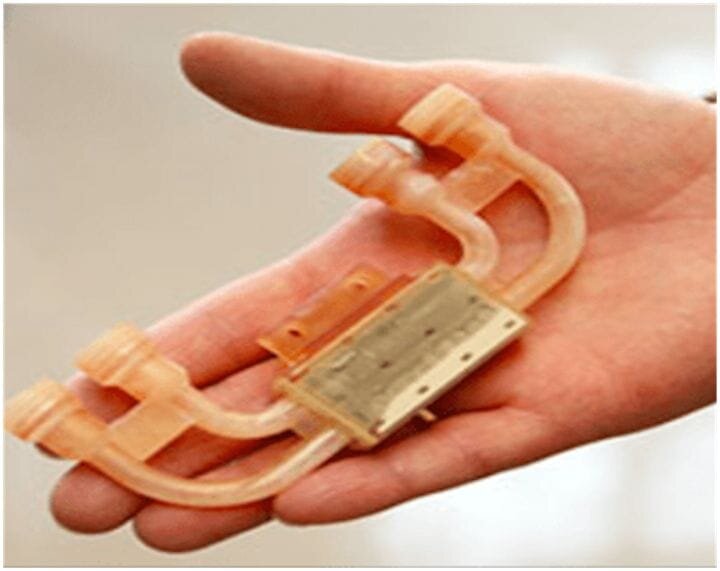
Charles Goulding and Peter Favata of R&D Tax Savers take a look at how the commercial refrigeration industry is beginning to make production use of 3D printing technology.
Commercial Refrigeration a Growing Industry
Commercial refrigeration is a growing market due to changing food consumption trends, the emergence of supermarkets and different fast-food chains, as well as increasing international trade. Growth of online grocery sales is also a major component, and with consumer demand for fresh produce, cold storage warehouses are a necessity.
According to a recent article in the Wall Street Journal, “similar to the way real-estate investors flocked to distribution centers to profit from the rise of online shopping – investors are starting to pile into cold-storage warehouses”. As a result, more energy-efficient equipment is being designed, manufactured, and installed.
A further growth area for commercial refrigeration has been the growing food delivery market. The global commercial refrigeration market had sales of $33 billion in 2018 and projected sales of $53 billion in 2026. Some major commercial refrigeration companies with interest and exposure to 3D printing include Carrier Commercial Refrigeration and Lennox International.
3D Printing to Design an Energy-Efficient Refrigeration system
Researchers at the Ames Laboratory, a United States Department of Energy national laboratory located in Ames, Iowa and affiliated with Iowa State University, have designed and built a solid-state system that can cool to refrigeration-level temperatures. This system requires no mechanical refrigeration and uses circulating water as the heat transfer medium.
The system is kept cool through magnetic refrigeration. This is called magneto thermodynamic phenomena; it is when certain materials will change temperature when exposed to a change in the strength of the magnetic field. The head of the project’s design, Julie Slaughter of Ames Laboratory, decided on using 3D printing to create the heart of the system, the manifold that is shown at top.
Lennox International
Lennox International is a publicly-traded HVAC air conditioning and Refrigeration Company with sales approaching US$4B and 11,000 employees. Lennox International has some interesting ideas for 3D printers when it comes to inventory. They want to have a printer on every truck in the field, giving them the ability to print a replacement part in only a few hours instead of waiting for the usual five to seven business days for it.
They would also implement the use of 3D scanners in the field. This would provide the technician with the ability to scan a part and immediately know more about the specific part. This could allow them to quickly diagnose a problem and use the scan to identify the requited part.
3D Printing Models for Refrigeration Parts
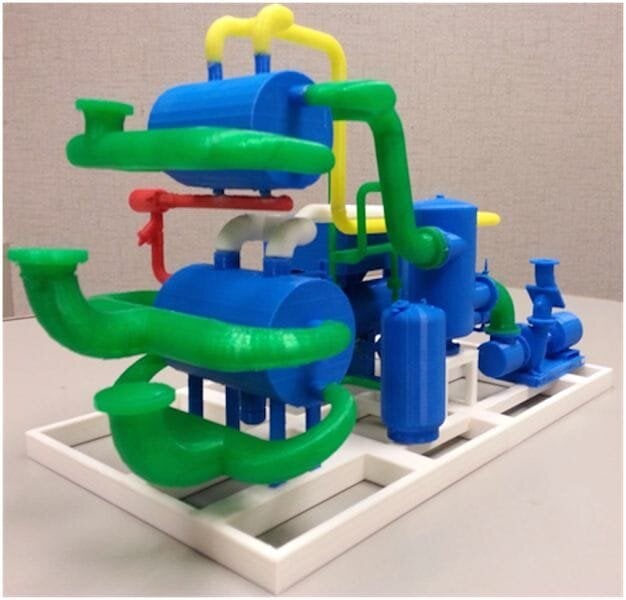
3D printing is starting to complement the refrigeration design process. Stellar Refrigeration Services in Jacksonville Florida has been experimenting with 3D printing by utilizing 3D printing during the initial design phase of refrigeration projects.
Stellar will build a CAD model on a computer from which they will 3D print the model so they can see what it will look like once the part is manufactured. Another reason for doing this is to show their clients the parts they will be buying before they make the purchase. The printed model is color-coded to show the different refrigerant surface types; a sample of the model is shown above.
Carrier Corporation
Carrier Corporation manufactures and distributes air conditioning, heating, and ventilation equipment and $10.5 million in sales with 45,000 employees as of 2018. Modern-day air-conditioning and refrigeration were invented by Willis Carrier. Carrier is in the process of being spun off by United Technologies its corporate parent. United Technologies has had a major commitment to its research center to 3D printing research.
Presumably, the 3D product developed relates to refrigeration can be further developed by an independent Carrier Corporation.
The Research & Development Tax Credit
Enacted in 1981, the now permanent Federal Research and Development (R&D) Tax Credit allows a credit that typically ranges from 4%-7% of eligible spending for new and improved products and processes. Qualified research must meet the following four criteria:
-
Must be technological in nature
-
Must be a component of the taxpayer’s business
-
Must represent R&D in the experimental sense and generally includes all such costs related to the development or improvement of a product or process
-
Must eliminate uncertainty through a process of experimentation that considers one or more alternatives
Eligible costs include US employee wages, cost of supplies consumed in the R&D process, cost of pre-production testing, US contract research expenses, and certain costs associated with developing a patent.
On December 18, 2015, President Obama signed the PATH Act, making the R&D Tax Credit permanent. Since 2016, the R&D credit can be used to offset Alternative Minimum Tax (AMT) for companies with revenue below $50MM and. Startup businesses can obtain up to $250,000 per year cash rebates that are applied to payroll taxes directly.
Potential to Expand on 3D Printing
With refrigeration companies beginning to utilize 3D printing there are many other components of refrigeration systems that have the potential to be 3D printed. For example, the shelf inserts and door handles of refrigerators are often made of 3D printable plastics, and we could soon see custom-designed shelf components in the future.