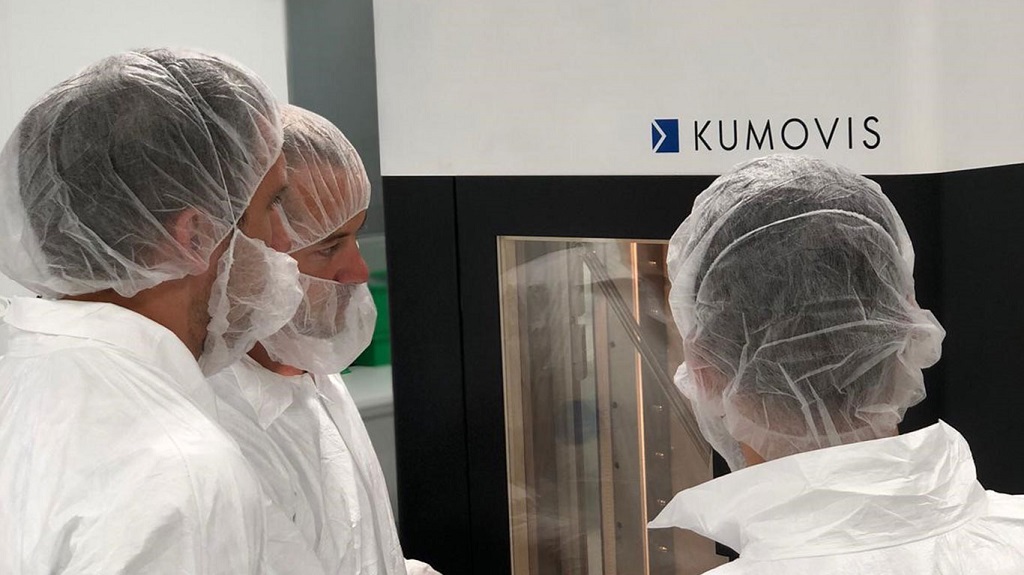
Decentralizing production is in focus for Kumovis’ mission in medical 3D printing.
I spoke recently with Stefan Leonhardt, one of two Managing Partners and four Founders of the Munich-based company, to catch up on all the activity inside the busy operation since we last chatted in October.
Kumovis has been focusing on point-of-care medical 3D printing with its “clean room” 3D printer, the R1. This focus has been of great benefit in the now-disrupted global supply chain, where shortages in personal protective equipment (PPE) and other pandemic-driven supply chain shortcomings have been shining a light on the benefits of localized production.
Kumovis Medical 3D Printing
When we caught up in October, Kumovis was delivering its first “serious machines” — and quite a lot has been happening since then.
“The team is enlarged; we have a new person in business development for the focus on point-of-care printing,” Leonhardt told me. “Point-of-care printing is rising in Germany, and we are pretty focused on this application at the moment.”
The team have been working with hospitals in Germany, Austria, and other nearby areas set up in-hospital 3D printing projects. Work with those in-house labs is showcasing the benefits of truly localized production, as each medical team can produce exactly what is needed — exactly where it is needed.
“With coronavirus, we are seeing more need for it now; hospitals want to be independent and have printers on their campus to produce products for themselves,” Leonhardt continued. “Corona shows that we need this independence.”
Kumovis started work with PEEK material as the main focus. They have been expanding from there, and are now also working with the “more tactile” PEKK and with PPSU “which is also implant-grade, and for use in instruments.”
“More and more we see we can print instruments at the point of care. We see people printing face shields and PPE, and we are also supporting some hospitals with face shields. We have a PPE project with a laryngoscope for intubation. These are all applications that can be printed directly in the hospital,” Leonhardt said.
Adding additional capabilities in materials is expanding the functionality of point-of-care 3D printing.
Next For Kumovis
The team at Kumovis has also been looking to launch its next steps — though now those launches will be reconfigured.
In the works for announcement at an upcoming fair — “but I guess there are no more fairs this year” — the next news will be presented virtually in the near future.
“A big topic for us is the home medical sector, and the big thing we focused on was process monitoring. We have been focusing on how to get proper documentation of the whole thing, so you can certify the product, the implant, whatever is made,” Leonhardt said of Kumovis’ focus on medical device regulation (MDR).
“This will be software that can document everything during the whole printing process: set parameters, temperature, build chamber, movement. There’s a pretty cool graphic afterward to see if we are in the limits set before. For a cranial implant, for example, you can do process validation. There are some limits in the parameters where you have to prove you are in this range. This will help the industry, to qualify systems in hospitals to prove the product is produced in a certain way. It’s a huge step for us.”
Kumovis has also been working on structures and post-processing for osseointegration.
Polymers like PEEK, PEKK, and PPSU don’t have a hydrophilic surface like titanium does, as Leonhardt pointed out. These allow for “really cool structures, pore structures for osseointegration for bone growth.”
This is a notable area of focus now for the team, as they are working on research projects in post-processing. They are examining plasma coating and spattering, working with a partner with a chemical coating. In the lab, they have 3D printed cubes with infrastructures where “we can see that liquid is going through, and realize how it can transport in especially the spinal area.”
Usability is another major area for Kumovis, as they seek to have their R1 3D printer as user-friendly as possible.
“When we give a printer to a hospital, we don’t want to waste the brain power of surgeons to learn printers, or stand by the printer and learn to work everything. It must work easy — it must be a wizard,” Leonhardt said with a smile. “This is something we are doing at the moment, with clinics together, to show that this machine is easy. It will never be a one-click machine, but it will be a guided process.”
In-hospital labs offer incredible accessibility for point-of-care production — but as the Kumovis team are well aware, 3D printing is certainly not that “one-click” process. Significant work in design, printing, and post-processing must happen, and as anyone who has ever worked with 3D printing well knows, it’s not always the most intuitive process. By dedicating resources to ensuring ease of use, Kumovis is seeking to guide surgeons and other medical professionals as much as possible for their own independence of use for the medical devices they need.
As we wrapped up our chat, Leonhardt noted succinctly that “it’s a big medical industry” and Kumovis still has a lot to figure out with their business model.
“As we’re setting up more printers in hospitals, of course medical device manufacturers will sell less implants, so we have to figure out how this will work out. And of course on the regulatory side: who is responsible? There’s a lot in certification. There are many approaches in the industry, and some with printer manufacturers. I guess in two years we will know which have worked out.”
Kumovis continues to grow in terms of both technology and business and after speaking with Leonhardt, it’s clear we’ll be hearing much more from this team — quite soon, by the sounds of it.
Via Kumovis