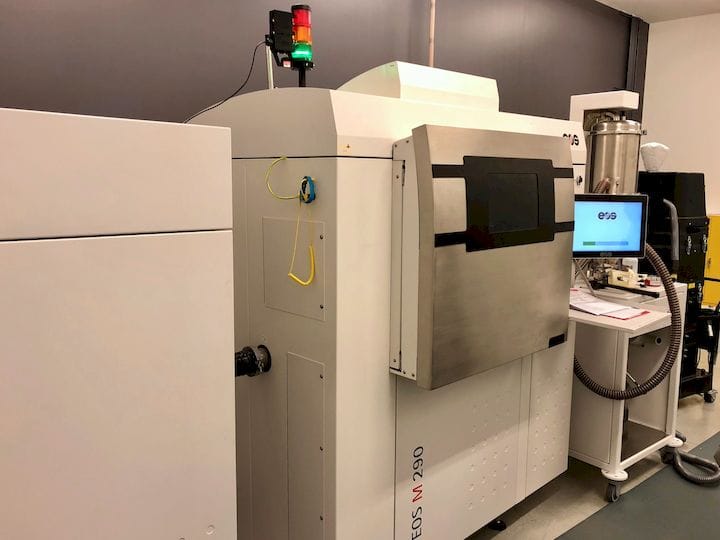
I’m reading a technical notice recently issued by EOS to their clients regarding safety, and it’s quite interesting.
The notice is destined for users of their popular metal 3D printer line, including the EOS M 290, EOS M 290, AM S 290, EOS M 400 and EOS M 400-4 systems. Each of these machines uses the familiar powder bed fusion approach, where powerful lasers selectively sinter a flat bed of fine metal powder, layer by layer.
EOS’ focus here is the handling of filters after 3D printing. This is a maintenance task that must be completed to keep the machine in running order. EOS emphasizes:
“While there is not a risk to the machine during build conditions, it is imperative that safety measures are carefully followed while handling the filters.”
And:
“For safety reasons, please always observe the following instructions in combination with the operating manual of the EOS M 290, EOS M 290 Custom X Frame, AM S 290, EOS M 400 and EOS M 400-4 systems.”
What is the big concern? Why is EOS issuing a special notice?
3D Print Metal Condensate
It turns out there is a notable risk that develops after the machine is running. The filters collect “condensate” during printing, and this substance can be dangerous to handle afterwards.
This condensate is in fact the same metal material that’s being 3D printed, but it is deposited in a much more risky form. EOS explains:
“During the laser solidification process, the metal alloy evaporates and re-condenses immediately after falling below the saturation temperature. This process creates very small particles with a very large surface area. Since the condensation occurs in an inert gas atmosphere, the surface of the particles is not oxidized. Consequently, metal condensate has a very low minimum ignition energy (< 1 mJ).”
This makes sense, as the fine metal powder material supplied to the machine will have a fairly uniform particle size. But if the metal is atomized during 3D printing, it could form into far smaller particles. This means there are more particles per weight of material, and thus far more surface area to interact with the oxygen in the atmosphere.
Normally pure metal powder, which is not oxidized, is stored in an oxygen-free environment before, during and after 3D printing. However, the condensate in the filters can be exposed to the atmosphere.
This phenomenon would occur in many types of PBF metal 3D printers, not just in EOS equipment.
I wrote about the metal 3D printing condensate issue last year when I first learned about it. In that story the fear was that some 3D printer operators were not taking the danger as seriously as they should, and thus were handling the condensate poorly. This generates a risk of ignition, and that’s never good.
3D Print Condensate Risk
The problem is that it is sometimes expensive to dispose of the flammable condensate, and some short-cutting operations just leave it in a pile. That is definitely not a good thing, as a pile of condensate is far worse than just a filter or two.
EOS explains what could happen:
“If a chemical reaction leading to a combustion event occurs in the metal condensate, it can be expected to develop slowly. First, the condensate on the filter surface is oxidized, causing a thermal reaction. Then, the fabric of the filter may ignite.”
EOS recommends ensuring all operators are sufficiently trained in the required procedures. Those procedures include: frequent filter cleaning (with 4X repeats); cooling filters before cleaning; PPE; two-person filter cleaning process; and of course, having extinguishing agents, including a sand tub, handy in case of trouble.
Running a metal 3D printing workshop with today’s equipment can be an extremely challenging set of tasks, and handling the filters is but only one of them. If you’re operating a metal 3D printer you might want to take some time to review your condensate procedures.
And kudos to EOS for raising this issue with their clients.
Via EOS