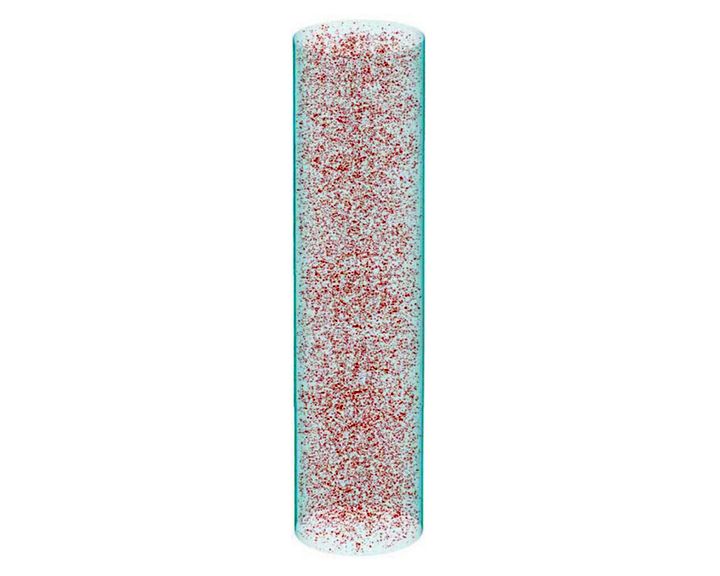
Researchers in the US military have developed a set of tests to determine the strength of 3D printed parts.
The specific material under investigation was Maraging Steel, a specific type of steel commonly used in aerospace, where good strength-to-weight ratios are required. Maraging steel is produced by lengthy heat treatments of martensitic steel.
The problem is that this type of steel, due to its unusual properties, is frequently used in applications where it is subject to repeated mechanical stress. For example, the undercarriage legs of a helicopter will be subjected to vibrations and landings repeatedly.
It would be of great interest if these parts could be tested in some way that could reliably predict whether they are undergoing fatigue, and thus enable replacement before they fail. If one is conservative and replaces the part too early, then you’re spending too much money on replacements. You want to hit the sweet spot for replacing a part.
This has been a challenging problem, and one not easily solved. However, this new research might light the way towards a solution.
The researchers used a bevy of different advanced sensor systems to examine precisely made parts. They printed a number of uniform metal samples using an EOS M 270 metal 3D printer, and prepared them for examination using multiple sensors after undergoing programmed mechanical stress.
Sensor types included: magnetic permeability, digital image correlation and structural compliance measurements.
All of this is really trying to understand the microscopic internal structure of the metal parts. Imperfections in the part result from an inability of the 3D printer to perfectly produce a representation of the desired CAD part. This is a well-known phenomenon, with the most frequently seen instance being the weakness of layer line adhesion in 3D prints, leading to anisotropic behavior.
The ideal is to have truly isotropic parts, and that’s hard to do. Even with a true isotropic part, there may still be imperfections in the part: isotropic imperfections! It’s these that were being sensed by the researchers.
In the image at top is a representation of the voids within a metal 3D printed part. While they are small and more-or-less uniformly spread within the part, they do exist and will contribute to part failure under repeated mechanical stress over time.
While this research is at the early stage and certainly is of questionable practicability in field settings, it’s a good start. Hopefully the techniques can be refined and ultimately integrated into 3D printing production so that parts can be examined in a way to determine an estimated field lifetime.
Via Springer