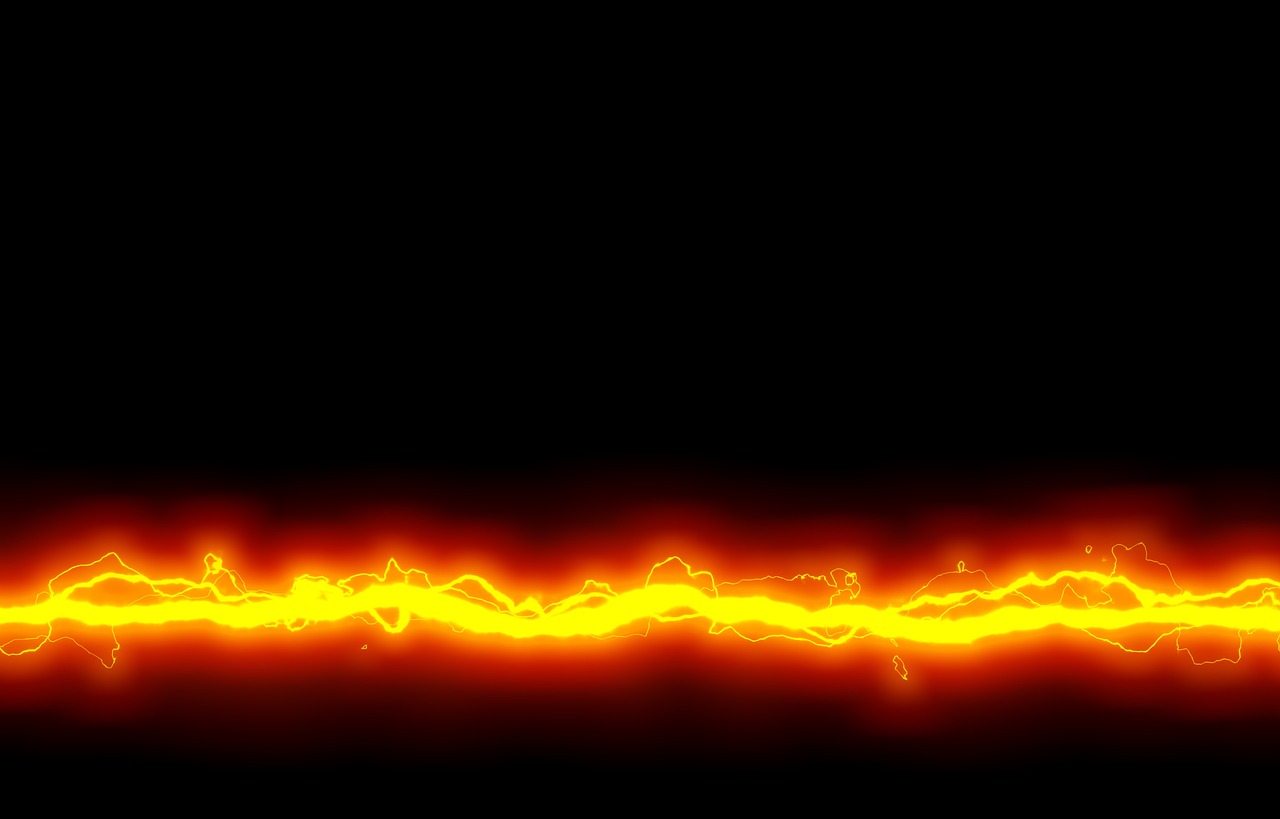
Recently I had a discussion with a maker designing a handheld transmitting device, who insisted on 3D printing with ABS instead of PLA, but his reasons were not what you might think.
Typically, ABS is considered a stronger material for “active” objects than its easier-to-3D-print counterpart, PLA. This is to avoid the brittleness of PLA when the object is to undergo some mechanical stress; PLA might break, but ABS has a bit of “give”.
However, while the maker’s product is a handheld device that would clearly undergo stress from drops, open and closing, etc, his primary interest was not mechanical stress. Instead, it was the dielectric constant of the material.
Wait, what is the dielectric constant? It’s defined as “a quantity measuring the ability of a substance to store electrical energy in an electric field.”
Every material has a dielectric constant (example chart here), and it varies not only by material, but also by material state. If the material is a liquid, solid, granulated solid, etc, it could take on different values. For example, granulated ABS has a dielectric constant of about 1.9, while liquid ABS resin is 2.4.
Why is this so important in this type of project? It’s because the purpose of the handheld device being developed in this situation is to transmit and receive electrical signals. The “guts” of the device is on a printed circuit board inside the case – which is made from 3D printed plastic. Thus, the electrical signals must pass through the plastic case.
Having different dielectric constants materially affects the quality of the signal, and subsequently the device’s performance. For example, range, sensitivity and signal quality can be affected adversely – or positively if the “correct” material is used.
In this case, the maker was able to 3D print his prototype case in PLA to test for “fit”, but not for electrical performance.
It gets even worse, as specific ABS mixes can have different dielectric constants! So you must have the specifications listed for the material being used. Unfortunately, by far the majority of 3D printer filament vendors do not state such specifics, leading to some prototyping challenges. But that’s a story for another day.