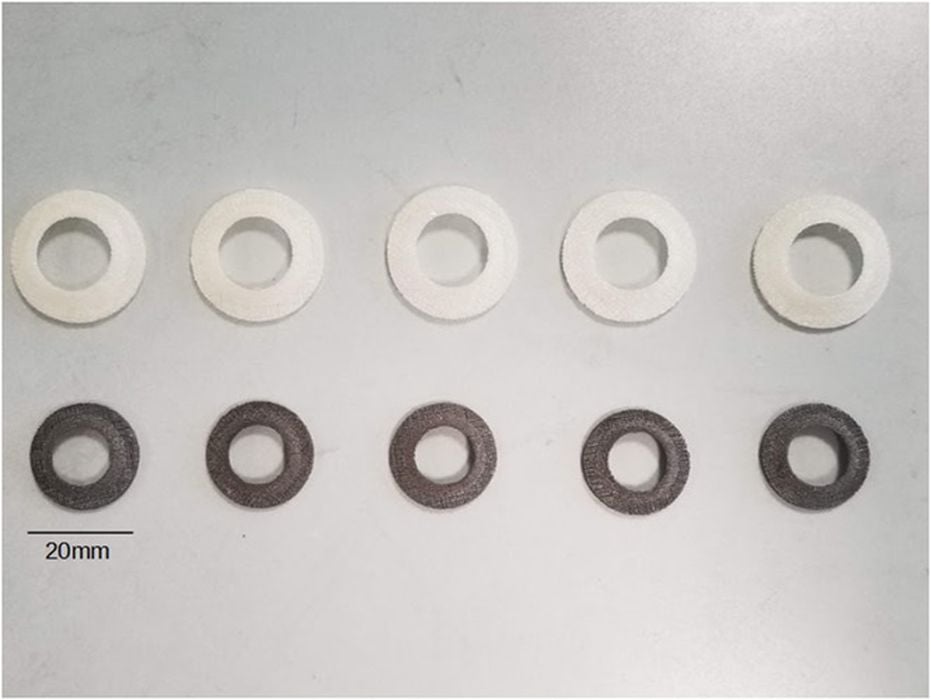
Researchers have developed a method of inexpensively 3D printing fully solid ceramic structures with complex geometries using FFF technology.
Ceramics are one of the materials I expect to be used widely in the future of 3D printing. Ceramics offer high rigidity, chemical resistance, electrical resistance, and most importantly, extremely high temperature resistance.
Those are properties that surely are required by many applications. Yet today we see relatively few ceramic 3D printing applications taking place.
One reason is that the cost of producing quality complex ceramic 3D printed parts is high. This is because the processes used to 3D print the ceramics are themselves expensive.
This is not news; there are many industries that are effectively “locked out” of 3D printing because their industry just happens to have lower costs for parts than others. Aerospace, for example, quickly adopted 3D printing because aerospace parts have always been expensive. Meanwhile, the local metal workshop hasn’t because the parts they produce don’t justify the high cost of acquiring metal 3D printing equipment.
The same has happened in ceramic 3D printing, which is offered by only a few vendors. These tend to be relatively pricey, again locking out many applications.
Could ceramics be 3D printing used more inexpensive processes? The answer is yes and no.
Yes, because there are ceramic 3D printing methods that use syringes to push ceramic material that can be fired post-printing. However, the resolution is extremely coarse and thus those approaches are useful only for producing larger items like vases or bulk electrical insulators.
Now there seems to be a way to 3D print ceramics in an extremely cost effective manner, according to researchers in Canada and Italy.
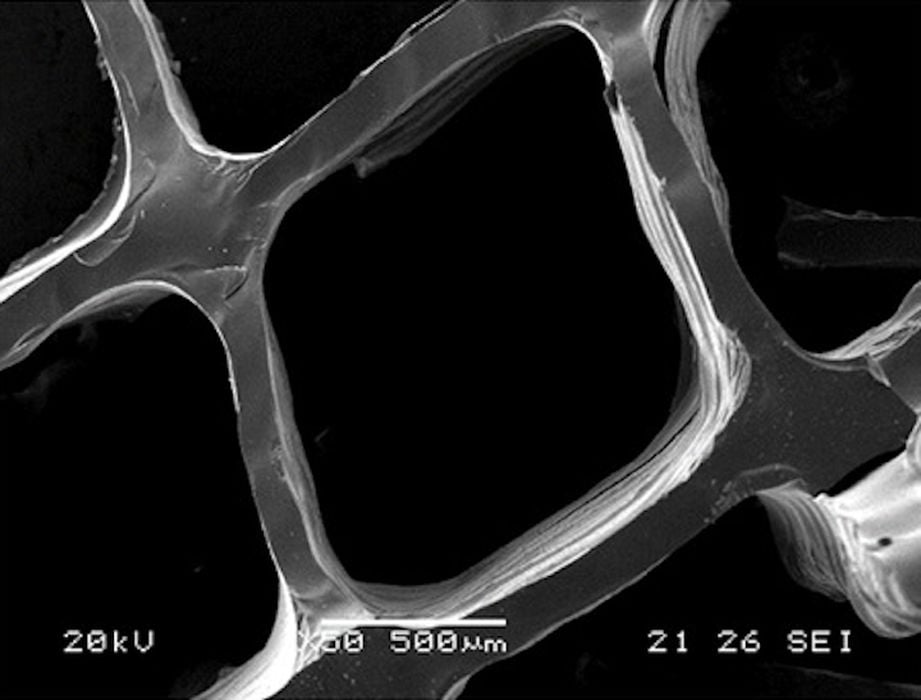
In a paper entitled, “SiOC(N) Cellular Structures with Dense Struts by Integrating Fused Filament Fabrication 3D Printing with Polymer-Derived Ceramics”, the researchers propose using standard FFF 3D printers and filament for a new method of ceramic printing.
Their process is indeed inexpensive: they were able to produce solid ceramic objects using a standard LulzBot TAZ 6 desktop 3D printer, and some TPU filament.
There are some other details that require explanation, however.
The TPU filament was impregnated with a precursor material for SiCN ceramic, polysilazane. This was done by soaking the TPU in a solution of acetone and a catalyst prior to impregnation on a timed schedule. After impregnation, the TPU filament was dried at room temperature for one day.
The next step was to 3D print the desired structure on the TAZ 6 using the impregnated TPU filament. This results in an object made from TPU and the ceramic precursor.
Prints were then heat treated in a furnace at 160C for three hours, cooled, and then fired at 1200C to pyrolyze the print. This process created the ceramic prints.
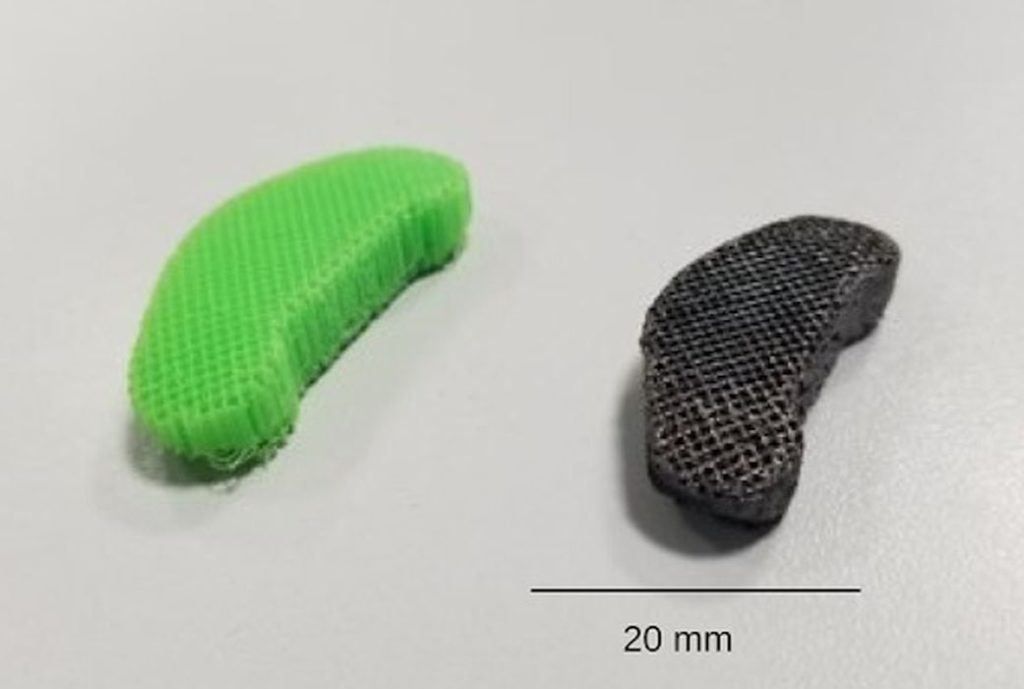
The researchers found the ceramic material to be not only biocompatible, but also quite suitable to be used as a scaffold for bioprinting. The idea here is to 3D print a ceramic scaffold for cells to grow bone to a desired geometry.
That could certainly be one of the commercial applications for this new ceramic technology, as the cost of this process is likely very significantly lower than options on the market today.
Consider what was done here:
- A standard, inexpensive 3D printer was used
- Standard TPU filament was used
- A chemical bath prepared the filament
- A furnace was used to finish the part
That’s about it. I imagine it would be possible for a filament manufacturer to perform the ceramic precursor impregnation at scale, making it feasible to market directly-usable ceramic filament. All you would require at that point would be the furnace and a procedure.
This research has not been commercialized, but it is sufficiently important that someone certainly will in the near future.
Via Wiley