![The FUNMAT PRO 410 high temperature 3D printer [Source: INTAMSYS]](https://fabbaloo.com/wp-content/uploads/2020/05/image-asset_img_5eb065c0b6a9a.jpg)
The FUNMAT PRO 410 high temperature 3D printer [Source: INTAMSYS]
With the recent increase of the Internet of Things and smart manufacturing products, there is a growing demand for applications such as complex 3D printed structural components with high bending and stretching mechanical properties in many fields.
3D printing is a manufacturing process that can effectively fabricate highly customized objects with diverse and complex geometries. Fused deposition modeling (FDM), also known as fused filament fabrication (FFF), is a common 3D printing method based on the deposition of successive layers of softened thermoplastic materials. FDM/FFF are widely used in numerous industries, including healthcare, automotive, aerospace, oil & gas, and others.
A recent study by China SMT (CAS Key Laboratory of Space Manufacturing Technology, SMT) entitled “Fabrication of Smart Components by 3D Printing and Laser-Scribing Technologies”, has been published in the America’s ACS Applied Materials & Interfaces journals. SMT proposes an innovative idea by combining 3D printing and laser-scribing technologies to fabricate smart components.
In this study, smart 3D printed structural components with self-monitoring abilities show potential applications in certain extreme environments, such as deep-water and space. SMT researchers put forward a unique strategy for the fabrication of smart components, which includes the 3D printing of PEEK architectures and the in-situ generation laser scribing laser-induced graphene (LIG) sensors on surfaces.
High-performance PEEK-LIG SCs can self-monitor the working process and the deformations (bidirectional bending and stretching) of the 3D printed components in various environments. In addition, the LIG layer shows good adhesion with the PEEK substrates, and it cannot decrease the strong mechanical properties of the 3D printed PEEK components.
PEEK Material
![A spool of high-temperature PEEK 3D print material [Source: INTAMSYS]](https://fabbaloo.com/wp-content/uploads/2020/05/image-asset_img_5eb065c0f1df3.jpg)
A spool of high-temperature PEEK 3D print material [Source: INTAMSYS]
STM developed a low-cost and straightforward fabrication of smart components combining FDM/FFF with laser-scribing technology. A thin LIG layer (∼50 μm) can serve as the active material for the sensors, which can be applied to the 3D printed PEEK components.
![The INTAMSYS 3D print- laser-scribing process [Source: INTAMSYS]](https://fabbaloo.com/wp-content/uploads/2020/05/image-asset_img_5eb065c14dd4f.jpg)
The INTAMSYS 3D print- laser-scribing process [Source: INTAMSYS]
The INTAMSYS FUNMAT HT 3D printer was used to support the China SMT team to develop this low-cost fabrication of intelligent components.
![The INTAMSYS FUNMAT HT [Source: INTAMSYS]](https://fabbaloo.com/wp-content/uploads/2020/05/image-asset_img_5eb065c191e64.jpg)
The INTAMSYS FUNMAT HT [Source: INTAMSYS]
Thanks to the FUNMAT HT’s advanced thermal design (90C chamber temperature and 450C nozzle temperature), more than 20 unique functional materials can be printed. These include high-performance functional materials like PEEK, PEKK, ULTEM (PEI), PPSU and engineering materials including as PC, PA, PA-CF, ABS, etc.
In addition to the FUNMAT HT, INTAMSYS also offers the FUNMAT PRO 410 model featuring dual extruders and a large build volume of 305 x 305 x 406 mm. This permits high-speed and high-precision 3D printing, ideal for research purposes requiring the use of these high-performance polymers.
Why use PEEK? PEEK is widely used in 3D printing due to its excellent processing properties, thermal stability and its strong mechanical properties.
The results of the SMT study showed excellent performance of the PEEK-LIG smart gear when monitoring the rotation and the abrasion, indicating a wide scope of potential applications for this strategy, especially in the fabrication of smart components and the building of self-monitoring structures. These could be of particular use in dangerous environments.
![The fabrication of smart component and the characterization of LIG [Source: INTAMSYS]](https://fabbaloo.com/wp-content/uploads/2020/05/image-asset_img_5eb065c1be37a.jpg)
The fabrication of smart component and the characterization of LIG [Source: INTAMSYS]
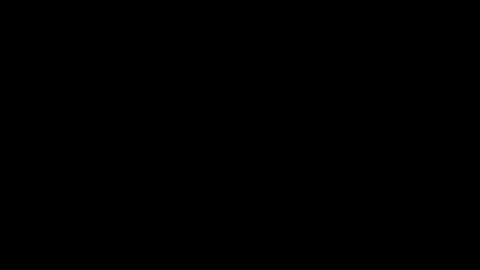
PEEK-LIG sensor detecting bidirectional bending in water
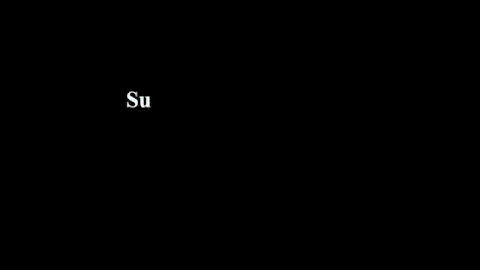
PEEK-LIG smart gear can self-monitor the rotation and abrasion
Click HERE for the detailed study by SMT. Data sourcing: ACS Applied Materials & Interfaces ( IF 8.456 ) Pub Date : 2020-01-10 , DOI: 10.1021/acsami.9b17467
About INTAMSYS
INTAMSYS 3D Printing All-in-One Solutions aspires to make our future fully customizable with the infinite possibilities offered by Additive Manufacturing. Meeting the most demanding industrial standards, INTAMSYS 3D Printers are optimized for applications in industries as diverse as Automotive, Aerospace, Oil & Gas, Healthcare, Jigs & Fixtures or even Education. To know more products information, please visit INTAMSYS.