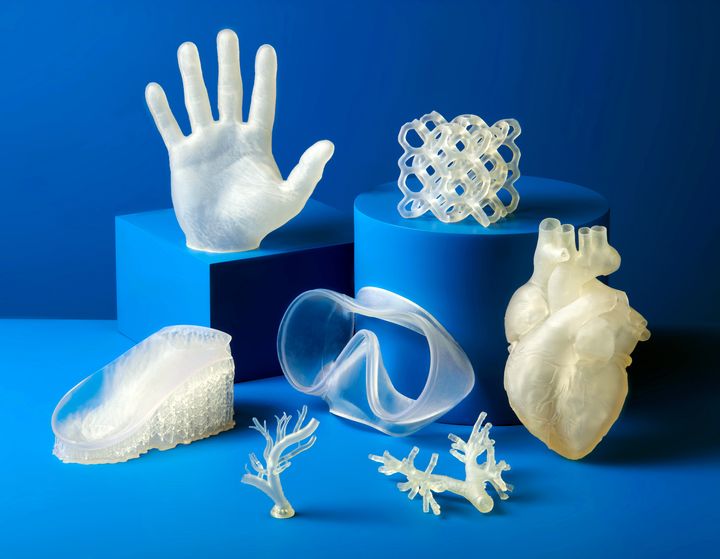
Formlabs today announced a series of powerful industrial materials in a new set of product families.
Formlabs manufacturers the Form series of SLA-style 3D printers, which are highly regarded by their users. From humble beginnings in a 2013 Kickstarter campaign, the company now is one of the leaders in desktop 3D printing. While initially servicing hobbyists, the company has shifted towards industry, and that has largely been facilitated by materials.
When Formlabs first announced the resin materials for their desktop 3D printers years ago you had choice of, well, gray material. Yes, only one. And they didn’t even describe the actual properties of the material because it didn’t really matter.
At the time Formlabs followers were thrilled by the subsequent introduction of clear and black materials. Again, the nature of these materials showed the function of the system at that time was really for simple prototyping or hobby use.
That all changed, as Formlabs repeatedly introduced increasingly sophisticated materials for their equipment.
I recall long ago hearing from an attendee at a 3D print trade show, who bluntly said they “would only buy a 3D printer if it was able to 3D print in [some specific material]”.
That statement really hit me: If you could not produce an item that had the necessary function, there was no point in 3D printing it. At that moment in my mind the 3D printing world was divided into two parts: the space where you could print things using materials that worked for the application, and the empty space where there were no suitable materials.
The key to 3D printer success then was to fill that empty space with new industrial materials that would in fact meet the needs of specific applications. Then, and only then, would clients buy more 3D printers to make use of those new materials.
This is the main strategy of several 3D printer manufacturers, including Formlabs: increase the breadth of material offerings to enable more industries to make use of the equipment. Then sell them the equipment.
Today’s announcement follows that strategy precisely and quite boldly, as the company announced not one material, but several FAMILIES of materials. Let’s take a look at what they’ve produced.
Formlabs Flexible Family
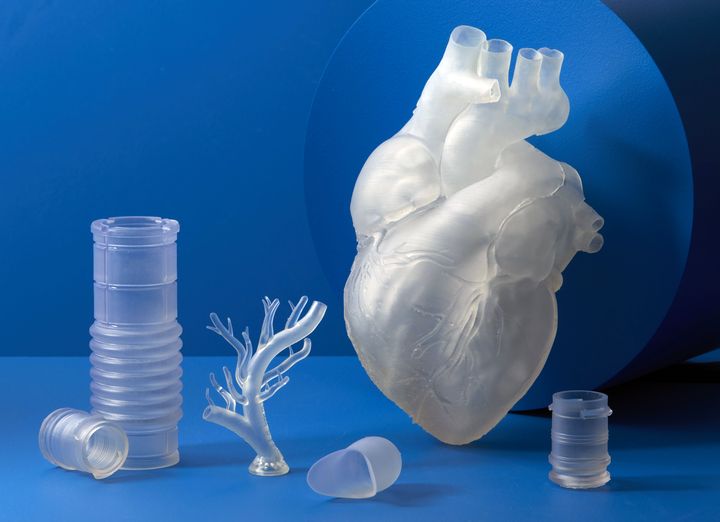
This is a new set of resins to replace the company’s previous flexible options. The new resins include:
- Flexible 80A Resin: Formlabs has remixed their previous flexible material into this new offering, which, as you might guess, has a shore durometer rating of 80A. It’s able to bend and flex through “repeated cycles”.
- Elastic 50A Resin: This is a brand new resin that has elastic properties. In other words, when bent or compressed it will spring back to its original shape without tearing, again able to do so for “repeated cycles”.
These two resins should form an excellent set of options for the two main types of flexible material: flex and elastic.
Formlabs BioMed Family
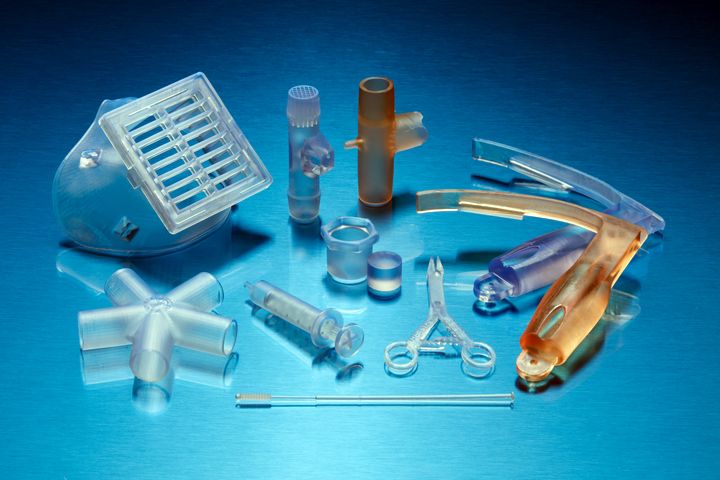
The BioMed Family is intended for medical applications and thus each member holds properties and certifications necessary for such use. For example, objects made with these resins can be sterilized using approved methods, whereas some 3D prints cannot withstand the temperatures of sterilization.
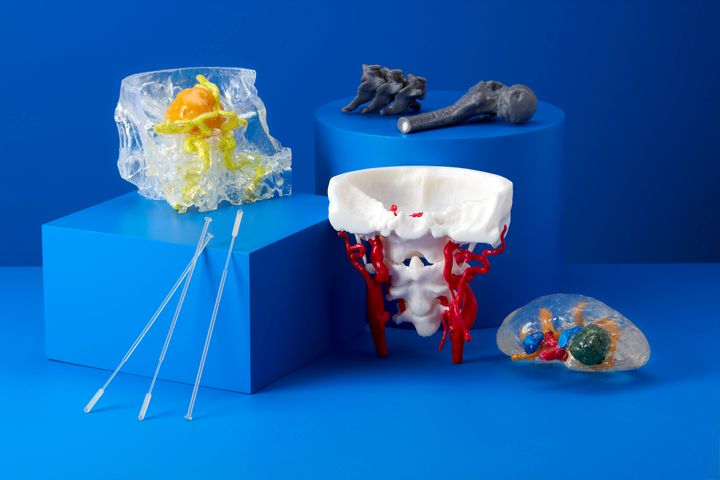
There’s two material in the BioMed family so far, starting with BioMed Clear Resin, which is certified to USP Class VI and targeted for long-term skin or mucosal membrane contact. Formlabs also explains this material is produced in their ISO 13485 manufacturing facility, ensuring it meets certification criteria.
The second BioMed material is BioMed Amber Resin, which is targeted for short-term skin or mucosal membrane contact.
Both can be used for a variety of healthcare and research applications.
Formlabs Dental Resins
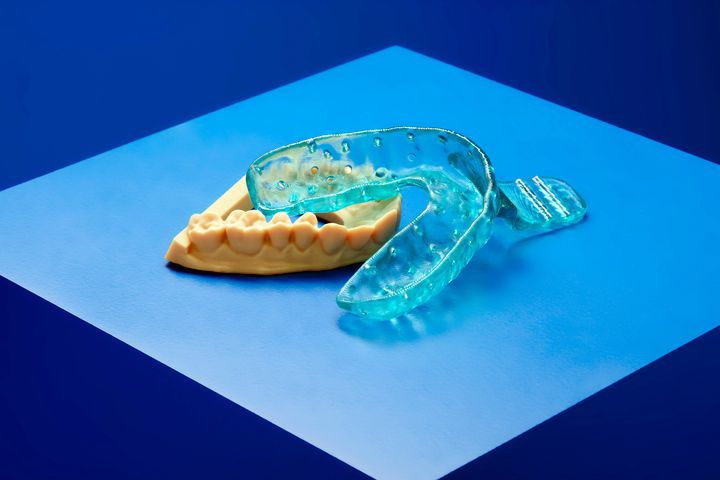
Finally, Formlabs announced several resins to add to their growing complement of dental resins. The new resins include Dental LT Clear V2, an upgrade on their previous formulation.
There’s also Custom Tray Resin, which doesn’t have anything to do with Formlabs’ 3D print trays. Instead it’s for dental impression trays, the terminology used in that industry. With this resin a tray can be produced in less than an hour, enabling the possibility of dentists using them almost in real time with patients.
Finally, there is Temporary CB Resin, used for directly 3D printing temporary dental crowns and other dental appliances. The material is available in four VITA shades, and should last up to a year in patients.
Formlabs Materials Strategy
It is quite likely Formlabs will continue to grow their business in these applications areas as their value proposition is significant. The company has competitors in each area, but they are typically higher priced and have more specialized resins. With these new materials and future announcements, it seems that Formlabs is catching up fast.
Via Formlabs