![Guitar v amp: winner, guitar. [Image: Sandvik]](https://fabbaloo.com/wp-content/uploads/2020/05/Smash-proofguitar8_512101_img_5eb09952d8ff2.jpg)
Or, rather, the 3D printed guitar that rock didn’t un-build: meet the smash-proof guitar.
3D printing has been providing new ways to think about instrument design, but many of these rethinkings have been in terms of sound, new capabilities, spare parts, accessibility, or otherwise playing into existing musical needs.
This time, it’s music and manufacturing to provide a smashing proof-of-concept — that couldn’t be smashed.
In action:
I’ll be pretty up front about most things, including my blind spots: I hadn’t heard of Yngwie Malmsteen prior to this week. That puts me in a minority, it seems, as the Swede is a rock legend, ranked by Time as one of the “10 greatest electric guitar players of all time.”
And of course, some stereotypes have basis in truth: this particular guitarist is renowned for smashing guitars during performances.
So why not create a guitar that could survive every performance?
Challenge accepted: Sandvik brought together a team to design and precisely engineer a fully metal guitar that specifically would hold up to Malmsteen’s roughhousing.
Sometimes a challenge seems a bit of a because-we-can more than the-world-needs-this, and you know what? That’s great. And can lead to useful applications, as techniques that can endure rockstar-quality stress-testing might just stand up to the rest of us who are more Rock Band than actual rockstar. Perhaps my Rock Band band (Deathbed Pony) doesn’t go through so many guitars as Malmsteen’s bands, but it’s nice to know strides are being made to reinforce guitars.
As seen in the video above, the project succeeded. So how did they do it?
A lot of expertise is the main answer.
Sandvik Coromant machining process developer and lifelong Malmsteen fan Henrik Loikkanen examined the mechanics of the smashing of a guitar: where does it break, and what would make it not?
The key point, he found, is “that critical joint between the neck and the body that usually cracks.” So, clearly, that joint should just be eliminated altogether: following digital simulation, the team milled the neck and fretboard in a single piece, created from recycled stainless steel.
Next, the body. To be a playable guitar, it needed to be the right size and shape, as well as strong and lightweight. Enter 3D printing. The Sandvik team 3D printed the body in titanium on a powder bed fusion system. With layer thickness of 50 microns, the body was a 56-hour print. The tailpiece that anchcors the strings and the volume knobs were also 3D printed. Post-processing involved blasting and machining each piece.
Materials science of course came into play as well, as the team used a specialized structure, an Isotropic Lightweight Structure (ILS) for the framework. The ILS, made of Sandvik’s hyper-duplex steel, was sandwiched between the neck and fretboard following careful examination into the welding process to avoid any issues with torsion.
Once the milling, 3D printing, and welding were complete, there it stood: a guitar. Initial tests saw the guitar stand up to some old equipment and furniture, but that wasn’t the Big Test.
Sandvik reports:
“At a club in Florida, Malmsteen ripped through several songs, then started swinging the guitar at amps, at stage structures, at the floor, doing his very best to smash it.”
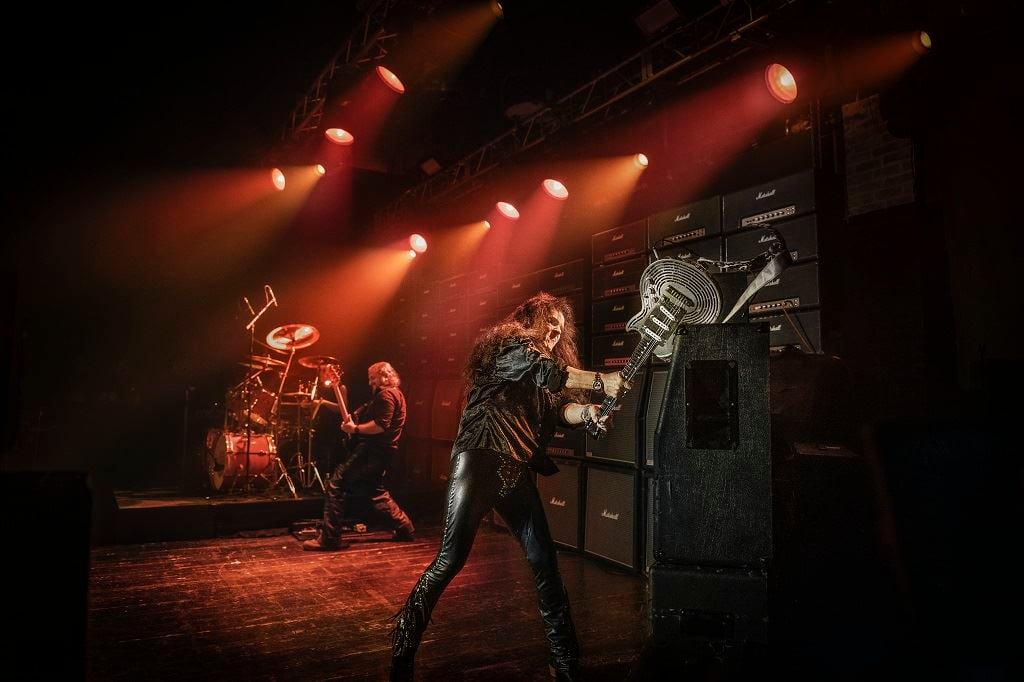
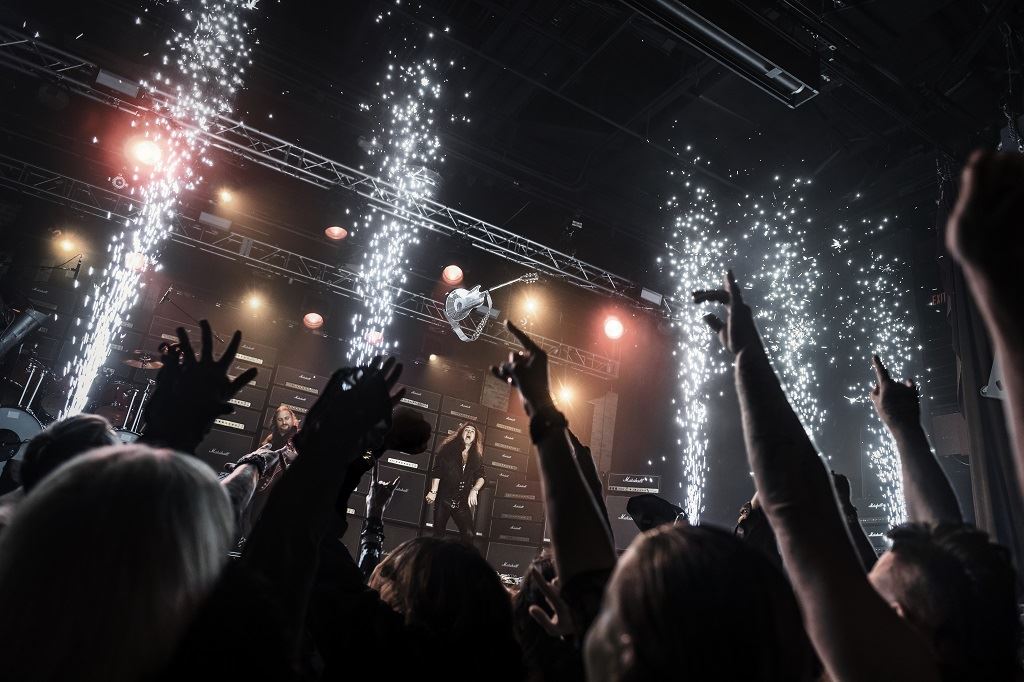
[Images: Sandvik]
Malmsteen, for his part, says that he “gave it everything I had, but it was impossible to smash.”
“To break it is impossible,” he noted. “But you can break other things with it.”
This is, let’s face it, a pretty cool application of mechanical engineering. Definitely more glam than most testing we hear about. But don’t let other headlines mislead: the entirety of the guitar wasn’t 3D printed.
As with the most successful applications of additive manufacturing, the technology was put to use where it made sense — alongside other processes.
Now that’s music to our ears.
More on the creation:
Via Sandvik