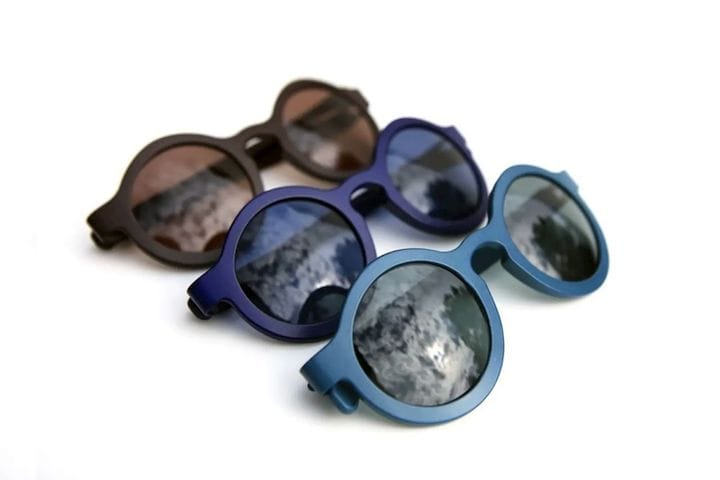
As the 3D printing space continues to transform into something that fits into industrial factory settings, we’ve seen materials expand, systems improve, and a trend toward automation. What has so far seemed to be the missing piece is an equal improvement in post-processing technologies.
One company looking to address that gap is Sheffield, UK-based Additive Manufacturing Technologies (AMT), which has developed a technology for modifying the surface area of a wide range of polymers, specifically with an eye toward 3D-printed parts. Not only that, but AMT aims to automate the entire 3D printing post-production process, from depowdering to inspection. To learn more, we spoke to AMT CEO Joseph Crabtree.
Post-Processing
Crabtree has a background in engineering, having spent the last ten years in traditional manufacturing, including in the aerospace and weapons industries. When he became exposed to 3D printing technology about three years ago, he also noticed the lack of attention paid to the post-processing space.
“Everyone’s either looking at raw materials or making a big splash about bigger, better faster printers, but this bit at the end—3D printing’s dirty little secret—wasn’t being addressed and we couldn’t believe it,” Crabtree recounted.
This led to the formation of AMT at the beginning of 2017. Using technology spun out of the University of Sheffield, AMT has created a range of products that modify the surface of 3D-printed parts without any manual intervention.
The flagship product, the PostPro3D, is a system that uses a proprietary “physiochemical process,” as Crabtree described it, in which a specialty liquid is converted into a vapor within a vacuum chamber. Parameters such as pressure, temperature and time can be precisely controlled to manage the surface modification of plastic parts.
Crabtree pointed out that the process doesn’t only smooth the texture of a component, but it can also strengthen a part and seals it as well (all with “no dimensional tolerance changes, no loss of fine features,” according to the CEO).
“Not only do we manage to smooth the part, but we’re also potentially improving the mechanical properties, such as elongation at break,” Crabtree said. Resolving all of the microscopic pores in 3D-printed parts thus makes them suitable for use in settings in which liquid penetration is an issue, such as in automotive or medical applications.
The liquid used for the PostPro3D is packaged in a consumable cartridge that is automatically re-ordered when the solvent runs out and relies on recycling used canisters. So far, over 85 different polymers have been validated for use in this process, including such standards as Nylon 12 and aerospace-approved materials like ULTEM 9085. Even elastomeric polymers, such as TPU, can be processed with the technology, despite the fact that other post-processing technologies, such as sandblasting, are too abrasive for such delicate materials.
The PostPro3D is currently available for sale and has a 100L chamber. AMT has also developed the PostPro3D Mini, with a chamber of only 30L, for use in universities, research labs and small manufacturing shops. The Mini is currently available for pre-order.
Read more at ENGINEERING.com