3D printed automotive dashboard vent, with digital production patterning, made in PRO-BLK 10 as seen at TCT Show [Image: Fabbaloo]
The latest materials for 3D Systems’ Figure 4 system highlight one very important thing for 3D printing: it’s ready for production.
Of course that’s not a blanket statement and most 3D printing usage will remain in more developmental applications for quite some time yet. But when it comes to the Figure 4, the intent is production — and materials development is a major part of that.
5 New Figure 4 Materials
This week, 3D Systems introduced five new materials for Figure 4. The team told me that it was more exciting than the press release made it sound, so I spoke with Ed Hortelano, 3D Systems’ VP of Materials R&D, to dig into why.
“We’re really excited about this round of materials we’re releasing for the Figure 4,” Hortelano told me. “We have a set of materials that have really good long-term stability, on top of really good out-of-the-printer properties. What’s exciting for our customers is the ability to create parts for their applications as a credible replacement to injection molded parts. This is finally in some ways fulfilling the dream of having 3D printed parts that are fully production-grade. The end users of the parts should pick these things up and not notice they came out of a printer rather than an injection mold.”
So what exactly are these new materials?
The star of the show, as it were, is Figure 4 PRO-BLK 10. This production-grade photopolymer is 3D Systems’ first, they say, to exhibit thermoplastic behaviors — which are what make it that injection molding replacement Hortelano references.
Post-processing for PRO-BLK 10 is a particular highlight. 3D Systems explains:
“The breakthrough material works with a simple isopropyl alcohol (IPA) wash and does not require a secondary thermal post-cure process, which significantly improves throughput yield and significantly reduces the extensive solvent cleaning cycles needed with other technologies.”
Automotive window clip 3D printed in FLEX-BLK 20 as seen at TCT Show [Image: Fabbaloo]
Along with the PRO-BLK 10 are, as described by 3D Systems:
-
Figure 4 EGGSHELL-AMB 10: A process-optimized material for the production of sacrificial tooling for casting true silicone components.
-
Figure 4 HI TEMP 300-AMB: Industry-leading, ultra-high temperature (300 Celsius) rigid plastic suitable for production applications such as high temperature component testing and stators and motor enclosures.
-
Figure 4 FLEX-BLK 20: Durable, flexible, high impact, fatigue resistant material with long term environmental stability for functional assemblies and prototypes such as automotive styling parts, consumer goods and electronic components, snap-fit assemblies, containers and enclosures.
-
Figure 4 RUBBER-BLK 10: High-tear strength, malleable, material designed for prototyping hard, rubber-like parts such as grips, handles and couplings.
Materials Development
The materials have been in development for some months as 3D Systems worked closely with a select group of customers in key (undisclosed) verticals to ensure they would be what actual users actually needed.
Hortelano called the new materials introductions “more blades on their Swiss army knife to make their printer more capable to do whatever they require of it.” He couldn’t discuss any customers in particular, or even the industries they work in, but the press release and a few sample parts reveal a bit about some of the targeted users.
D&K Engineering, a California-based contract manufacturer, has been working with PRO-BLK 10 in its prototyping lab, creating threaded parts — and looking toward making production parts for customers.
A spotlight part featured in the press release in this material is an automotive dashboard vent, which our own Kerry had the opportunity to see at this week’s TCT Show (photographed at top) and he was able to get hands-on with parts in each of the new materials. The properties seem as described, with the rubbery material showing good flex and the Eggshell appropriate for silicone molding usage.
A closer look at these parts:
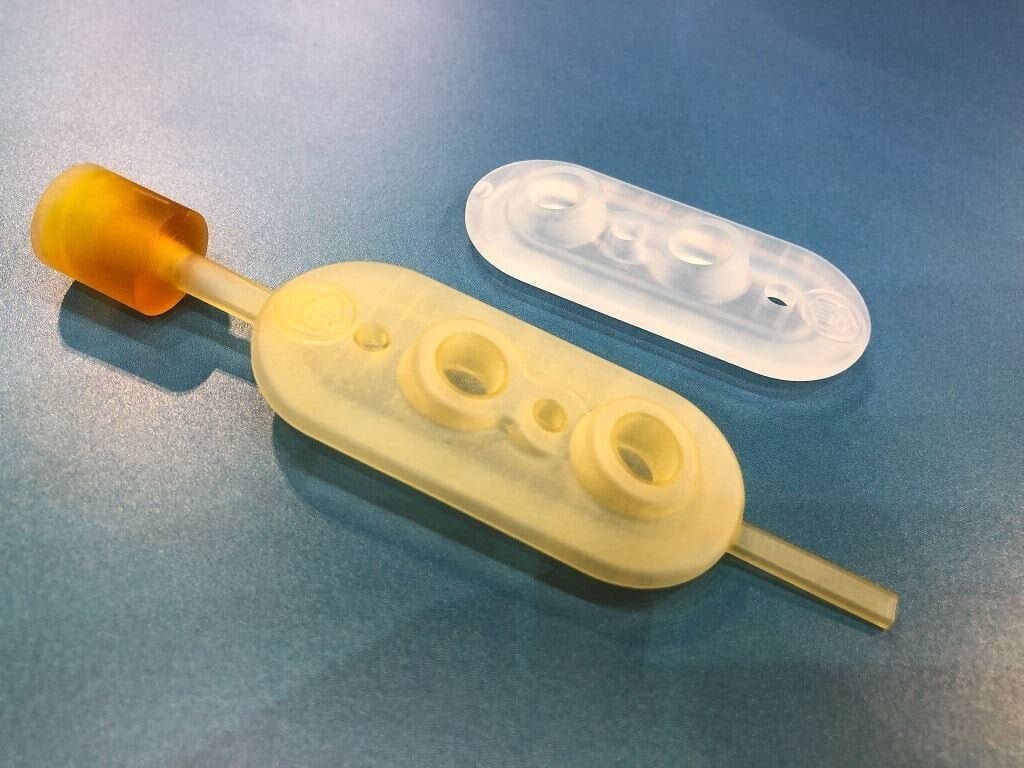
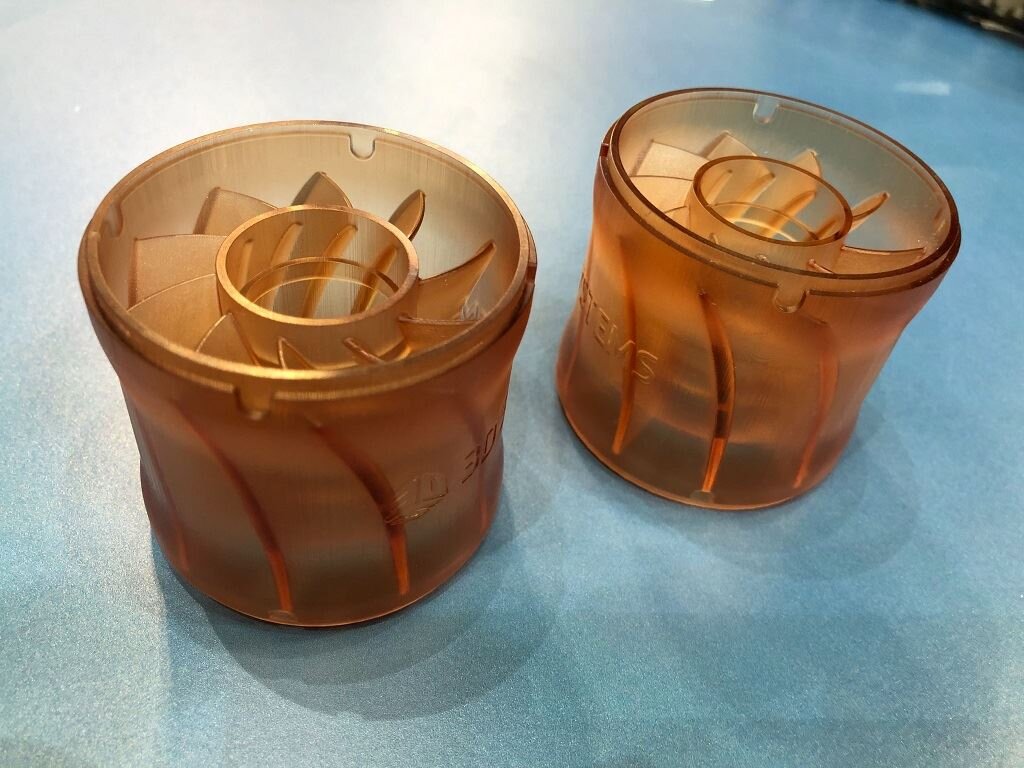
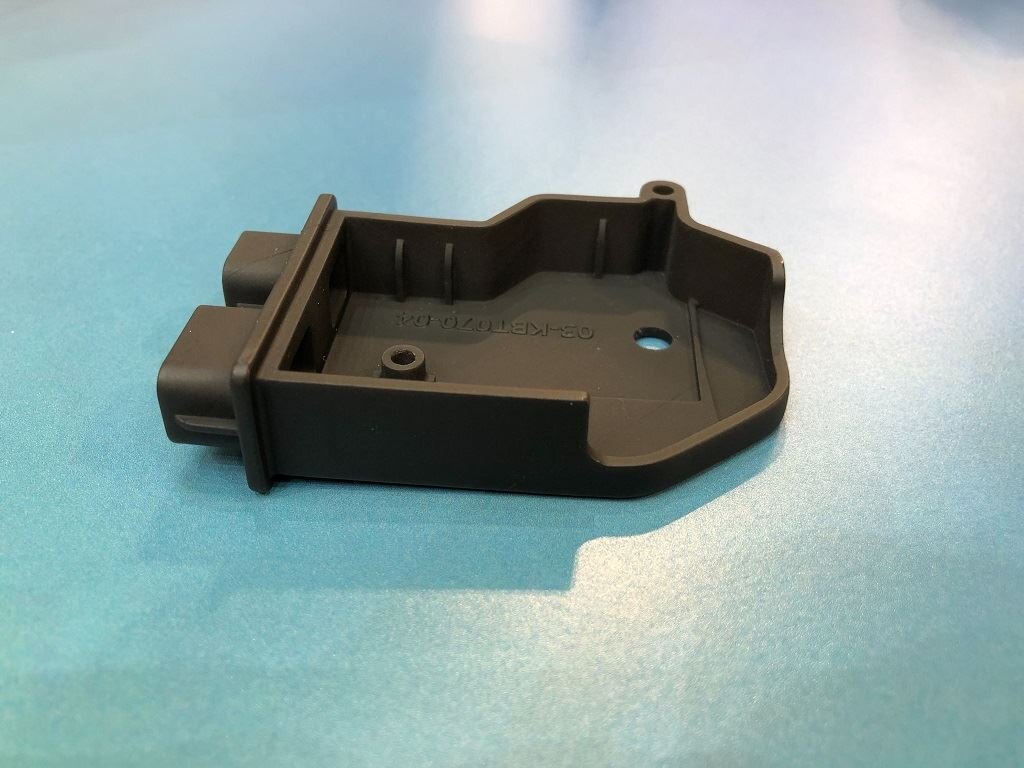
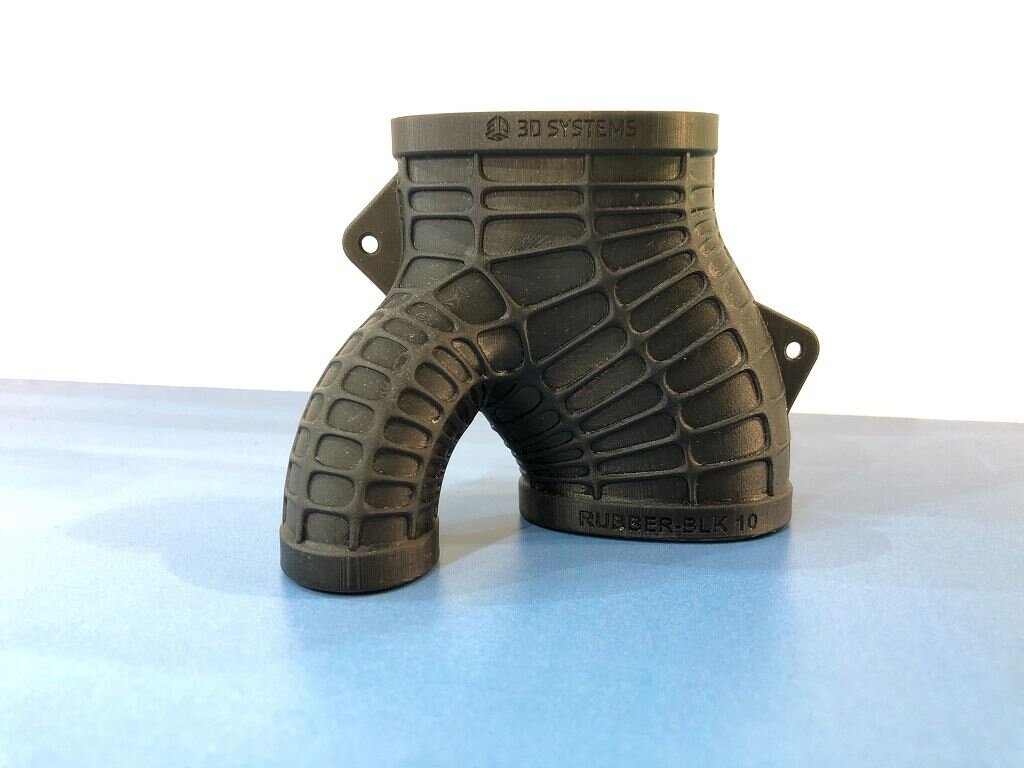
[L-R from top: EGGSHELL-AMB 10, HI TEMP 300-AMB, FLEX-BLK 20, RUBBER-BLK 10 as seen at TCT Show / Images: Fabbaloo]
Customer conversations started early this year, with collaborations really picking up the pace around May, as Hortelano revealed. He described the collaborative partners as “selected customers who are leading in a particular vertical” and noted that the conversations led to “opportunity for very good iteration to give them something to evaluate and test.”
“It gave us a chance to have this good collaboration, good iteration, good feedback to know that all these products will really function in their intended application areas. It’s more than having good smart capable people in [3D Systems’ HQ in] Rock Hill formulating and testing prints. I’m really happy with these materials and the results of looking outward and getting good input from users in this area,” Hortelano told me.
Big Picture Look
This RUBBER-BLK 10 part shows good flexibility at TCT Show [Image: Fabbaloo]
Overall, these materials are significant for not only 3D Systems and their customers, but for the industry — any strong proof point of production-quality 3D printing is a strong testament to the viability of this technology suite.
And testament sure seems to be what these materials are.
“In the big picture, these are high-performance materials that are now available out of 3D printers, increasing the application space for 3D printing at the end of the day. For me those are really the things that these materials are enabling for our customers,” Hortelano said.
Customer enablement should be at the heart of every development and every step along the path toward production quality.
Via 3D Systems