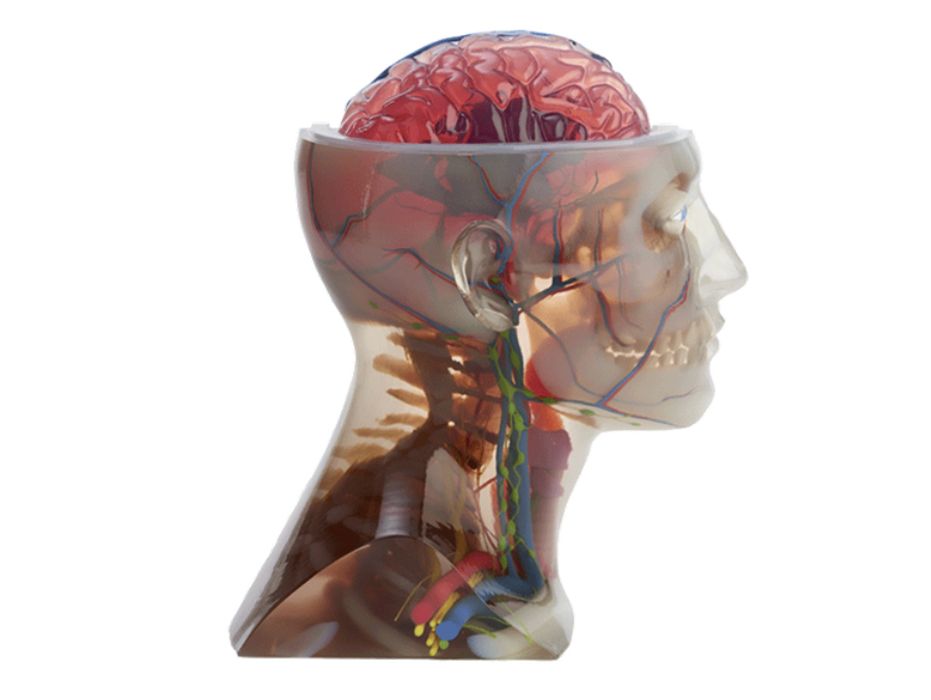
Stratasys announced a consolidation of their PolyJet services.
The company is most well-known for their equipment and materials, but did you know they also operate one of the largest 3D print services on the planet? Stratasys Direct is just down the street from Stratasys HQ, offering making services to industry.
You might suspect that Stratasys Direct is filled with a variety of Stratasys equipment. That might have been true years ago — and it was when I visited a long time ago — but it’s not true today.
Stratasys Direct found that clients really don’t care much for 3D printer brands, but really just want to get their parts made using the most appropriate tools.
Sometimes that means using “someone else’s” equipment.
To that end, Stratasys Direct now offers 3D printing services in a wide selection of 3D printing processes, including:
- FDM (Stratasys)
- SLS
- SLA (3D Systems)
- MJF (HP)
- DMLS
- PolyJet (Stratasys)
The last process, PolyJet, is the subject of this story. It seems that Stratasys Direct is consolidating their PolyJet production. They explain:
“Stratasys Direct Manufacturing, a subsidiary of Stratasys Ltd., today announced the opening of the PolyJet Design and Print Center at their location in Eden Prairie, Minn. The expanded facility is the largest on-demand PolyJet print bureau in North America and centralizes Stratasys Direct’s PolyJet capacity and expertise into one location. The PolyJet Design Center features more than 16 state-of-the-art PolyJet 3D printers, including two J55 Prime printers.”
This move makes sense in several ways.
First, it’s usually more productive to centralize an operation, because knowledge, spare parts, tools, and more can be shared among a larger base of equipment and staff. That should make activities at the new Design and Print Center more efficient than operating a series of separate operations.
Secondly it will focus the stream of print jobs, and let me explain why I believe that is important.
PolyJet is one of the very few 3D printing processes that can produce full color texture objects. I’ve seen many prints of this type from Stratasys, and some of them are so realistic you wouldn’t know they were a 3D print until you picked them up and examined them in detail.
That said, the amount of full color 3D printing is quite limited as compared to “normal” 3D printing of mechanical parts. This is because there are fewer use cases.
Typically full color 3D printing is used for visual prototyping — which is quite different from mechanical prototyping. Mechanical prototypes would test “fit” and “strength”, while visual prototypes would test “look” and “feel”.
Both are valid forms of testing; it’s just that there is a lot less need for visual prototyping.
Now let’s combine that with the PolyJet process. This process involves an ink-jet head selectively dropping liquid resin on a platform, with each layer being individually cured by a UV light source. Layer after layer, the full color object builds up.
To produce the colors, the Stratasys PolyJet equipment uses a spread of resins, each with a base color. By combining droplets they are able to create all possible colors, even able to reproduce Pantone standards.
But to operate these machines efficiently, they need to be used. They should not sit idle for lengths of time. In addition, the individual resin cartridges are relatively expensive, so you don’t want to have too many cartridges lying around waiting to be used.
By centralizing the PolyJet operations, Stratasys Direct solves these issues. First, the machine fleet is very likely scaled to the expected amount of service requests in a consolidated environment. Secondly, smaller quantities of resin cartridges are required because the resin inventory is shared among a larger set of equipment.
This is a good move by Stratays Direct to create a more efficient and effective PolyJet service.
Via Stratasys Direct