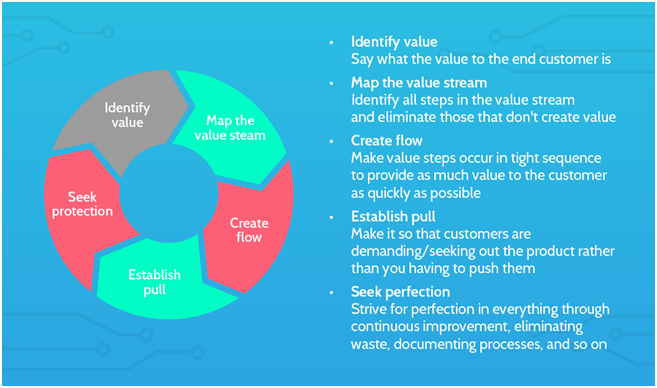
Charles R. Goulding and Preeti Sulibhavi examine the principles of Lean Manufacturing together with rising trends in automation and required social distancing.
At this time every plant manager is focused on how to re-engineer facilities to achieve appropriate social distancing. The fundamentals of Lean Manufacturing can be very helpful in this process. The five main principles of Lean Manufacturing are illustrated in the diagram above.
Although automation has always been a central component of Lean production, automated solutions, including collaborative robots, are much more advanced than when the term “Lean” was coined in 1988. To begin the distance-centric Lean process, plant managers should first outline existing plant processes using flowcharts. Flexible flowcharting software should be used as it is important to retain all of the new plant layout iterations until “Lean Perfection” is obtained. The Lean principle of establishing a pull system to effectively reduce inventory levels only to what the customer needs are will free up space at the plant.
Ultimately, automation will facilitate the “Lean Goal” of reducing excess staff for specific tasks. High-volume repetitive tasks can now be handled by collaborative robots, or cobots, which can further reduce the number of people on the plant floor. Cobots are particularly adept with standard high-volume product packaging. Furthermore, today’s 6-axis CNC machines and hybrid CNC/3D printers can reduce the number of machines needed on the plant floor. All production slowing bottlenecks need to be identified and can be eliminated with the help of these automated solutions.
With Lean Manufacturing, every tool and supply has an established location on the plant floor, so time isn’t wasted looking for required items. With social distancing measures in place, the required six-foot spacing is also marked on the plant floor. All non-production related tasks should be removed or segregated to reduce large group interaction. Non-production activities suitable for separate completion can include engineering and design concepts (CAD, 3D printing, etc.), new product labs, packing, and shipping.
Cobots [Source: Accenture]
Plant access should be secure and limited to essential plant workers. Once the first new commercial production layout is completed it should be flowcharted and compared to the first existing plant flowchart. One would expect the new plant layout to be entirely different.
New and improved Lean, Automation and Distancing (LAD) technology advances and plant re-engineering activities can be supported by R&D tax credits:
The Research & Development Tax Credit
Enacted in 1981, the now permanent Federal Research and Development (R&D) Tax Credit allows a credit that typically ranges from 4%-7% of eligible spending for new and improved products and processes. Qualified research must meet the following four criteria:
- Must be technological in nature
- Must be a component of the taxpayer’s business
- Must represent R&D in the experimental sense and generally includes all such costs related to the development or improvement of a product or process
- Must eliminate uncertainty through a process of experimentation that considers one or more alternatives
Eligible costs include US employee wages, cost of supplies consumed in the R&D process, cost of pre-production testing, US contract research expenses, and certain costs associated with developing a patent.
On December 18, 2015, President Obama signed the PATH Act, making the R&D Tax Credit permanent. Beginning in 2016, the R&D credit has been used to offset Alternative Minimum Tax for companies with revenue below $50MM, and startup businesses can obtain up to $250,000 per year in cash rebates applied directly toward payroll taxes.
Conclusion
Combining Lean Manufacturing, automation and social distancing practices is paramount to taking a whiteboard to plant operations. The manufacturing sector is going to need this kind of thought process to reopen safely and efficiently.