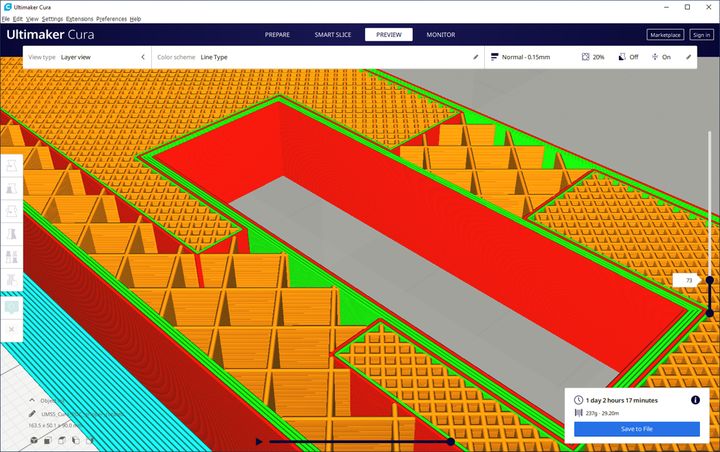
BigRep announced an important collaboration with Teton Simulation.
Teton Simulation builds an incredibly powerful 3D print slicing system that’s far, far beyond anything you could expect to use in “normal” 3D print slicers.
The problem is that the strength of 3D printed parts is directly affected by the slicing parameters and method of making each layer. For example, if the density of infill is lowered, the part loses strength. Typically, slicers are a kind of “blunt instrument” when preparing 3D print jobs: the infill for the entire part is set in one parameter.
Meanwhile, it is clear that one should really vary the amount of infill to make some regions stronger, while other regions don’t require extra material for strength.
Usually regions requiring additional strength are identified through the use of sophisticated, but separate, FEA tools. A designer can look at the FEA output and visually identify regions requiring strength, and then make some adjustments to the slicing system, as are possible. Typically this is an iterative process, where tweaks are repeatedly applied until a maximum strength is achieved — or until the designer gives up or runs out of time.
Typical slicers just don’t have the smarts to do this, and that’s why separate FEA tools are used.
But this is where Teton Simulation comes in.
They produce “SmartSlice”, an advanced slicing system that incorporates FEA methods. In other words, the operator inputs forces into SmartSlice and it calculates the FEA — within the slicer!
It then organizes a more sophisticated slicing pattern for each layer that optimizes for the required strengths. SmartSlice typically produces highly unusual layers where the infill density and directions vary.
This approach cuts out a significant amount of steps involved in obtaining a proper part: SmartSlice performs the analysis and uses that result to direct the slicing, all within one tool.
Teton Simulation has previously made arrangements to integrate SmartSlice into Ultimaker Cura, and more recently with GrabCAD. Now, they are apparently integrating it into BigRep’s slicing software.
Managing Director of BigRep Dr. Sven Thate said:
“We are excited to work with Teton Simulation and explore the possibilities of their advanced FEM technology. We are convinced their industry-standard design verification will boost large-format FDM usage even in the most load-critical applications. We also see the possibilities of their load based design optimization to deliver significant time and materials savings and make FDM usage on industrial level easier than ever.”
BigRep added:
“The output of this partnership is expected to bring confidence that parts meet functional and performance requirements as well as time, money and material saving possibilities with automated part analysis and optimization from small- to large-format 3D printing.”
This is very likely to occur once they launch the integrated product.
SmartSlice solves a persistent but often ignored issue in 3D printing: how to actually get the best possible part. It seems that multiple 3D printer manufacturers (Ultimaker, Stratasys and now BigRep) have caught onto this idea and have partnered with Teton Simulation.
It’s very likely there will be additional industry partners in the future, and at some point we may see SmartSlice as a default feature in slicers, at least for industry use.
Via BigRep and Teton Simulation