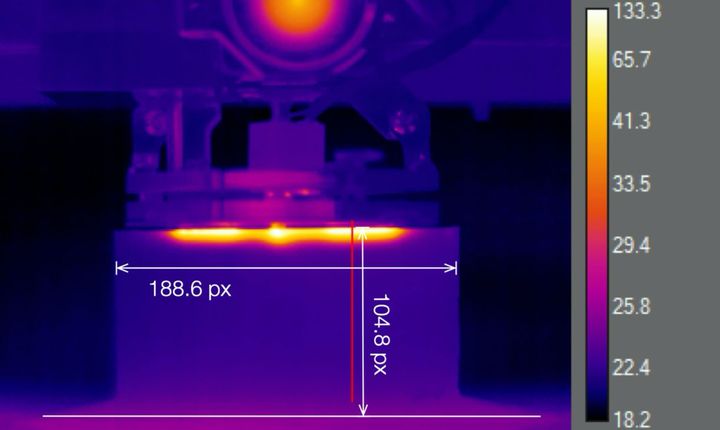
Researchers, including some from 3D printer manufacturer Essentium, have developed a unique method of achieving isotropic 3D printing by using an electric plasma.
Isotropic 3D Printing
Isotropic 3D printing is the gold standard for production parts, as it provides the best possible strength for a given material.
Typical injection molded parts have isotropic properties; that is, the part strength is near-identical in all directions. Injection molding achieves this because the molten thermoplastic mixes well in all directions and solidifies as a contiguous mass.
That’s quite different from 3D printing, in which this effect occurs only with the extrusion strand emerging from the nozzle. Within that strand we find isotropy, but this extrusion must be joined to adjacent layers.
That’s where the problem lies: the weakest part of a material extrusion 3D print is the bonding between the layers. If you’ve ever put a 3D printed part under mechanical stress, that’s where it’s likely going to break: between layers.
In other words, material extrusion 3D prints are almost always anisotropic, the opposite of isotropic.
3D Printing Dielectric Barrier Discharge Applicator
The new research describes a method by which a Dielectric Barrier Discharge Applicator (DBD) is used to overcome the poor interlayer bonding. The DBD is essentially an electrode mounted concentrically around the extrusion nozzle.
The next thing to understand is the material being used for the experiment: it’s a composite material containing carbon nanotubes. It turns out that carbon nanotubes react in the presence of an electric field of certain frequencies by strongly heating up.
The concept is that as the composite material is extruded, it encounters the electric field generated by the DBD. This causes the carbon nanotubes within the material to rapidly heat up due to the resistive heating effect, and they correspondingly heat up the adjacent thermoplastic component of the material.
The strongly heated extrusion then bonds with much greater strength to the previous layer, far more than is typically achieved with conventional material extrusion 3D printing.
The research paper describes the action as “welding”, which is effectively what’s happening.
Evidently the researchers spent considerable time experimenting with different settings for the DBD and material to ensure successful bonding. Using advanced techniques, they found a combination of parameters to ensure sufficient “time at temperature” for strong layer bonding.
Isotropic 3D Print Testing
But is the resulting 3D print strong?
Test coupons (dog bones) were 3D printed with and without the DBD effect and tested. They found the DBD-enhanced prints had 31% greater tensile strength and were in fact “statistically equivalent to injection-molded parts”. This is quite a development.
DBD 3D Printing
This approach is quite reminiscent of Essentium’s prior work with electrically-enhanced 3D printing. In 2017 they produced the “Fuse” filament, which used electrical resistance from a current between the nozzle and the print bed to generate extra heat. However, this required specialized 3D printing hardware.
The researchers mention they’ve previously experimented with microwave-based heating in a similar approach, but found microwave hardware to be bulky and not particularly practical for 3D printing.
However, it seems that the DBD approach might be a winner, as it seems to be a more practical approach.
Several of the authors of the paper are from Essentium, including CEO Blake Teipel, who we recently interviewed. It’s quite possible that Essentium may incorporate the DBD approach into their future equipment, making their 3D printers capable of producing end-use fully isotropic parts.
Via ACS