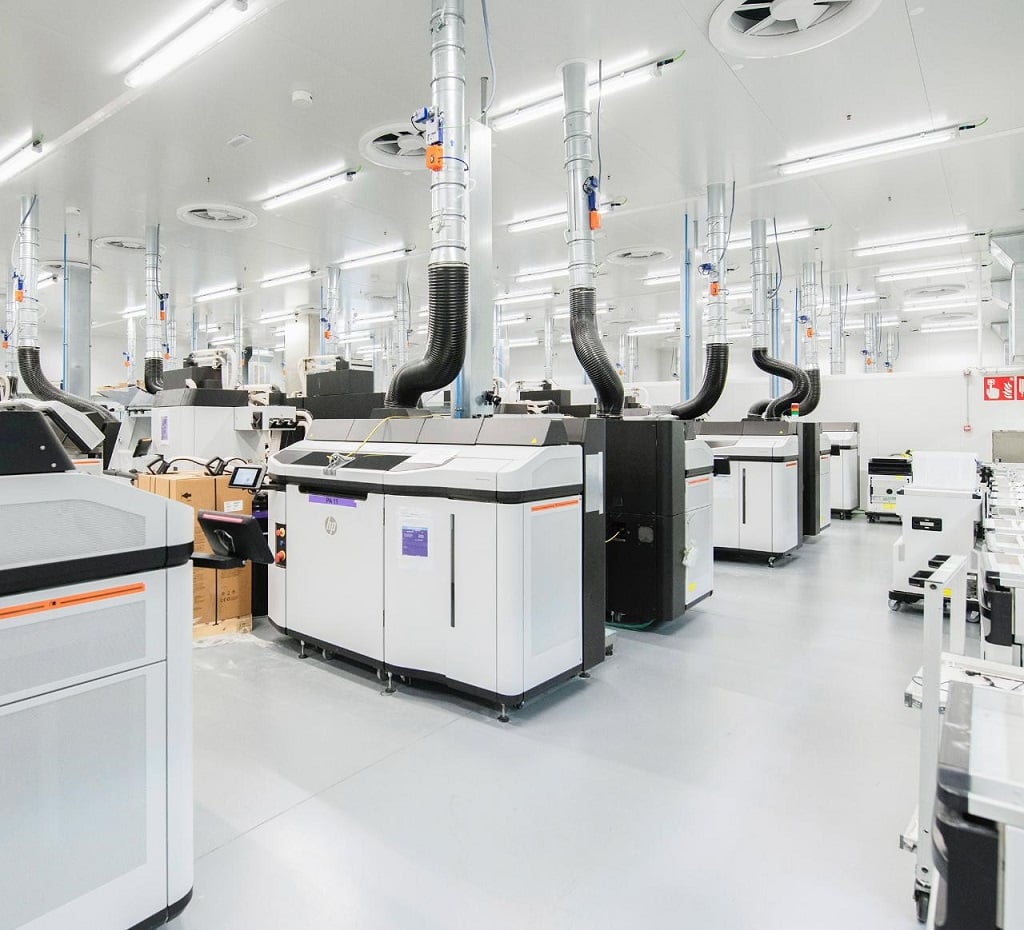
HP 3D Printing and Digital Manufacturing is not, to put it lightly, an operation that does anything by half-measures.
Today the company has a slew of announcements, characteristic of the boldness they favor.
Ramon Pastor, Interim President, 3D Printing and Digital Manufacturing, HP Inc., offered a preview yesterday of today’s announcements — and for more information, HP is working with SME on a virtual event today to detail the latest in digital manufacturing happenings.
A Watershed Moment
In introducing today’s announcements, Pastor called the present time “a watershed moment” for the industry.
2020 has been a game-changer for not only industry, but the world itself. From a manufacturing perspective, we might now see a clear “before” and “after”:
- Old paradigm — Pre-COVID-19
- New paradigm — Post-COVID-19
HP lays it out for additive manufacturing (AM) thusly:
- Old paradigm: AM forging a new manufacturing value chain
- New paradigm: AM fitting in analog manufacturing value chain
- Old paradigm: No customer investment in supply chain innovation
- New paradigm: Customers investing in strategic supply chain innovation
- Old paradigm: Consolidated manufacturing and assembly
- New paradigm: Distributed manufacturing and assembly
Indeed, many of these trends are among those we’ve noticed here. The world is looking at 3D printing in a new light: perhaps this is that tipping point, that watershed moment, that will change the global structure of manufacturing supply chains.
Fully realistically, maybe it isn’t. But it’s still going to be an important point in this timeline of change, an inflection point from which in many ways there will be no return to the “old ways.”
3D printing has come into play to meet immediate supply chain needs, producing critical personal protective equipment (PPE) and other need-it-now items for response to COVID-19. HP has, unsurprisingly, been among those big names working on significant initiatives to meet supply needs around the world, through both internal work and customer and partner collaborations. We’ve spoken to company executives about some of this work, and it’s only continued. Pastor noted that together with more than 30 partners and customers, HP and its global partner network have produced more than 2.3 million parts.
Thus, Pastor said, people are really “seeing the power of flexible manufacturing.” For its part, he noted, “we realized we have to use our knowledge of additive manufacturing technologies for this crisis,” as the company and its partners made products in “days and weeks,” which is “unheard of in the medical industry.”
Such fast-acting need is indeed at the heart of many of these announcements, as HP is now relying on the insights and data gathered to continue to innovate. Pastor pointed to three key areas of focus:
- Economics
- Manufacturing productivity
- Application expansion, new materials/new post-processing
“Innovation works in a very collaborative way” for HP, Pastor said, moving into the day’s introductions.
HP PP Material
“New applications enabled are enormous,” Pastor explained during the briefing of the new polypropylene (PP) material for 3D printing.
The material — formally HP 3D High Reusability PP enabled by BASF — offers the same properties as traditional PP manufacturing material. This is an important consideration for customers (and potential customers) familiar with PP who could see significant use for it in industrial 3D printing.
HP Multi Jet Fusion was introduced with nylon materials, and the expansion of this portfolio will continue to prove necessary for advancing its capabilities. PP is well-suited for use in 3D printing piping, fluid systems, and containers, for example. Furthermore, HP explains, “the new PP helps reduce waste by enabling up to 100% reusability of surplus powder.”
The BASF factor is important here as the chemicals giant continues to lean into the 3D printing industry with its tried-and-true materials expertise. The partnership to develop PP for the Jet Fusion 5200 3D Series is important to HP’s strategy — as we’ll discuss in a moment, the relationship with BASF has deepened.
HP is also jointly developing new applications for PP 3D printing with:
- Extol
- GKN Powder Metallurgy/Forecast 3D
- Henkel
- Oechsler
- Prototal
HP Professional Services
Next up, HP is introducing 3D Professional Services, including new and expanded offerings.
These include, per the presentation, service capabilities to:
- Facilitate Adoption: HP Parts Assessment, design for additive manufacturing training programs
- Enable Development: HP Design Optimization, application development support
- Drive Production: Sourcing strategy development, manufacturing optimization
Industry 4.0 Alliances
Collaboration is the way ahead for additive manufacturing — and for HP.
Along with the PP announcement, HP and BASF have also decided to ‘advance their strategic alliance.’ This deeper relationship will lead to new materials, joint development of applications, and go-to-market strategies, as well as a focus on sustainable production.
A new strategic alliance also introduces a relationship with Oechsler for joint applications development, with focus in automotive, commercial and home appliances, industrial, and medical uses. This alliance, the announcement notes, will see Oechsler leverage its Jet Fusion 5200 3D Series fleet and will “span the product lifecycle from application design to production of final parts.”
Further, HP is expanding its Digital Manufacturing Network, bringing Fast Radius onboard. The company joins Forecast 3D, GKN Additive, Go Proto, Jabil, Materialise, Parmatech, Prototal, and ZiggZagg.
Metal Jet Applications
Finally, HP shares an update on “advancing mass production” with new customers for its Metal Jet 3D printing technology.
The new customers are in slightly different focus, as HP announces Cobra Golf and the Marines as new users of Metal Jet.
Cobra will be putting the technology to use in work with HP and Parmatech laid out in a “multi-year product roadmap” to innovate and produce “first-of-its-kind clubs and equipment designed to elevate the game.”
The US Marine Corps (USMC) will be 3D printing replacement parts for its Amphibious Assault Vehicle (AAV). The new approach to supply chain — 3D printing on demand via virtual inventory — will keep the vehicle fleet operational, with approximately 200 AAV parts 3D printed in stainless steel.
“You can see why I’m so optimistic about this next step in our Digital Manufacturing journey. This has been a watershed moment for us, a watershed moment for the industry. The benefits of 3D printing are becoming clear and the world is watching us,” Pastor said, wrapping up the briefing. “We are doubling down on the adoption of 3D printing.”
Via HP