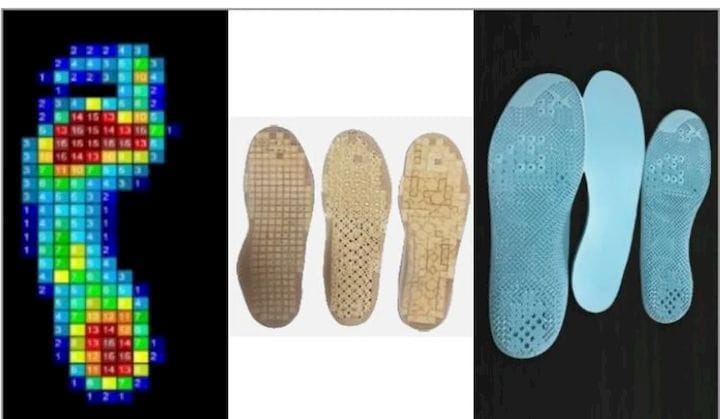
Injection molding, as a process for mass-producing plastic parts, has been refined over multiple decades and is a massively efficient way to produce high volumes of identical plastic parts. In the age of mass-produced goods, this was ideal.
Today, with the advent of digital manufacturing, the demand is rising for customized products tailored to the individual. It’s not enough to offer a customized product. Manufacturing processes must now also be flexible enough to accommodate custom work at mass production speed.
In response to this demand for “mass customization,” production of high-value and low-volume parts has started to shift to industrialized 3D printing, known as additive manufacturing (AM). However, most high-volume parts continue to be made with traditional injection molding (IM) techniques because the cost of engineering and moldmaking is amortized across many parts. So, these two options accommodate both low-volume custom orders and high-volume, mass-production orders. But what about manufacturers that need to produce custom parts at scale—is this a new growth area?
According to EOS, the solution lies in the industrial additive manufacturing ecosystem. This includes not just the additive machines, but also the design, materials, process and software which can be optimized to support flexible production of custom parts at a global scale. Solution engineering is fundamental for deploying AM effectively in serial production. This means rethinking and reengineering the material, process and system of the product design in order to take full advantage of the capabilities of AM.
In this way, AM and traditional molding complement each other, serving each type and scale of need for plastic production.
Taking Advantage of AM Capabilities
With industrial polymer 3D printers, powder-based technology, such as selective laser sintering (SLS), is most suitable. Parts can be arrayed in the build chamber in three dimensions, supported by the unfused powder, allowing the relatively long cycle time (10+ hours in many cases) to be offset by the high productivity per print cycle.
“Today’s SLS processes are competitive with precision injection molding on parameters such as repeatability and cost, at least at low-medium volumes,” explained Fabian Krauss, global business development manager for polymers at EOS. “Without tooling time or tooling cost, AM is much more cost effective than injection molding.”
This graph from Jabil shows how the cost of injection molding, including mold cost, compares with AM. Jabil actively uses EOS, HP and Ultimaker printers in their production operations for consumer goods, automotive parts, jigs and fixtures, and medical device manufacturing.
This basic cost comparison does not capture the full story, however. Comparing AM and IM directly ignores the opportunities to redesign, customize and optimize products at the product lifecycle level.
Solution Engineering: Going Beyond Deposition Differences
The ‘tip of the iceberg’ is a tired analogy, but in this case it’s fitting. The fact that AM allows for production of plastic parts without a mold is the 5 percent of the iceberg above the waterline. The other 95 percent is below the surface. This is where solution engineering comes in.
When designing a 3D printing solution for a polymer part, engineers have the opportunity to step back and reexamine the part from a system level, considering the entire lifecycle of the part. In additive manufacturing, your part’s digital twin is not just a static model of what will be manufactured—it’s a dynamic part of the manufacturing process.
Read more at ENGINEERING.com
A manufacturing-as-a-service company has developed a way to 3D print continuous carbon fiber in a production setting.