When some 3D prints are completed, they are painted; others are dyed.
Plastic extrusion 3D prints are sometimes painted after printing to complete their production, but that isn’t always an effective technique for prints made with the SLS powder process.
SLS, or Selective Laser Sintering, is a process in which a powerful laser sweeps across a bed of powder, typically nylon, to fuse successive layers into solid objects. Nylon prints made with the SLS process are very popular due to their strength and versatility. EOS, 3D Systems and others have developed powerful 3D printers specifically for this purpose.
But the powdery nature of their production results in objects that have a less than smooth finish that’s not the greatest for painting. The finished prints can also be somewhat porous. This presents the opportunity to provide a highly durable color solution that matches the durability of the object itself: dyeing.
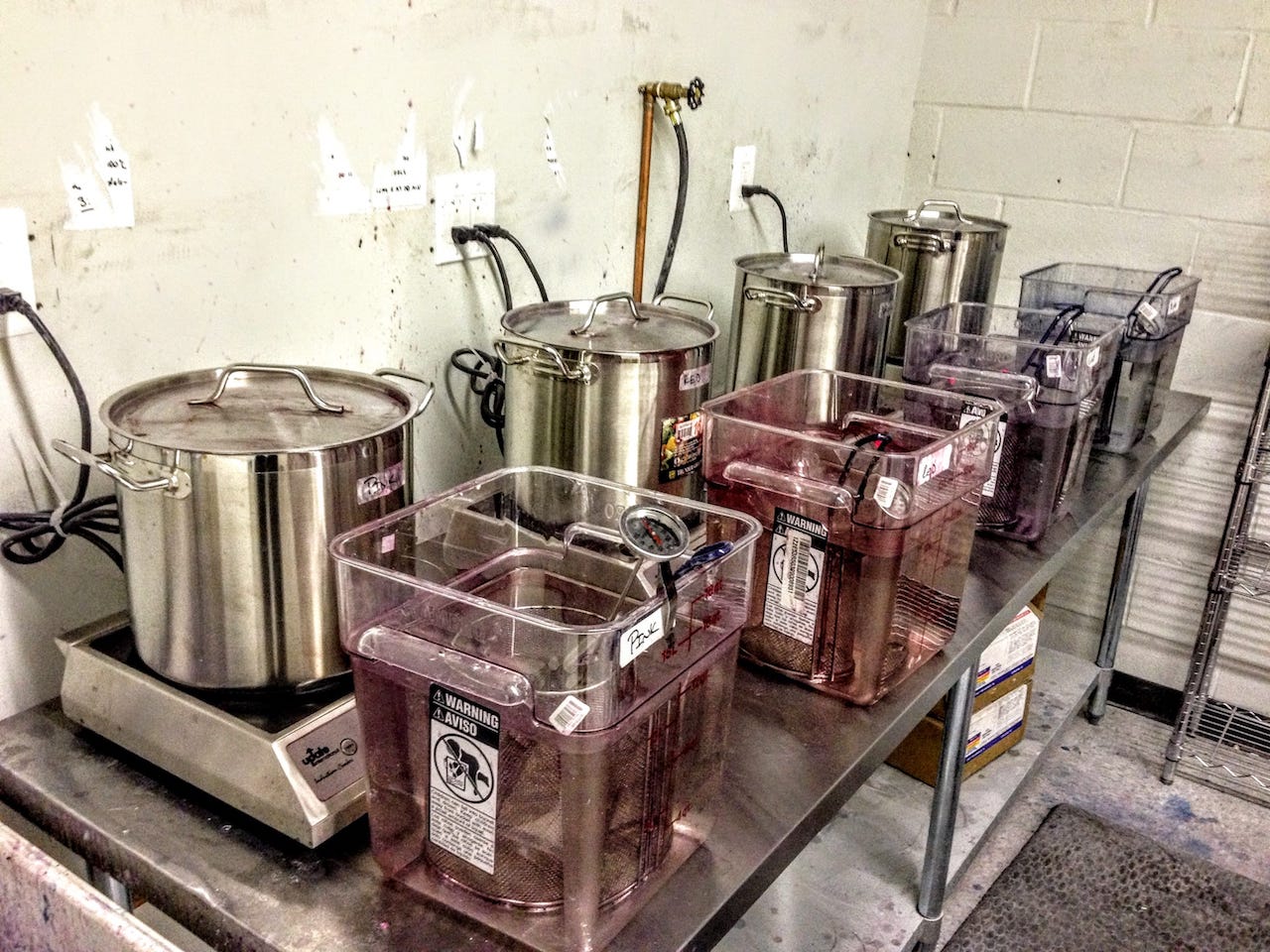
The process of dyeing nylon 3D prints has been done for years. Here’s an image of the dyeing station at Shapeways’ Brooklyn facility, where you can see they’re brewing up specific, repeatable dyeing mixtures that can be applied to prints from their equipment for clients.
As you can tell in the Shapeways example, the process of dyeing has been quite rudimentary. But now there’s a professional solution that’s specifically designed for 3D printing from Dye Mansion.
Dye Mansion (and I love the name, a play on “Dimension”), produces the DM60, said to be the “world’s first automated coloring machine for SLS parts”. Certainly there have been industrial dyeing machines available for decades, but this one is for 3D prints.
The DM60 can handle a variety of nylons as well as TPU plastic. They say the machine has also been observed to successfully dye TPE, PrimePart, PA6, Alumide, PP, ABS and other materials.
The color range is literally infinite. The company says they can produce all RAL and Pantone colors. However, the company provides color cartridges for 17 standard colors.
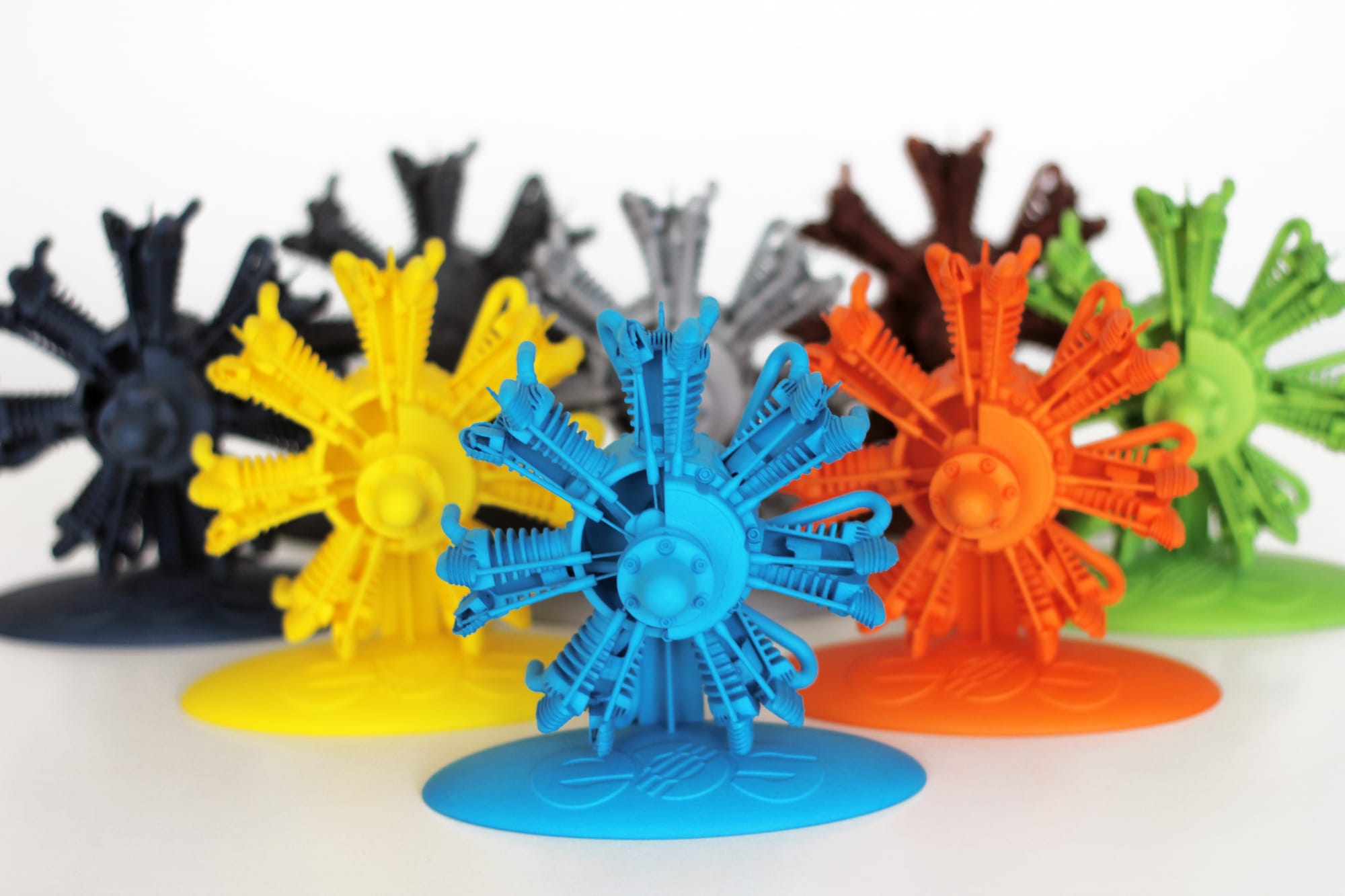
The availability of standard colors is very important, as that is the way by which you can achieve color consistency. If you are mixing your own colors as Shapeways was doing above, you run the risk of having slightly different shades for each batch. That won’t happen with the DM60.
Typically the automated process takes 2.5 hours to complete. Just drop in the parts and hit the start button. The DM60 also includes an automated cleaning program that takes only 15 minutes.
If your operation requires a lot of part dyeing, you might consider an automated solution like the DM60.
Via Dye Mansion