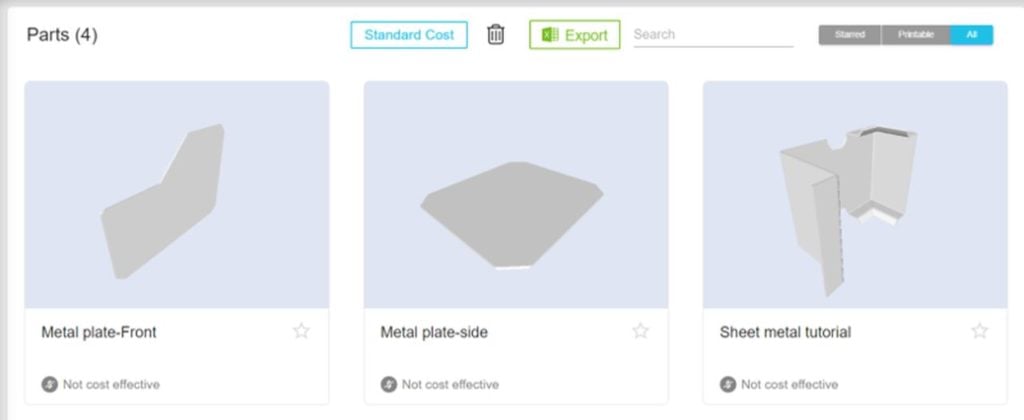
California-based CASTOR announced a new version of their additive inventory software that includes several notable features.
CASTOR doesn’t make a 3D printer, slicing software or materials, but instead addresses a major issues facing many manufacturers: what can be 3D printed?
What Can Be 3D Printed?
Every 3D printer operator knows there are constraints to each 3D printing process. Sometimes these constraints disqualify a given 3D model from consideration for 3D printing.
This is a matter of growing importance, because the future is “digital inventory”. In this approach a manufacturer does not make spare parts in advance. Instead the “inventory” remains a digital model and the parts are simply 3D printed when they are required, any time in the future. This is vastly less expensive than the traditional approach of making thousands of spares and storing them for years — and sometimes never using many of them.
But before you can consider a move to digital inventory, you have to know which parts are applicable.
On a one-by-one basis, this is a relatively straightforward process. The 3D printer operator eyeballs a 3D model and makes a decision about how to print it. Or not. Perhaps the geometry of the part is such that another method, such as injection molding, CNC machining or something else is the best approach.
That may sound like an easy decision, but it’s not for two reasons.
First, many manufacturers simply don’t have anyone on board that is capable of making such decisions. That expertise is still relatively rare and those with the skills are in high demand. There’s no one to make the decisions.
The second problem is scale. Some manufacturers might have hundreds, thousands or even tens of thousands of 3D models in their portfolio, all of which should be examined to determine how to deal with them in the coming digital inventory universe. Even if staff expertise were on hand, it could not complete the job.
Identifying 3D Printable Designs
That’s where companies like CASTOR come in. They produce sophisticated software that can automatically examine 3D models and make determinations not only on whether the models could be 3D printed, but also their predicted cost using appropriate materials.
CASTOR’s latest software release has some very interesting features.
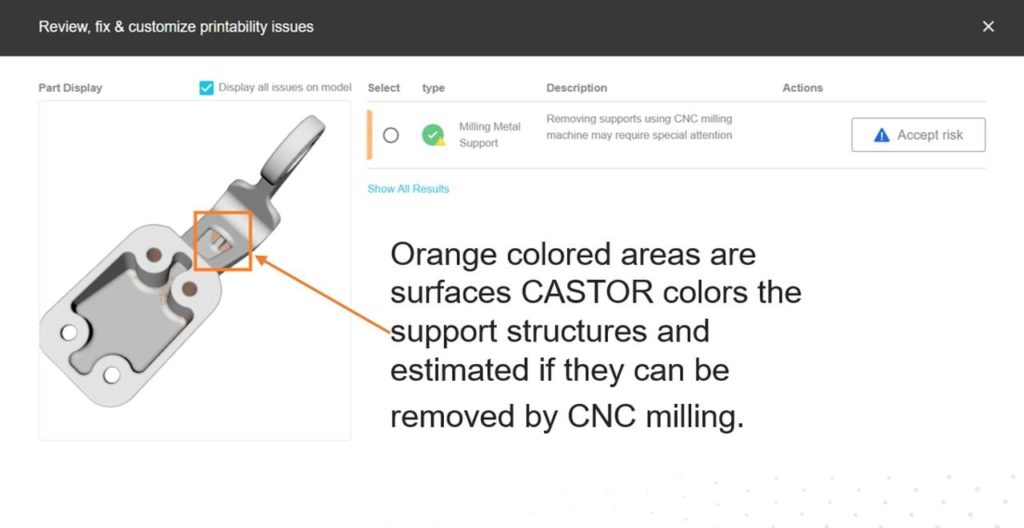
The most interesting one, in my opinion, is their support structure removal feature.
The idea here is that if a 3D model is indeed printable, how practical is it to do so? Virtually all metal parts must be 3D printed with significant amounts of support material, which must be removed after printing. Sometimes this is done manually, but for consistency and scale it’s also performed by 5-axis CNC mills, which shave off the supports to leave the completed part.
CASTOR’s new software release generates a likely configuration for metal support material, and then simulates the removal of it by a CNC mill. The simulation can then determine if it is even geometrically possible to do so. In other words, even if the part might be 3D printable, you can’t remove the supports. That would likely disqualify the part from digital inventory, and certainly is something a manufacturer would want to know before proceeding.
The software will also grade the difficulty of support removal, and that allows a manufacturer to make an informed decision on each part.
The latest CASTOR software include a couple of other interesting features. One detects the presence of sheet metal structures in a part, which are typically not 3D printable due to the thin walls.

Finally, a third feature analyzes the 3D models not just for 3D print production, but also for CNC milling and die-cast production. By estimating the costs for each, CASTOR can now provide a “break even point” for a given part to be produced using 3D printing.
This information is gold for manufacturers who need to decide how to digitally produce parts.
Via CASTOR