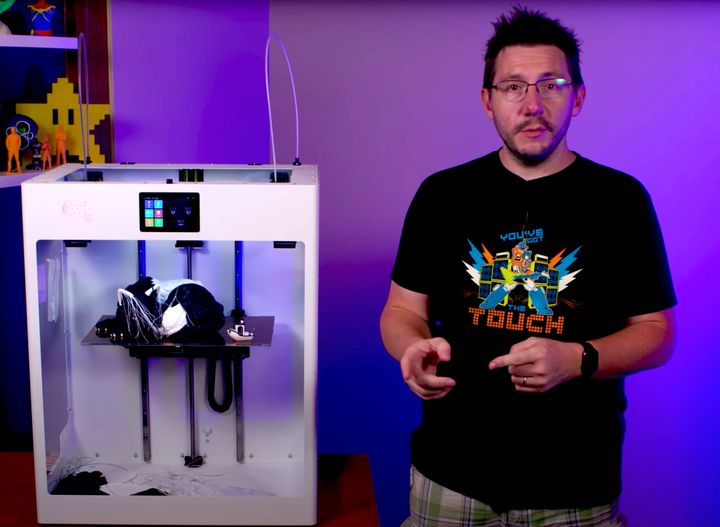
I’ve been watching Fabbaloo friend Joel Telling’s series of videos on his testing of the Craftbot FLOW IDEX XL, and the process seems quite familiar to me.
Joel’s popular YouTube channel, “3D Printing Nerd”, is filled with videos of him reviewing a cascade of unusual 3D printers. Usually they’re smaller desktop machines, but occasionally he encounters a larger device, such as he’s been looking at recently, the Craftbot FLOW IDEX XL.
This is an interesting industrial machine that offers a huge build volume and, most notably, dual independent extruders. These would permit advanced job styles such as two-at-once prints, mirror printing or, if suitable GCODE generation was available, two-printheads-on-one-model printing, but that’s another story.
In his most recent episode, Joel encounters a number of technical challenges with the massive Craftbot. Persistent issues with the right-hand extruder caused him to disassemble and reassemble it several times. He found, deep inside, a bent pin that apparently caused at least some of the issues.
The manufacturer suggested this could have been caused by shipping damage, so replacement parts were swiftly dispatched from Craftbot’s HQ in Budapest, Hungary.
However, once Joel began replacing the hot end he discovered to his horror that the replacement hot end was already jammed! Somehow this hot end had been tested, but the filament was not properly removed, and it was subsequently sent out as a replacement part.
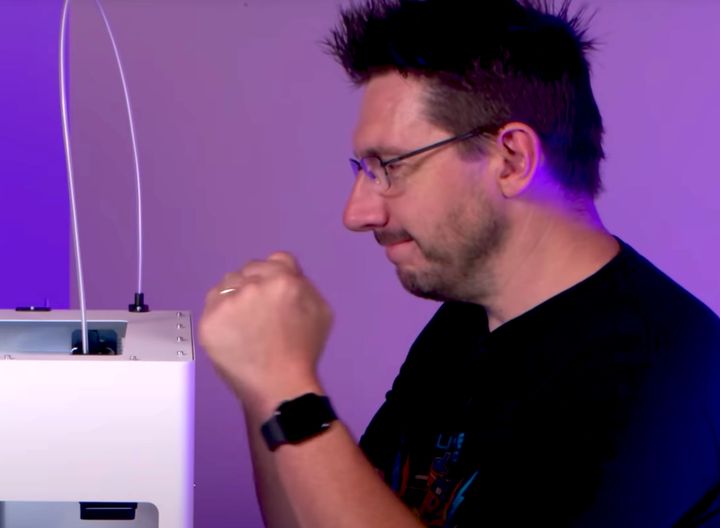
To his credit, Joel maintained his cool throughout the experience and gave Craftbot the benefit of the doubt. However, he said:
“I get it. I mean a company wants its products shown in the best light possible. But the problems experienced on the stream were unfortunate, and it’s very possible that those problems were caused during shipping.
The clogged nozzle sent as a replacement part was more of a serious oversight. And my worry is that if I, as the reviewer, with an audience, gets the clogged nozzle, then what does non-reviewer without an audience receive?
My hope is that all of these issues are just a string of accidents and not indicative of a larger problem.”
I encourage you to give this whole video a watch, as well as Joel’s previous videos on the Craftbot equipment.
Reviewing 3D Printers
Reviewing 3D printers is something we do here at Fabbaloo as well. In fact, we have published well over 80 3D printing reviews, many of which involve 3D printers.
Shipping damages can and do actually happen, and I’ve personally experienced this. Perhaps the most notable and revealing incident involved a CubeX 3D printer years ago. We sequentially received not one, but two devices that had significant shipping damage.
I discussed this with the manufacturer in the UK, and found that they had specifically designed the shipping box to account for the forces expected, as provided by the shipper. However, after sending them images of the box and shattered contents, they realized the shippers were fooling them. They changed their box design and fixed the issues.
This is all to say that most manufacturers don’t truly understand how to ship devices until they actually do so. Only then does the equipment truly experience actual shipping environments.
This is compounded by reviewers, who often are the very first to receive new devices, in newly designed shipping boxes. It’s common to receive broken equipment or even have contents missing.
Fortunately, most vendors are very happy to quickly rectify the situation, and, like Joel, I hope they all provide similar service to anyone purchasing their products.
In most cases a vendor will provide a point of contact for the reviewer to guide them through problems. I almost always end up contacting them because I’ve found something unusual or somehow broken something in the course of the review. Usually they are quite helpful, and if an issue was legitimately an accident, I typically won’t bother reporting it because buyers likely won’t experience it.
But then after publishing the review, I’ll often receive questions from readers using the same device asking ME questions about how to use it, simply because the vendor isn’t taking the same time to work with their real clients as they did with me.
There are a couple of points here that all 3D printer companies should follow.
First, make sure you have products that actually work. This requires considerable testing with internal friendlies, and should be comprised of the entire experience — including shipping — and not just using the machine.
Secondly, manufacturers should recognize that buyers will have issues. Be ready to receive them and help the clients move forward. They had confidence in the products, so the manufacturer should be able to offer similar respect and service. Of course, any issues encountered should always be followed up and rectified for future shipments.
Meanwhile, I’m curious to see Joel get the Craftbot in operation.
Via YouTube