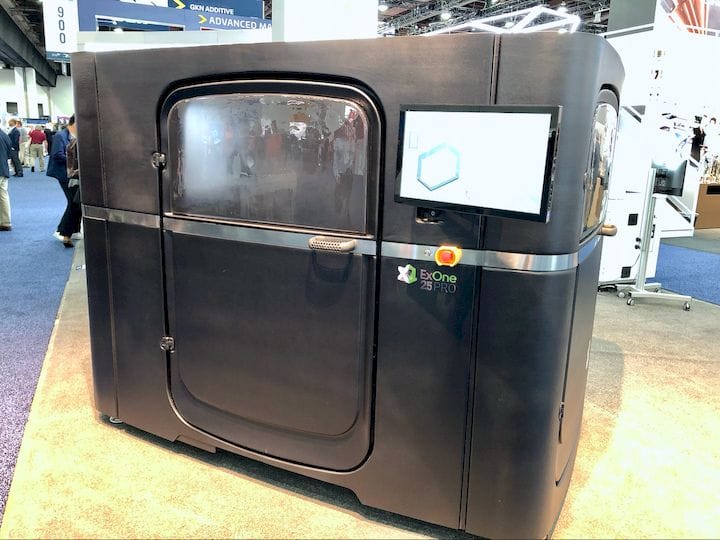
ExOne launched a new social media campaign a few weeks ago focusing on the green aspects of 3D printing.
The company, based in North Huntingdon, PA, manufactures large-scale 3D printers that employ the binder jetting process. Using this technique, the company has produced a number of machines that are able to 3D print in 20 metal, sand or even ceramic or composite materials.
They’ve been around for over twenty years, so they’re one of the veteran manufacturers of 3D printing. We’ve covered their X1 25PRO and X1 160PRO machines, as well as chatting with their new CEO, John Hartner, last year.
#MakeMetalGreen
Last month ExOne announced a social media campaign called “#MakeMetalGreen”. The idea here is that they believe, correctly, that 3D printing can be a much “greener” solution than many traditional approaches. They:
“… announced a new #MakeMetalGreen social media campaign to educate manufacturers about the sustainability benefits of metal binder jetting technology.”
They say binder jetting technology is green because it:
- Fabricates metal objects with little to no waste, offering a dramatic improvements over traditional manufacturing methods
- Enables all-new lightweight metal part designs, including those that consolidate many pieces of a product into a single unit, while preserving function and strength
- Produces parts that can make cars, trucks, airplanes and other equipment more fuel-efficient and also dramatically shorten supply chains, consuming far less energy”
These are all indeed true, but what struck me was that they need to say this at all. Doesn’t everyone understand these things yet?
Design For Additive Manufacturing
Sure, traditional mass manufacturing can produce individual parts faster than a typical 3D printer, but in many situations there must be many different “simple” parts assembled into a final “complex” system, whereas in some cases the final system could simply be designed as a single part and 3D printed in one step. This eliminates the sometimes-costly / time consuming / error-prone process of assembly.
This design approach has been leveraged extensively by many in the aerospace industry, led by GE, who first designed parts of an aircraft engine. Their project demonstrated to that industry the possibilities of 3D printing. Since then there has been a rush towards 3D printing by the aerospace industry, and many other industries have also taken notice and are increasing their use of 3D printing.
These practices have been well publicized by not only the 3D printer manufacturers, but also some of the companies benefiting from them. It’s been all over the trade press for years. Not a day goes by without us at Fabbaloo receiving another case study from a company showing how 3D printing provides much greater utility.
Yet, in spite of this continued and deep coverage, ExOne is still doing social media campaigns to highlight what most of us now believe to be obvious.
Except it is probably not obvious, still, to many manufacturers.
Promoting 3D Printing
Years ago I said that the spread of 3D printers in business is still thin and there’s plenty of room for many 3D printer manufacturers. Evidently that is still the case.
While we see survey results, such as from Sculpteo’s recent report, showing increased interest in 3D printing, the respondents from these surveys tend to be those who are aware of and use 3D printing already. There must be a vast number of manufacturers who could still be in the dark about the technology.
What do we do about this? 3D printer manufacturers will still publish case studies or trigger social media campaigns, but perhaps there is more we can do.
If you or your company is making innovative use of 3D printing, why not tell the world about your progress? Give everyone some tips on how it’s done. Show them it IS POSSIBLE in your industry to effectively use 3D printing. Let others see your confidence in the technology.
We’ll eventually have a better world because of it.
Via ExOne