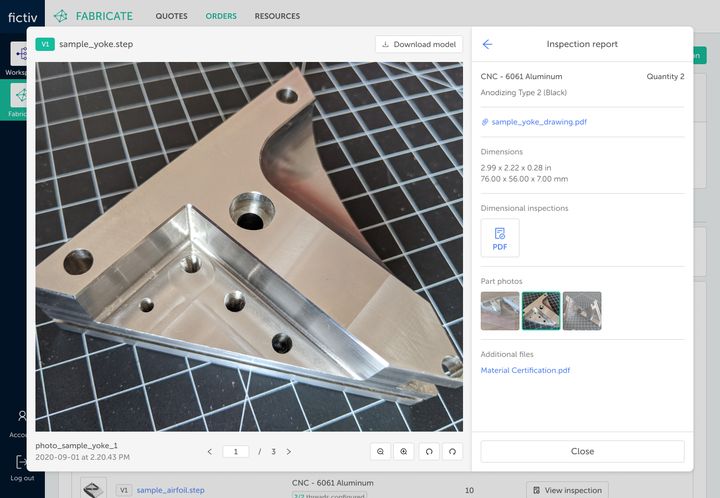
Fictiv announced a comprehensive set of transparency features that should fit well into the current state of the world.
If you’ve not heard of Fictiv, they are a manufacturing network, composed of a group of vetted partners that provide making services to the network. Clients are connected with a partner for each project to produce the goods.
Clients would use them to produce products, either prototypes or production units, when it’s more feasible than doing so internally. However, this introduces a bit of an issue: do you really know what’s going on at the manufacturer?
Manufacturing Transparency
This is an especially challenging issue for those contracting with overseas manufacturers. You place your order, but do you know anything about what’s happening before the items show up at your door? What happens if there was a mistake along the way, or something was not accounted for?
It would be better to be closer to the action in order to ensure those and other factors were resolved before large quantities of products were produced. That’s easy to do when the manufacturing plant is on-site, but a lot more difficult if it’s in another company, perhaps far away, or even overseas in a completely different time zone.
Even worse, the current pandemic has put in place a variety of constraints that add even more challenges to this puzzle. You can’t easily visit a factory anymore, especially if it’s in another country. Sure, you may be able to legally travel, if you’re willing to take virus risks, but what if the rules change and you’re trapped somewhere?
Because of this many manufacturing services have become a bit more opaque than they already were.
Fictiv Transparency
Those issues will now be substantially reduced with Fictiv’s new transparency initiative. They say:
“Fictiv today unveiled industry-first features that deliver unprecedented visibility, traceability, speed, and quality benefits for customers leveraging its Digital Manufacturing Ecosystem (DME) to order high-tolerance, custom mechanical parts for both prototyping and production needs. In response to evolving customer work-from-home requirements as well as more compressed NPI timelines, Fictiv’s new radical transparency initiative brings into focus the otherwise opaque nature of traditional onshore and overseas manufacturing and introduces significant risk mitigation and cost-savings opportunities.”
This sounds good, but what does this mean, exactly?
Specifically Fictiv is introducing the following:
- On-Demand Production Status: detailed current production status of all the parts within every order, immediately and online
- Virtual Inspection Photos: inspection photos from manufacturing partner facilities, before the parts are delivered (see example above)
- Centralized Access to Quality Documentation: material certifications, certificates of conformance, and inspection documentation all available in one place
- Order Configuration Details: centralized access to 2D and 3D design files, thread specifications, material and process configurations, and invoices for all Fictiv orders
- Historical DFM: digitally call up previous manufacturability feedback for all ordered parts to inform future design cycles
- Reorders: streamlined quoting process to reorder parts and lock in previous pricing
- Shipment Tracking: aggregate tracking links from third-party providers to keep all shipments in one secure place
While some of those features may be present in other services, Fictiv is putting together a great package of services that use might raise the bar for other services.
After all, if you had the choice to work with an opaque service provider or one that provided some level of transparency, which would you choose? As soon as a few services do this, I suspect the rest will have to fall in line to keep their clients.
Via Fictiv