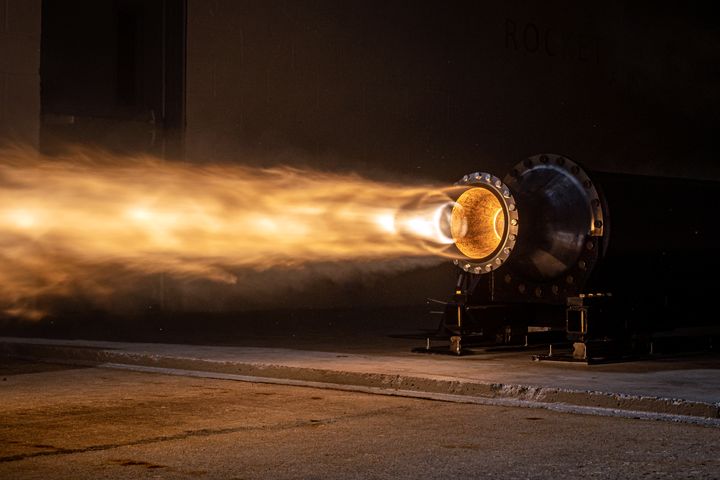
It’s been quite a while since we last wrote about Rocket Crafters — four years, to be exact — but they’re back in the news with some new 3D print testing.
The company is not alone in the rocket engine industry, but they are unique in one very intriguing aspect. They say:
“We print rocket fuel!”
And it’s true: their highly unusual 3D printed rocket engine design includes use of 3D printed solid rocket fuel.
3D Printed Rocket Fuel
I explained Rocket Crafters 3D printed fuel concept a few years ago:
“One contributing factor to their plan is the use of 3D printing technology, and specifically in their solid-fuel booster. In a solid-fuel booster, the burnable material is cast into a long combustion chamber, where it burns to produce thrust.
The challenge with solid fuel is that once you light it, it isn’t going to stop burning until it runs out of fuel. Normal solid fuel boosters have a uniform layer of fuel pasted against the sides of the chamber, and the burning occurs from the center outward in an even manner. This provides uniform thrust throughout the flight.
However, this is a problem: optimal flight patterns require the ability to jog the thrust higher and lower as various layers of atmosphere are penetrated. Since normal solid-fuel boosters are constant thrust, the flight profile has to go with the “lowest common denominator”.
But Rocket Crafters’ ingenious idea is this: 3D print the solid fuel in a burnable pattern that matches the optimum flight profile! In this way they can “throttle down” through the denser portions of the atmosphere where other solid fuel boosters cannot.
I can imagine they could design custom burn patterns for various flight profiles, each providing the most cost effective approach. It should enable them to make more effective use of solid fuel technology, which is far simpler to build than liquid fuels used by other rocket systems.”
Their engine design is quite interesting in that it does not include the highly complex turbo pumps that other engines use. Instead they have use only two moving parts! They say:
“The STAR-3D engines are so mechanically simple that they include only two moving parts, a main on/off valve and the throttle valve. The engines use differential pressure to maintain pressure in the oxidizer tanks: high-pressure Helium pushes the Nitrous into the engine; just like squeezing a tube of toothpaste. The engines can then be throttled by regulating the amount of oxidizer entering the engine, allowing thrust to be adjusted as needed.”
Rocket Crafters Testing
This month Rocket Crafters announced the completion of their testing of the new comet engine, which uses the concepts described above. The engine was able to produce a thrust of 5000 lbs, a bit small as far as rockets go, but certainly demonstrating the viability of their unusual engine concept.
Two successful tests occurred, but an anomaly occurred on the third test, resulting in an explosion. The folks from Rocket Crafters performed an investigation and determined that the cause of the anomaly was not in the engine itself, saying:
“After extensive analysis, it was concluded that there was an initial failure in an ancillary part of the engine. This led to a larger over-pressurization inside the combustion chamber. The team found no problems within the core STAR-3D engine design.”
That’s what tests are for: find problems and fix them.
In time Rocket Crafters may be able to scale up their concept to enable larger payloads and take on some of the other players in the rocket industry using 3D printing.
Via Rocket Crafters