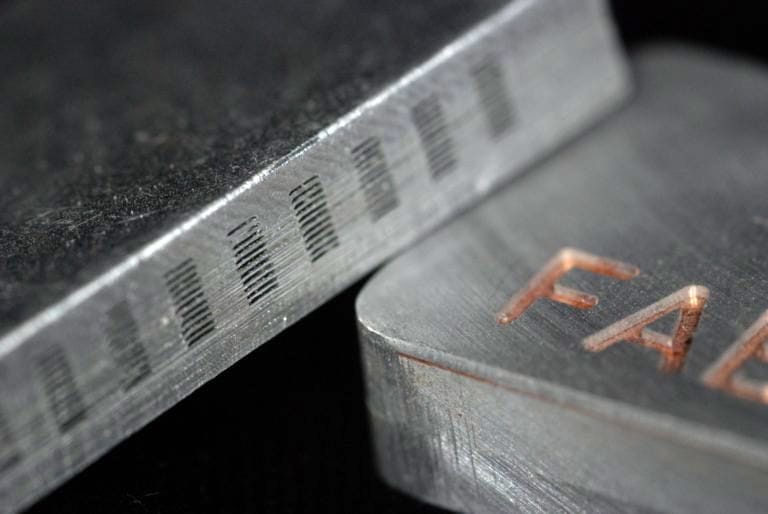
A piece from Fabrisonic explains how their process might be better than others, but it suggests a pattern across all 3D printing processes.
Their article, entitled, “The Top Five Reasons to 3D Print Your Next Heat Exchanger” contains some profound reasons why 3D printing truly is a better technology in many ways, and these reasons are not applicable to Fabrisonic only.
They list these five advantages of 3D printing in the production of heat exchangers, but really they fit for any 3D printing scenario:
- Complex channel paths: The ability to create tiny embedded within a part. Traditional making would require multiple (sometimes many) separate parts to accomplish this, if it were possible at all.
- Simplicity: By 3D printing all the functions in a single part, the process of assembly can be reduced or even eliminated. This is a powerful capability that carries value far past the printing stage.
- Higher performance: Advanced designs, previously impossible, enable higher performance parts.
- Customization: Without the constraint of “tooling up”, 3D printing can enable easy customization for job runs, or even individual parts.
- Time to Market: Traditional manufacturing can take considerable time to get going due to setup efforts, but that’s largely eliminated with 3D printing technology.
Those are true for almost every 3D print technology. However, what Fabrisonic didn’t say was that 3D printing typically carries a higher per-unit cost when larger quantities of parts are required, thus traditional manufacturing has plenty of road left.
Here’s where it gets interesting: Fabrisonic uses an ultrasonic method of 3D printing, in which they molecularly fuse thin layers of metal together with the vibration of powerful sound waves. You can even fuse together materials that otherwise wouldn’t easily be combined. Their technology is quite different from most other 3D metal printing approaches, which typically use powder, lasers and binders.
This results in Fabrisonic having some capabilities that the others don’t, and vice versa.
For example, in the heat exchanger example, it would be possible to introduce different metals into a Fabrisonic print; there is no requirement for the input materials to be identical metal sheets. This means that you could theoretically design a part that had changes in metal throughout its structure, at least layer by layer.
This allows Fabrisonic users to engineer a part that has unique thermal properties, for example, by carefully arranging these layers of differentiated metal.
Their process also allows for print operations to pause for the insertion of non-3D printable items like sensors, switches or other gear.
That’s all quite interesting, but here’s the point of all this discussion: While most 3D printing processes offer the significant benefits Fabrisonic listed above, each specific 3D printing process offers different capabilities. All have advantages and disadvantages.
It’s up to the designers to consider the particulars of each part and then match them with the optimum 3D printing process. They know what properties of a part are most important, and thus can suggest which process is most appropriate.
In the Fabrisonic example, it may well be that their process could be better than others for production of certain types of heat exchangers. But for another part, it may be that another vendor’s 3D printing process may work better.
Know your part; choose 3D printing processes wisely.
Via Fabrisonic