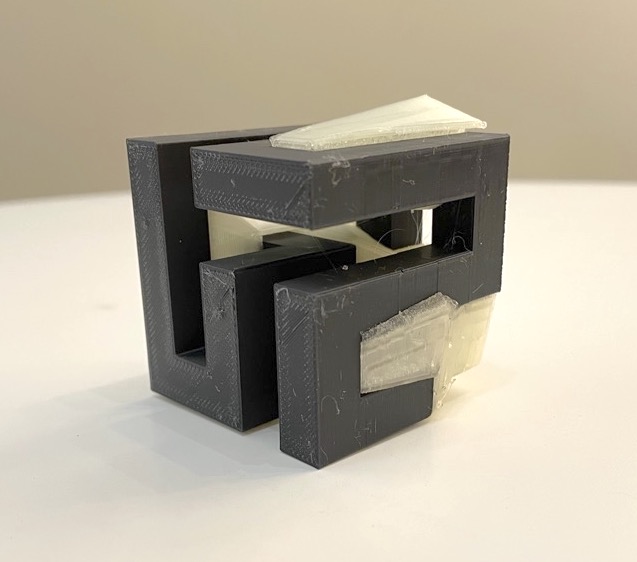
MakerBot announced two interesting and complementary materials today that could make 3D printing ABS objects far easier.
The company has already been quite invested in ABS printing, as their METHOD X platform is one of the best I’ve seen for that often misbehaving material.
ABS is tremendously difficult to 3D print due to its propensity to warp. That’s because there’s usually a very high thermal gradient between the extrusion temperature and the ambient air temperature. As the center of the print cools, it tends to pull up the extremities of the geometry and the print fails. This means that it is extraordinarily challenging to 3D print any ABS object having complex geometry.
But that’s the prime advantage of 3D printing technology, so how can you make it work?
MakerBot’s METHOD X attempts to overcome the problem by providing a fully heated and controlled build chamber. This results in a huge drop in the thermal gradient, as the print stays at a very hot temperature until the print completes. Then when removed it shrinks in all axes uniformly to arrive at the correct dimensions.
That approach does work, and I’ve personally inspected ABS parts from this machine and found them to be of exceptional quality.
However, while the prints I saw were quite good, they were not particularly challenging geometry-wise. The real value of 3D printing ABS comes when you can print arbitrarily complex parts without fail.
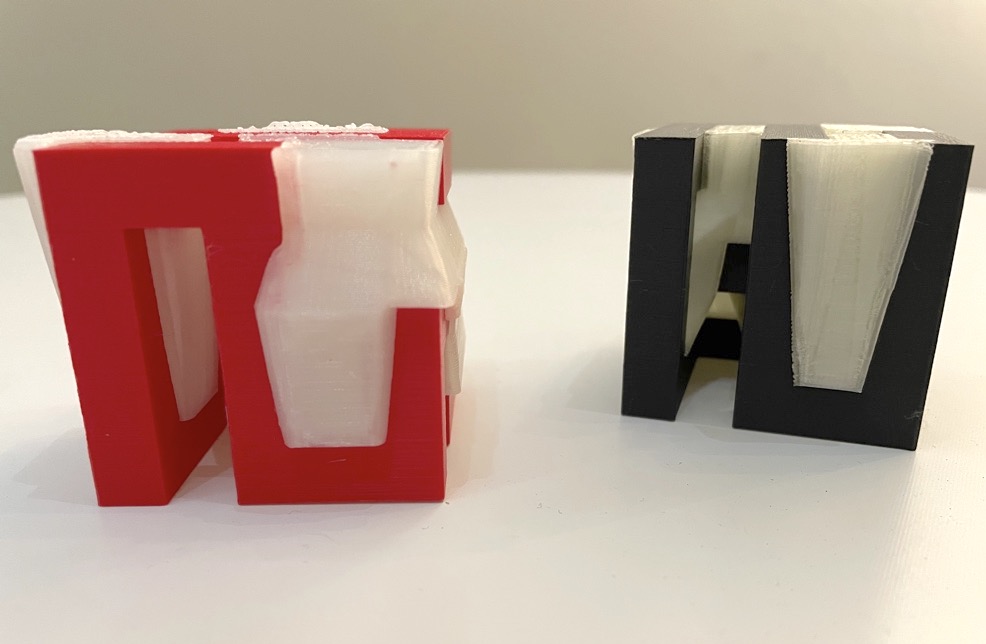
That seems to be the goal of two new materials introduced by MakerBot today: ABS-R and RapidRinse.
ABS-R is an ABS material, as you’d suspect, but it’s slightly different chemically. MakerBot explains:
“ABS-R is a new ABS formulation that provides superior printing reliability and performance for consistent, repeatable ABS prototypes, tools, and parts. ABS-R is optimized to work with the new RapidRinse fast-dissolving support material to deliver the best print quality and user experience.”
RapidRinse is the complementary soluble support material. It’s easily dissolvable in water, meaning it can be quickly removed, even from highly complex 3D prints where non-soluble supports might be trapped inside the geometry. MakerBot said the material can “dissolve significantly quicker than other high-temperature soluble support materials under the same conditions.”
Why not just use a commonly available soluble support material like, say, PVA? I suspect it’s because of the heated chamber on the METHOD X, which might soften the relatively low-temperature PVA material, making it less suitable for support structures.
Meanwhile, the new RapidRinse is clearly designed to work perfectly within the METHOD X’s heated chamber. This technology is now branded “VECT 110”, which suggests the build chamber might actually reach 110C, far above the typical 70-80C seen on other equipment.
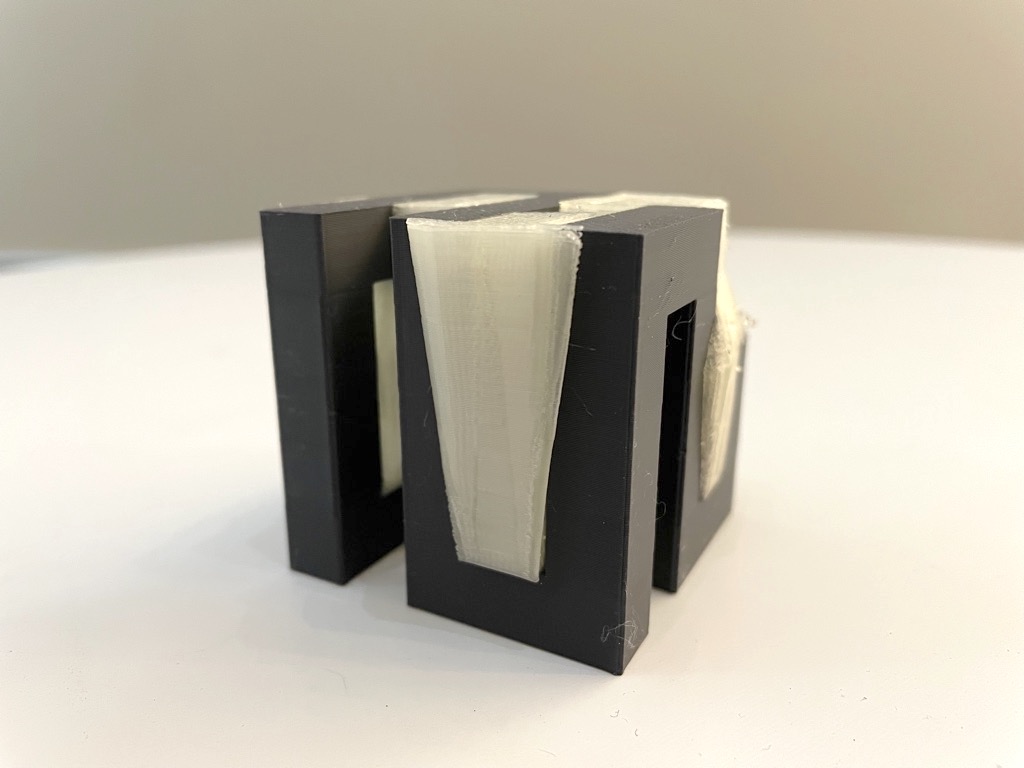
The combination of hardware, software and materials on the METHOD X now allows reliable production of high quality — and complex — ABS parts with a dimensional accuracy of 0.2mm. That’s certainly a capability that few other professional 3D printer can achieve.
MakerBot intends on shipping the new materials this December.
Via MakerBot