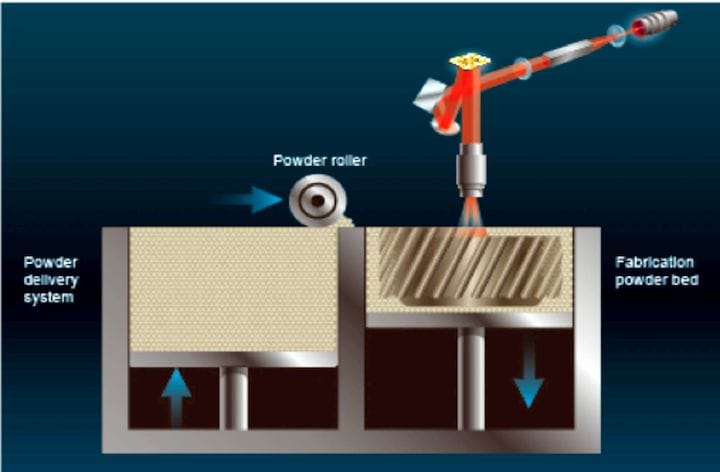
Stereolithography introduced to the world the possibility of turning digital CAD models into physical reality by directing a laser at a vat of photopolymer resin, point by point and layer by layer until that object was realized.
The introduction of digital light processing (DLP) technology brought a new level of speed to the world of 3D printing through the ability to cure large swathes of material, rather than point by point.
Now, similar DLP technology could potentially be brought to selective laser sintering (SLS) and other additive manufacturing (AM) technologies thanks to a development from Texas Instruments (TI). Engineering.com spoke to Raecine Meza, business manager for Industrial DLP Products at TI, to learn about the company’s new near infrared (NIR) digital micromirror device (DMD) and its potential impact on 3D printing.
From DLP to SLS
Typically, with 3D printers using DLP technology, a light source, often an LED screen, is cast onto a DMD, made up of hundreds of thousands to millions of microscale mirrors that then project the light onto a vat of photopolymer resin. With each layer, a new pattern of light representing an individual 2D slice of a 3D object hardens the liquid into a solid shape. The process continues with each new layer until the object is fully formed and is then removed from the vat.
Until now, the DMD for industrial systems was capable of withstanding the heat from the light source, associated with energy in the ultraviolet range. TI’s new DMD, the DLP650LNIR, can withstand even greater heat, associated with a NIR range of between 950 to 1150 nanometers. This makes it possible to project a NIR laser with up to 160W of power at the DMD, and bounce it through an optical set up and onto a print bed to melt plastic powder.
In other words, some of the capabilities that DLP technology brought to the vat photopolymerization market can now be introduced to the plastic powder bed fusion market. Rather than fuse plastic powder point by point, as is the case with SLS, it’s possible to melt or sinter that powder layer by layer or section by section, depending on the actual build area and machine set up.
“What we’ve done is we’ve really married the device with a very nice thermal package so that we can be very efficient at dissipating the heat that might be generated as we apply those wavelengths to the array,” Meza said. “Then we’ve also increased the window transmission for the wavelengths of interest.”
While Meza did not have any specific numbers related to print speed, she did believe that using the new DMD would increase the speed at which plastic parts could be produced, when compared to traditional SLS. Moreover, Meza pointed out that the DMD enables much greater thermal stability than was previously available, opening up finer, more complex print details printed at constant speeds.
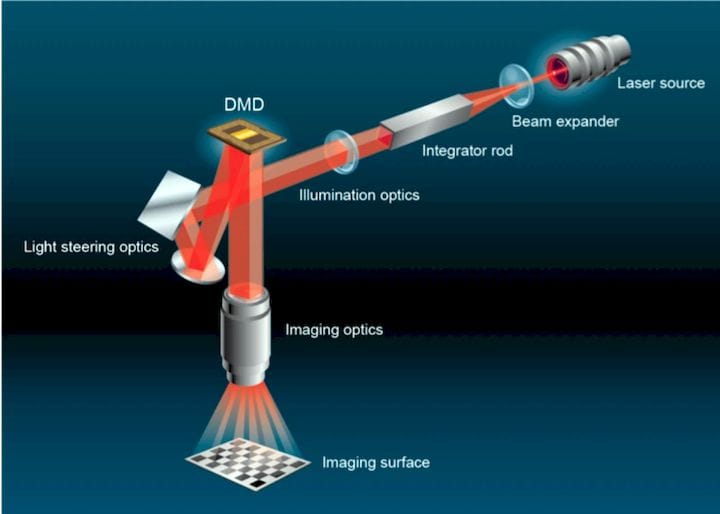
Most SLS printers rely on mechanical systems for fusing powder, such as galvanometer mirrors. Even high-speed sintering (HSS) and Multi Jet Fusion (MJF) use mechanical inkjet heads. In either case, the mirrors or heads may require recurring maintenance or calibration. Because DMDs are digital, this sort of calibration or maintenance can be reduced or eliminated with this method. The system is also programmable, introducing more flexibility to the printing process.
“Controlling thermal drift or variation across a system is a very common engineering challenge,” Meza explained. “The ability to have fast, real-time programmability for where heat is delivered has several implications to it.”
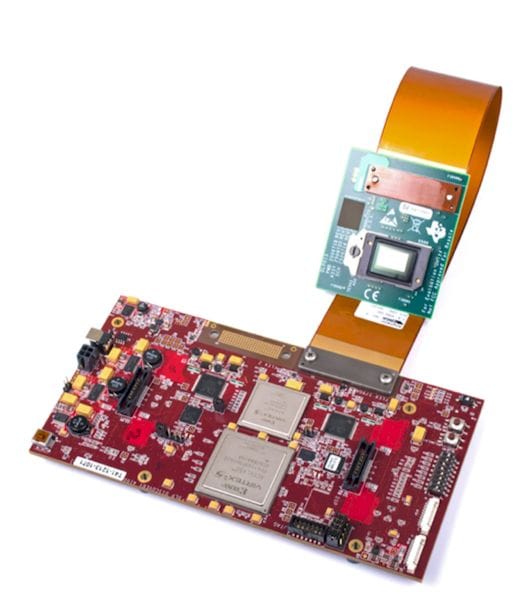
The DMD chipset can be purchased on its own, bundled with electronics such as a TI evaluation module, or as part of an optical light engine for a given application.
Beyond SLS 3D Printing
Our interest lies mainly with 3D printing, but Meza described two other applications for the new chipset that could have significance for AM. One application is meant for industrial printing or marking in which packaging can be customized in real time with complex information. Intricate logos or marketing offers could be produced on a per-package basis. More elaborate serial numbers could also be added to packages for real-time supply chain tracking.
Read more at ENGINEERING.com
Formlabs just issued three new videos for beginners to 3D printing, and the result was quite surprising.