![3D printed building [Source: COBOD]](https://fabbaloo.com/wp-content/uploads/2020/05/image-asset_img_5eb099651d58a.jpg)
While we await livable 3D-printed homes and buildings, the field of additive construction is experiencing steady development.
China’s WinSun has made the most progress in terms of actually 3D printing buildings, but Danish firm COBOD International may be the most established when it comes to the manufacturing of construction 3D printers. COBOD has just unveiled its second-generation concrete 3D printer, the BOD2, and has signed a distribution agreement that will see the sale and rental of its equipment across Germany, Switzerland and Austria.
To learn more about the company and its technology, we spoke to COBOD Head of Communication Asger Dath.
From 3D Printers to 3D-Printed House
Dath explained that he and his colleagues didn’t initially plan to 3D print houses. With their Danish 3D printing company, 3D Printhuset, the eventual founders of COBOD began by selling 3D printers and scanners, as well as providing 3D printing services, consulting and 3D printer distribution. During that time, the group continually had ideas for other 3D printing-related businesses.
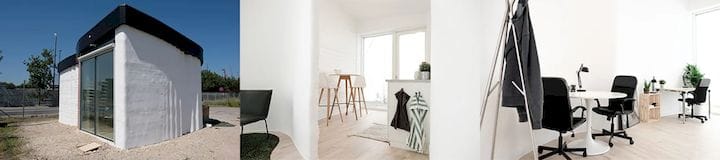
It wasn’t until it received a government grant from the Danish government that 3D Printhuset—along with other companies that included NCC Construction, Force Institute and Gypsum Recycling—became involved in additive construction. Upon visiting over 35 construction printing projects worldwide, the partners began testing materials and processes, and eventually created what they consider the first 3D-printed building in Europe: the BOD (“Building on Demand”).
The BOD is a 50-square-meter (538 sq. ft.) building with no straight walls, all of which were 3D printed, along with portions of the foundation. The team initially experienced difficulty with material handling, which caused some trouble with the 3D printer, but, once that was resolved, the print process itself performed as planned and took only 50 hours.
“We had to comply with the local building regulations and, because the technology is so new, there are no rules for that type of construction,” Dath said.“We incorporated pillars inside the walls where we made some rebar, which was then approved to be strong enough by the building regulators. The walls themselves were more than strong enough—I think it’s four times as strong as it needed to be—but because of the regulations [we incorporated] traditional ways of supporting the roof, which was pillars with rebar.”
In the past, it has often been a difficult task to find a concrete formula that can set quickly enough for use in additive construction. However, according to Dath, that is no longer the case.
![Scale of the COBOD construction 3D printer [Source: COBOD]](https://fabbaloo.com/wp-content/uploads/2020/05/cobod-scale_result_img_5eb09965af734.jpg)
“We have tested a bunch of different combinations of mixtures and it was very difficult in the beginning to get right,” Dath said. “It has actually gotten a lot easier just this year than it was before because more and more companies [that are] cement and concrete manufacturers are beginning to develop ready-mix concrete. That means that we can just take that and mix it with water and print. [Now, everything comes] down to the water content, how fluid [the concrete] should be.”
Quickly Growing
The project saw COBOD’s development of its first-generation 3D printer, the BOD1. The BOD2 is meant to be a significant improvement over its predecessor, in that it is faster (printing at 1000 mm/s) and modular. This second detail means that COBOD can modify the system’s size depending on the interests of the customer.
If you visit the firm’s website, you can find an extensive pricing sheet that describes how each additional module for the printer increases its volume and price. The smallest system, with one 2.5m module for the X-axis and another 2.5m module for the Y-axis begins at €180,000 and will get you a build volume of about 1.87m x2.13m x4.05m. At the other end of the spectrum, the largest machine—made up of 18 Y-axis modules of 2.5m each, 5 X-axis modules of 2.5m each—is priced at €950,000 and will get you a build volume of 11.98m x45.07m x9.10m.
So far, the company has several sales in the pipeline and has delivered its first 10-cubic-meter BOD2 3D printer to Kamp C in Belgium, which plans to produce a two-story building with the system. The biggest unitordered so far, described as capable of producing buildings 12x27x9m, buildings, has been purchased by Elite for Construction & Development Co. in Saudi Arabia.
This growth is being fueled in part by the PERI Group, a German formwork and scaffolding manufacturer. The PERI Group purchased a significant minority stake in COBOD in 2018 and recently announced that it will distribute BOD2 printers for sale or rental in the three countries in which it operates: Germany, Switzerland and Austria. Outside of Europe, COBOD has partnered with 3DVinci Creations to distribute its 3D printers in the United Arab Emirates.
Read More at ENGINEERING.com
COBOD’s BOD2 construction 3D printer seems to be catching on as the company has made multiple sales of the new device.