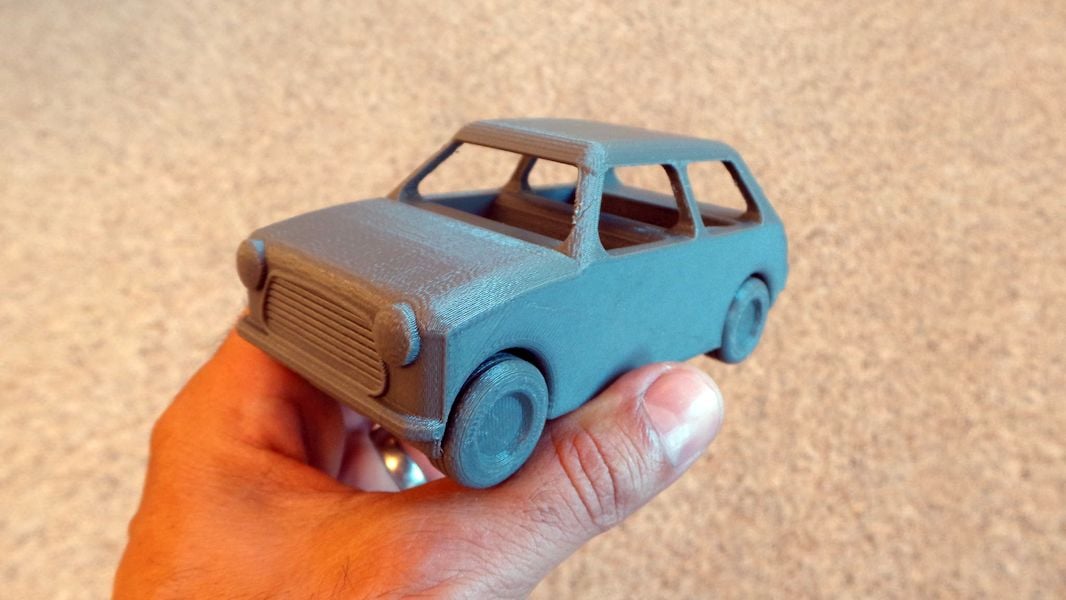
The automobile sector is booming.
According to a recent study, the automotive industry will reach the light vehicles sales volume of 114 million units in 2024. But, considering the emerging environmental and economic concerns, the automobile industry has to rethink the way it functions today. Fortunately, there are several different ways to improve production without compromising quality while keeping the costs and wastage down.
Among the various technologies being explored in this regard, 3D printing technology has caught the attention of industry leaders. It is playing a critical role in reshaping the automotive industry. According to Frost & Sullivan, the global 3D printing materials market in automotive transportation will reach the revenue of $576.5 million by 2024, with an impressive compound annual growth rate (CAGR) of 17.8% between 2017 and 2024.
Here are four ways 3D printing is revolutionizing the automobile industry.
1. Fast and Inexpensive Prototyping
3D printing has opened up the possibility of fast and inexpensive prototyping. Armed with this technology, you don’t have to worry about creating molds or setting up specialized machines to manufacture new parts. From steering wheels to the breaks, you can use a single 3D printer to build prototypes of any car component.
Though in its infancy, many automobile manufacturers are using 3D printing for prototyping. In 2016, Volkswagen Autoeuropa began to 3D-print parts for its machines that create car parts. They produced more than 1,000 machine tools saving $160,000 in assembly line components. They are presently using 3D printing to create gear shifters, water connectors for engines, and metal components that connect door handles to leather interiors.
General Motors is also using 3D printing for rapid prototyping. Using this technology, they have managed to produce lighter but more durable parts in a relatively less time. GM has averaged a weight loss of 350 pounds across 14 new vehicles it has introduced since 2016.
2. Personalize Cars through Custom-Fitted Parts
Customization has been one of the most essential aspects of the automobile industry. Most people are interested in adorning their cars with customized elements. 3D printing has a promising potential on this front. With 3D printing, car owners can get customizations done from manufacturers itself. They won’t have to rely on local mechanics or third parties.
BMW, the premium British car manufacturer, is already leveraging 3D printing along with laser lettering to produce individualized accessories and products for a selected range of MINI series. The service called MINI Yours Customized is quickly gaining momentum among BMW customers. As of now, the customizable product range includes the indicator inlays or side scuttles, trims for the passenger side in the interior, LED door sills and LED door projectors. Consumers can select, design, and order the new parts through an online portal.
High-end carmakers such as Rolls Royce are thinking of using this technology to make fully customized cars for their wealthiest clients. Their long-term goal is to build large spare-parts or even body parts using 3D printing. Amateur grease monkeys, on the other hand, can also use 3D printing technology to create custom car parts of their own making. Local mechanics can also learn to use this technology to provide better service at an affordable rate.
3. Restoring Vintage Car Models
3D printing will not only revolutionize the future of automobile industry but also help revive its historic milestones by restoring vintage cars. Sadly, restoring vintage cars is easier said than done. One of the most common challenges vintage car owners have to face is the unavailability of the right OEM (original equipment manufacturer) parts in the event of an accident or damage.
Unfortunately, original drawings of the spares are rarely available and traditional manufacturing processes are often cost prohibitive. But, in the past few years, 3D printing technology is changing this situation and helping people breathe new life back into their old cars. For example, local automobile engineers in Australia managed to bring the only surviving 103-year-old 1914 Delage Type-S Grand Prix car back on the road using 3D printing. Designers scanned the engine block inside and out and created a 3D model. Based on this model, a 3D printer produced a sand mold, which in turn, was used to forge the engine block.
Another successful restoration took place in the UK when a British shop called Classic Motor Cars used 3D printing to revive a 1954 Jaguar XK120 SE. Body parts such as rear window apertures, window screens, mock-ups of the lights, and several smaller missing items were 3D printed during the restoration process.
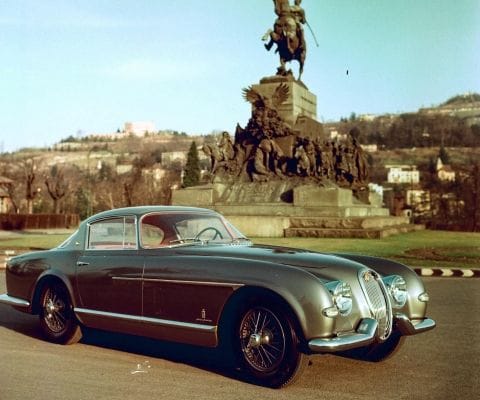
3D printed parts not only save money on restoration but also eliminate the guesswork of reverse engineering. The detailed 3D scan can record every bump, curve, and deviation, delivering more accurate results compared to traditional methods. The good news is 3D printing service providers and restoration companies are slowly but steadily coming together to attract vintage car collectors and car museums.
4. Improved Supply Chain Management
It takes thousands of components (that come in all sizes) to build one car. Usually, all these elements are sourced from suppliers located across the globe. In other words, supply chain management is the backbone of automobile manufacturing. Unfortunately, today’s spare-parts inventory management in automotive industry is data-heavy, cumbersome, and relies heavily on bulk production. It often leads to increased costs and reduced efficiency as millions of spare-parts keep sitting on the shelves for weeks or even months.
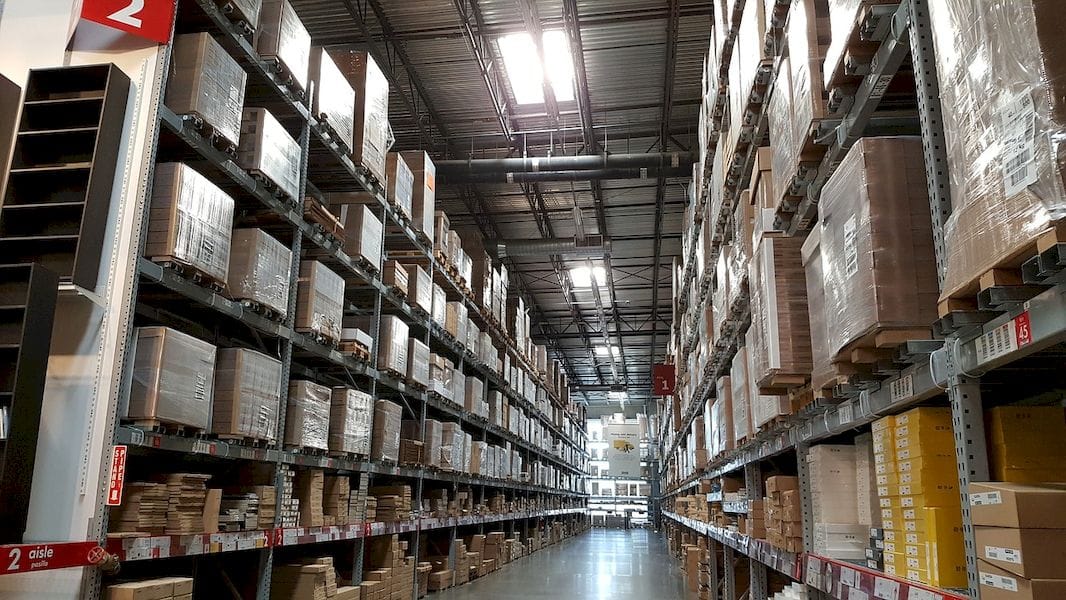
With the help of 3D printing, however, manufacturers can store these spare-parts digitally and produce them on-demand. Daimler EvoBus is already using 3D printing to improve its supply chain management. The spare-parts are 3D printed to avoid excess production and save the storage space and cost. In just nine months, the company was able to filter out around 300 plastic parts and more than 100 metal parts suitable for 3D printing. Presently, they are in the process of digitalizing the supply chain accordingly.
Parting Words
3D printing has already started changing the automobile manufacturing landscape. Its prominence will only rise as the technology becomes further sophisticated and affordable. Hopefully, the points enlisted in this article will help you understand that the impact of 3D printing on automotive sector goes well beyond just aesthetics. With so many leading brands exploiting this technology to the best of their abilities, it is bound to become an integral part of the automobile manufacturing process in coming years. What do you think? Tell us in the comments.