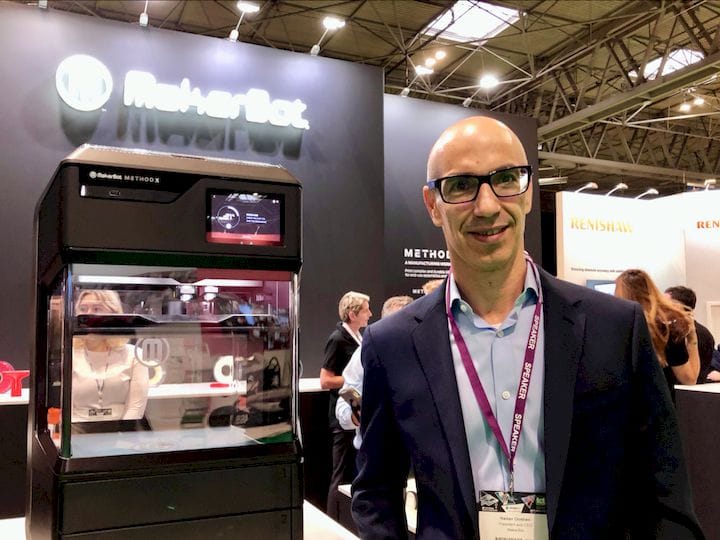
3D Print Annealing
Annealing is the process of heating up an object to improve its physical properties. Essentially, the material is allowed to recrystallize and this forms a stronger part. Wikipedia explains:
“In metallurgy and materials science, annealing is a heat treatment that alters the physical and sometimes chemical properties of a material to increase its ductility and reduce its hardness, making it more workable. It involves heating a material above its recrystallization temperature, maintaining a suitable temperature for an appropriate amount of time and then cooling.”
An excellent overview of how much a part’s strength can be improved was done by CNC Kitchen’s Stefan Hermann, who produced this excellent video on his annealing experiments:
Few 3D printer operators seem to do this process, as it is a bit cumbersome. Typically one uses a standard oven to heat the parts after 3D printing, but as you can imagine, this is less than precise. If you’re not careful you can actually damage the geometry of the parts with a poorly controlled annealing process.
MakerBot Annealing
Then I noticed a very telling line hidden in MakerBot’s latest press release announcing their new METHOD Carbon Fiber Editions. The line said:
“Users can print complex geometries with internal cavities using MakerBot’s PVA soluble support material and anneal the final part for extra strength with METHOD’s new heated chamber annealing feature.”
This is a powerful feature you might not notice unless you read the fine print.
MakerBot’s METHOD series uses a very different approach for build heating. Instead of using a heated print surface like practically every other 3D printer made today, they use a heated chamber. This means that not only the bottom of the print is heated, but the entire object during the entire print cycle. That heating prevents warping off the print surface, but also reduces thermal stresses throughout the print, leading to very high-quality prints with extremely accurate geometries.
But it now seems they are leveraging the ability to heat the build chamber for a second purpose: annealing.
I haven’t seen this yet, but it would appear that you could place parts in the 3D printer and set some type of “annealing mode” active. This would take the build chamber to a specific temperature (likely based on the material type) for a specific duration. The cooling rate can also be precisely controlled. This “recipe” could produce an optimum annealing without compromising the object’s fine geometry.
The MakerBot annealing function could be a lot more accurate than performing the process in an oven or other device not specifically designed to maintain precise temperatures. One potential drawback might be that the printer would be effectively “down” for further 3D prints while it’s busy annealing.
Nevertheless, this is a fascinating and powerful feature that appears to be available on the MakerBot METHOD series, and one that is not possible to implement on virtually any other FFF 3D printer.
Via MakerBot