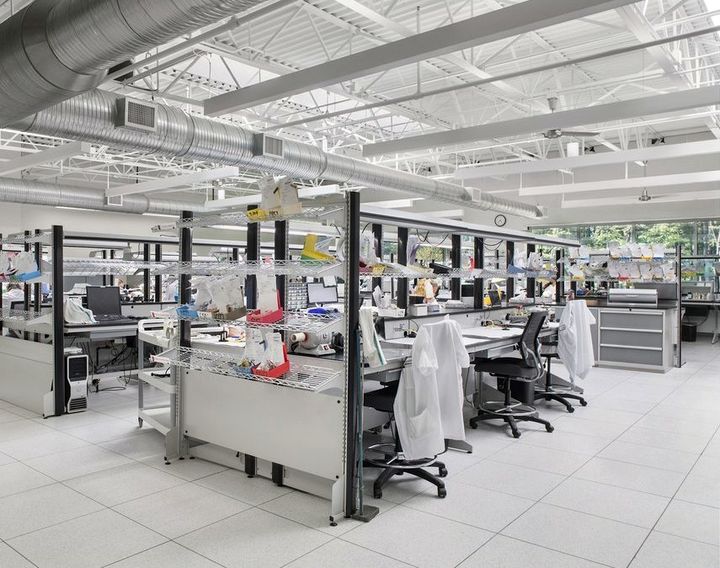
One (or more) of Formlabs’ clients has been saved from catastrophe during the COVID-19 crisis in a way that demonstrates the incredible power of 3D printing.
Formlabs, as long-time readers will recall, is one of the leading manufacturers of desktop SLA 3D printers, using resin to print high-resolution objects on demand.
One of the largest client groups for Formlabs is the dental industry, who use their equipment and materials to produce casting, dentures, surgical guides, aligner models and many more functional appliances. 3D printing is particularly useful for these products as they need to be personalized, and such one-off production is easily handled by a 3D printer.
Dental is one of the prime industries being addressed by 3D printing, simply because it is incredibly efficient. Several companies, including Formlabs, have built a strong focus on the dental industry, providing different types of support services.
COVID-19 Effect On Dental Industry
The use of 3D printing in dental applications has been growing strongly, but in spring 2020, something happened. That was COVID-19, and its effect on the dental industry has been near catastrophic.
The problem is that dental procedures, even routine procedures, are highly likely to generate aerosols containing the virus from affected patients. As a result, dental offices have been shut down almost everywhere.
In our area at least, emergency dental services have been available. But I asked a dentist friend to explain how this works and they told me they really aren’t doing services — they’re merely prescribing painkillers and few actual dental services are being performed.
That pattern is likely being echoed in dental offices across the globe, and this means there is a dramatic, if not total, stoppage of dental appliance production. That means there’s little dental 3D printing taking place, and consequently fewer dental 3D printers being purchased. Not good news for dental labs nor Formlabs.
Formlabs COVID-19 Reaction
Formlabs reacted to the crisis in a very innovative and positive way. They sought to bring their skills and resources to address the crisis and they shifted focus.
They transformed their array of Formlabs 3D printers towards COVID-19 production. They selected a design for a 3D printable test swab, which is required in massive volumes. Formlabs was able to adapt their internal printer farm to produce almost 1M test swabs each week in record time.
Their project, among several others in the 3D print community, proved to the world that 3D printing technology is indeed able to handle very short-term production to notable unit levels. This is something that is now known by the public and should change the fate of 3D printing technology forever.
Dental Industry COVID-19 Reaction
To those operating dental laboratories the crisis is devastating, as they’ve had to endure almost total shutdowns. However, something rather interesting occurred to at least one Formlabs client.
ROE Dental Lab took a cue from Formlabs’ lead and performed a similar transformation. Formlabs explains:
“ROE Dental has now retooled to manufacture PPE and medical supplies, including 15,000 nasopharyngeal (NP) swabs a day. These swabs are vital for collecting samples for COVID-19 testing. The lab has already managed to bring back 175 staff and have been personally thanked by Ohio Governor Mike DeWine for supporting the fight against the pandemic.”
While the result for ROE Dental has clearly been positive, there’s something incredibly powerful going on here.
A company that happened to operate a farm of 3D printers was literally able to completely repurpose their production in only a couple of weeks! This would be entirely impossible for traditional manufacturing operations, which in some cases have still not caught up to COVID-19 required levels.
The implication is that anyone using 3D printers at scale has a powerful ability to shift gears and adapt at a rate never seen before in industry.
3D printers can not only provide fast turnaround, but they can also provide a massive degree of flexibility and risk mitigation for a company choosing to use them.
Via Formlabs