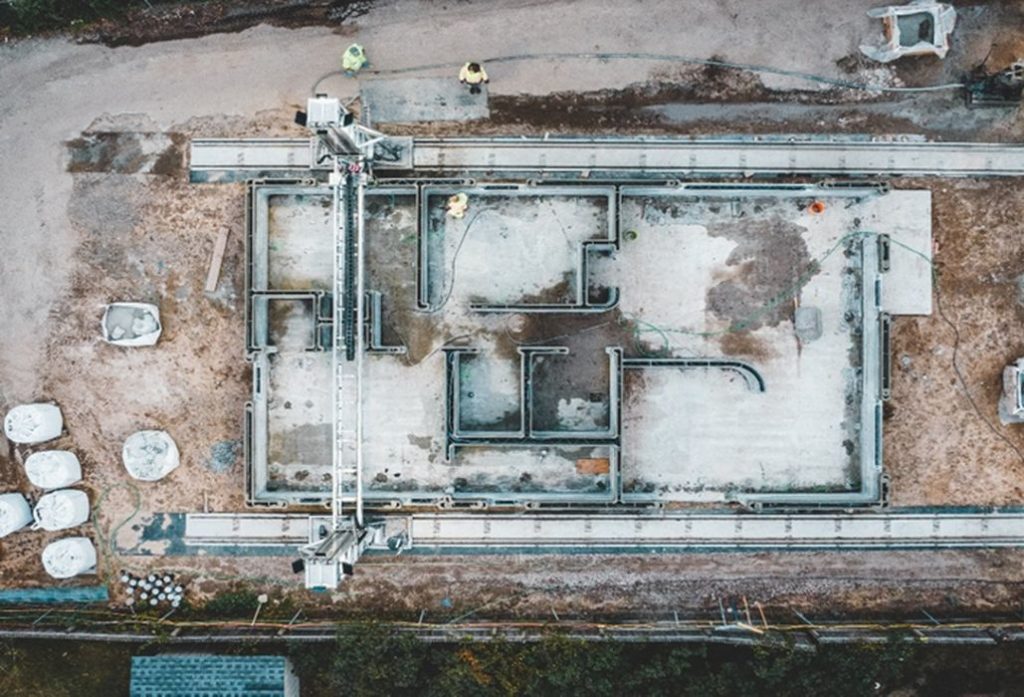
One of the largest challenges that SQ4D faces, and will continue to face, is people who question the integrity of these 3D printed homes. To this Kirk Andersen said, “We are layering it (concrete) just like (concrete) blocks would be, but we are actually intertwining the entire floor plan into a more structure, which is stronger and more efficient to build.” In the construction business, the costs are largely dictated by who is doing the building and how much the land costs. With this technology, rather than for example paying for 2×6’s vs 2×4’s for stick frame houses the G-Code program can be adjusted to make the walls wider, longer, or rounded without much-added cost.
Currently, the company is focusing its energy on building single-story homes to give people homes at a more affordable price. As they are still proving out these concepts the costs are not where they will be in, say, ten years.
But SQ4D does plan to expand their current operation and are currently designing and planning out the development of a second printer with more modularity. With their current machine, the Riverhead home was printed in 100 hours, which in “40 hours work week time” is only 2.5 weeks. This is approximately 2-3 times faster than the normal 5-8 week framing period of stick frame homes.
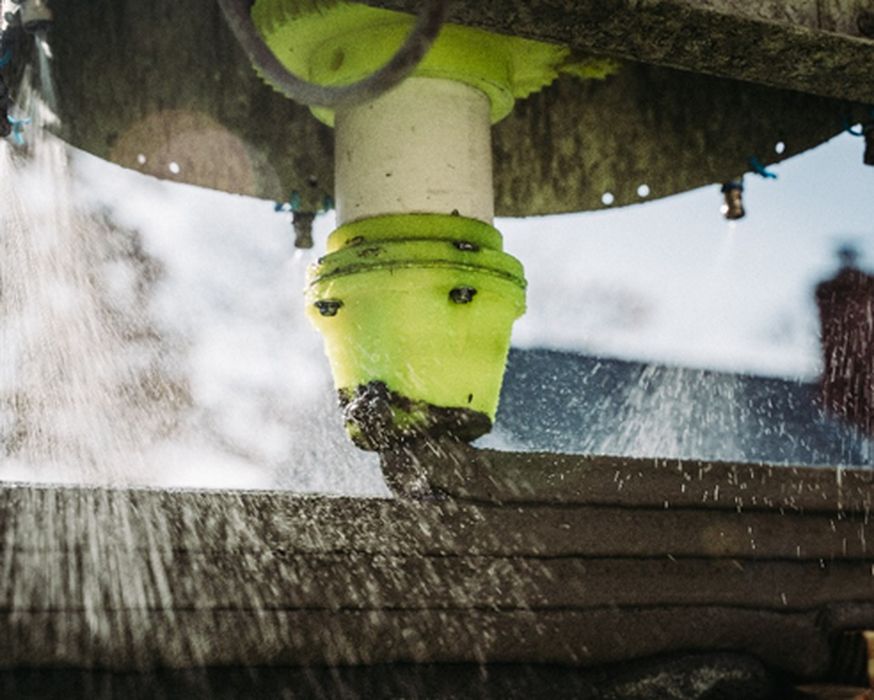
In addition to the speed of these printers, SQ4D will soon have the capability to make several aesthetic alterations to the concrete including smoothing via smoothing arms. This is possible due to the use of Type III concrete (Portland Cement), which offers high strength at early stages of setting due to the baking and fine grain of the material, allowing them to stack layers while not losing the geometric shapes and sizes. This is due to the low slump rating (~2) of their concrete which is very viscous to allow for manipulation and extrusion of the concrete through the extruder nozzle. This type III concrete will also provide SQ4D the opportunity for growth as they can utilize the cement, sand, and water from anywhere in the country. The concrete structure of these homes allows for hanging of items such as cabinets, and the exterior façade can be left as layered concrete which is sealed by elastomeric paint, or if desired, siding can be hung.
This technology currently has massive potential, much like the plastic and metal 3D printing industry showed decades ago. Kirk himself believes that because this technology is disrupting one of the largest industries, the housing industry this technology may have an even larger future than that of 3D printing with metals, or even plastic resins. The pure volume that their gantry system extrudes is what leads Kirk to believe that his technology is here to stay, and in 20-30 years he said you will likely drive down a block and there will be a robot out their 3D printing some portion of a home. Automating these processes makes sense as it makes construction safer and more practical in the long term.