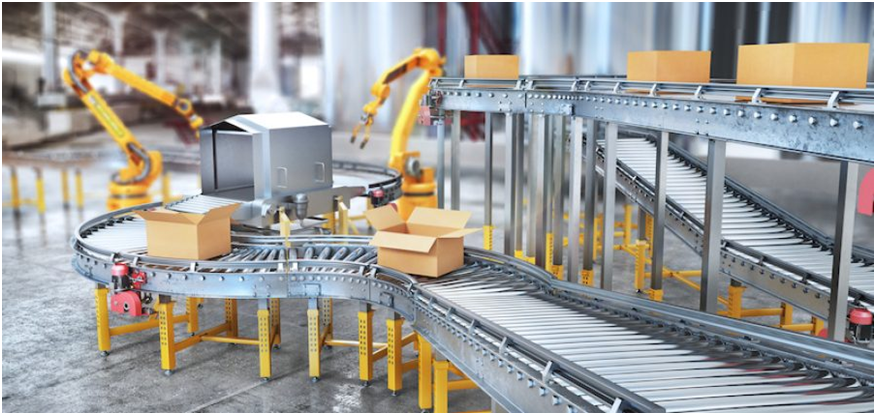
Charles R. Goulding and Ryan Donley consider how 3D printing can help overcome large companies’ supply chain woes.
The past year has shown both how fragile and resilient the global supply is. Consumer demand is at record levels especially for durable goods such as bikes, camping and hiking gear, boats and boating equipment, as well as exercise equipment. The increased demand has challenged manufacturers as the global pandemic has restricted every level of the supply chain. From factory production lines to shipping and receiving logistics, manufacturer slowdowns are compounded daily.
Supply chain disruptions impact even the prominent durable goods manufacturers such as Polaris Industries and Whirlpool Corporation who, in each of their respective fields, have restricted their output despite seeing a sharp increase in consumer demand for their products. The challenges that both companies are experiencing was featured in a recent Wall Street Journal article. However, these companies are strategically positioned to overcome some supply chain pressures since, in recent years, they have infused more 3D printing into design and production processes.
A summary of Whirlpool and Polaris’ overall R&D spending is shown below:
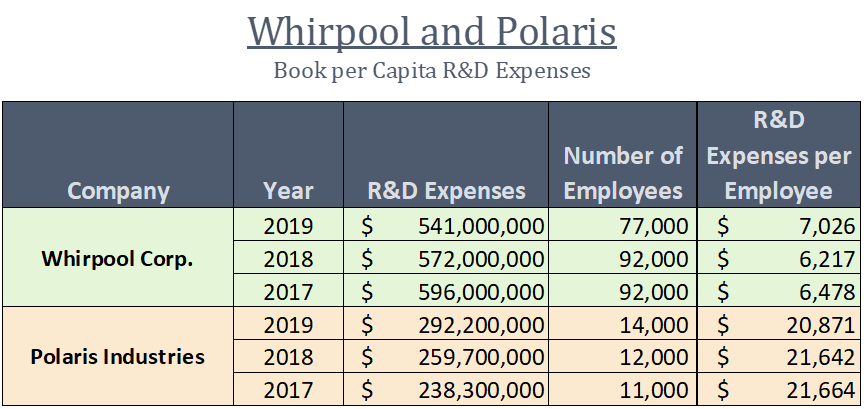
Whirlpool Corporation
Whirlpool Corporation is a multinational manufacturer of durable goods in the home appliance segment. The New York Stock Exchange publicly traded company is valued at over $21 billion and operates well-known subsidiaries such as Maytag, KitchenAid, and JennAir. Whirlpool has largely been hindered by the COVID-19 pandemic. According to CEO Marc Blitzer, “Adding space between workers has slowed appliance output, some appliances will be in short supply until at least halfway through 2021.”
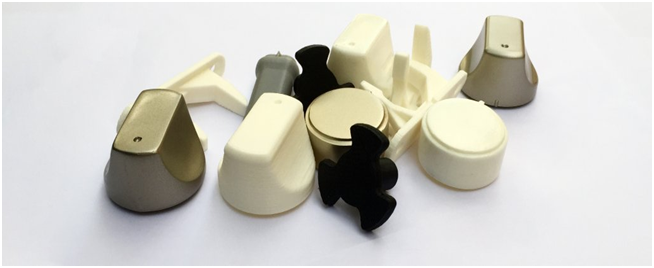
Nonetheless, Whirlpool can meet the demand of numerous spare part batches as in November of 2018, the company partnered with Spare Parts 3D to incorporate 3D printing throughout their processes. Since then, the company has expressed intent on the expansion of additive manufacturing practices into larger parts and batches of production. Partner Spare Parts 3D shared similar goals, specifically to enlarge the process of digitization to encapsulate a larger pool of parts. The ability to significantly reduce production time and cost for spare parts in-house provides some relief for overall appliance production, especially given the current state of the pandemic.
Polaris Industries
Polaris Industries is an American manufacturer of boats, motorcycles, snowmobiles, and other recreational vehicles and is a New York Stock Exchange publicly traded company that is valued at over $5 billion. Polaris is another company that has seen a sharp increase in consumer demand during the pandemic as, according to the company, 700,000 new customers were added with a large portion coming from the sought-after young consumer demographic. Between the novel coronavirus pandemic and increased demand, Polaris’ production has fallen short and is actively seeking to overcome production issues by adding third factory shifts and placing employees directly with suppliers.
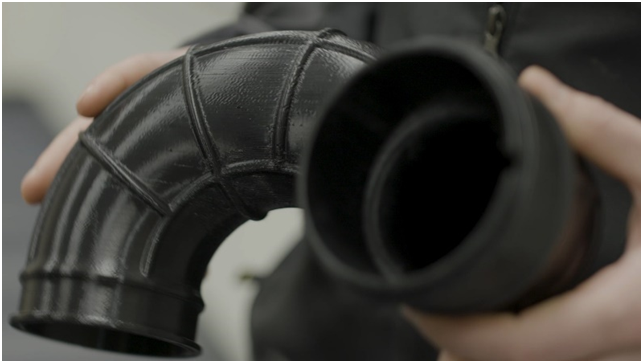
Polaris, similar to Whirlpool, has integrated 3D printers into their processes for part production. In 2019, Polaris added more Stratasys 3D printers, expanding upon their initial 2014 investment into the 3D printers which were used to revive well-known classic motorcycle brand, Indian Motorcycles. Since the initial experimentation into 3D printing, Polaris has been at the forefront of the technology, leveraging it to innovate on products. 3D printing has reduced their design process time to just 24 hours in some cases whereas the previous average was 8-12 weeks. According to Polaris Systems Engineer Will Fickenscher:
“This lets you have more design process upfront, so you have greater confidence when you kick off your final tools for production. As well as reduced tooling times, Stratasys technology allows us to cut costs significantly. It means we can stretch it into other areas where we wouldn’t have previously considered 3D printing.”
The flexibility and adaptability of 3D printing within Polaris’ production should assist the company in aiding their production woes.
The Research & Development Tax Credit
Whether it’s used for creating and testing prototypes or for final production, 3D printing is a great indicator that R&D Credit eligible activities are taking place. Companies implementing this technology at any point should consider taking advantage of R&D Tax Credits.
Enacted in 1981, the now permanent Federal Research and Development Tax Credit allows a credit that typically ranges from 4%-7% of eligible spending for new and improved products and processes. Qualified research must meet the following four criteria:
- Must be technological in nature
- Must be a component of the taxpayer’s business
- Must represent R&D in the experimental sense and generally includes all such costs related to the development or improvement of a product or process
- Must eliminate uncertainty through a process of experimentation that considers one or more alternatives
Eligible costs include US employee wages, cost of supplies consumed in the R&D process, cost of pre-production testing, US contract research expenses, and certain costs associated with developing a patent.
On December 18, 2015, President Obama signed the PATH Act, making the R&D Tax Credit permanent. Beginning in 2016, the R&D credit can be used to offset Alternative Minimum tax for companies with revenue below $50MM and, startup businesses can obtain up to $250,000 per year in payroll tax cash rebates.
Conclusion
Manufacturers are facing unprecedented demand at a time where supply chains are fragile. Companies that are short on parts inventory are expanding their capabilities with innovative additive manufacturing processes and are proving to be resilient against shortages throughout the supply chain.