![Matt and the beginnings of Batman the Ride [Image: Fabbaloo]](https://fabbaloo.com/wp-content/uploads/2020/05/matt1_img_5eb09ca7cbe6e.jpg)
Even when 3D printing is fun and games, there’s a lot of engineering behind it.
So it’s a good thing Matt Schmotzer has a background in mechanical engineering. When he was a student at Purdue, all student work in his department relied on SOLIDWORKS. So it made sense that I met him at this year’s SOLIDWORKS World, where he was putting together his latest roller coaster model.
Schmotzer has been working for a few years now on his functional models of well-known rides from various theme parks. He shows them at various events, where we’ve heard about all that goes into their creation, and it’s not just makers and designers who think they’re cool — the coasters have been drawing attention from the very parks whose coasters he creates.
“It began because I’ve always loved roller coasters — so I became a mechanical engineer,” Schmotzer, whose Print My Ride Detroit project fits around his full-time work at Ford, told me. “I’ve always been a creative person and like to put ideas into reality. 3D printing is the best way to make that happen affordably.”
He had drafted up a design of Invertigo, a roller coaster at King’s Island, and the design sat there for a while. It clicked one day, he said: “why not 3D print it at 1:32 scale?” So he did; it took three iterations to create a functional roller coaster, and, “through luck or otherwise, it all came together.”
“When I made Invertigo, as I was building it I talked to a professor at Purdue. The department for theme parks was interesting, so the day after I completed it I showed them, and they loved it. That’s students who are pursuing careers in theme park engineering, and they wanted to know everything. Purdue published a video, and theme parks took notice,” he said.
After the video, Cedar Point asked how they could be involved. Schmotzer is currently working on a model of Steel Vengeance, which will be a non-functional model at the park’s museum.
At SWW, Schmotzer brought his current work in progress: Batman the Ride, from Six Flags in Texas. It seemed fitting as SWW was held in Dallas this year.
“The overall response has been great, and not just from coaster enthusiasts, really from cross-functional industries,” Schmotzer said.
To create this coaster, he used 3D printing, CNC, and laser cutting. The hardware coming into play as far as 3D printers go includes 6 LulzBot TAZ, a Formlabs Form 2 and a Form 1+, and two FlashForge Finders.
“They’re all workhorses. I use the LulzBots for large pieces, and the FlashForge for support joints. The Formlabs printers are critical for train design, and for small pieces that really need the resolution of SLA, going down to M2 fasteners,” he said. “For materials, I use mostly PLA; it’s cheap and not prone to warping. There’s some ABS for stressed points. For SLA, I use mostly Standard Grey, and some Tough Resin.”
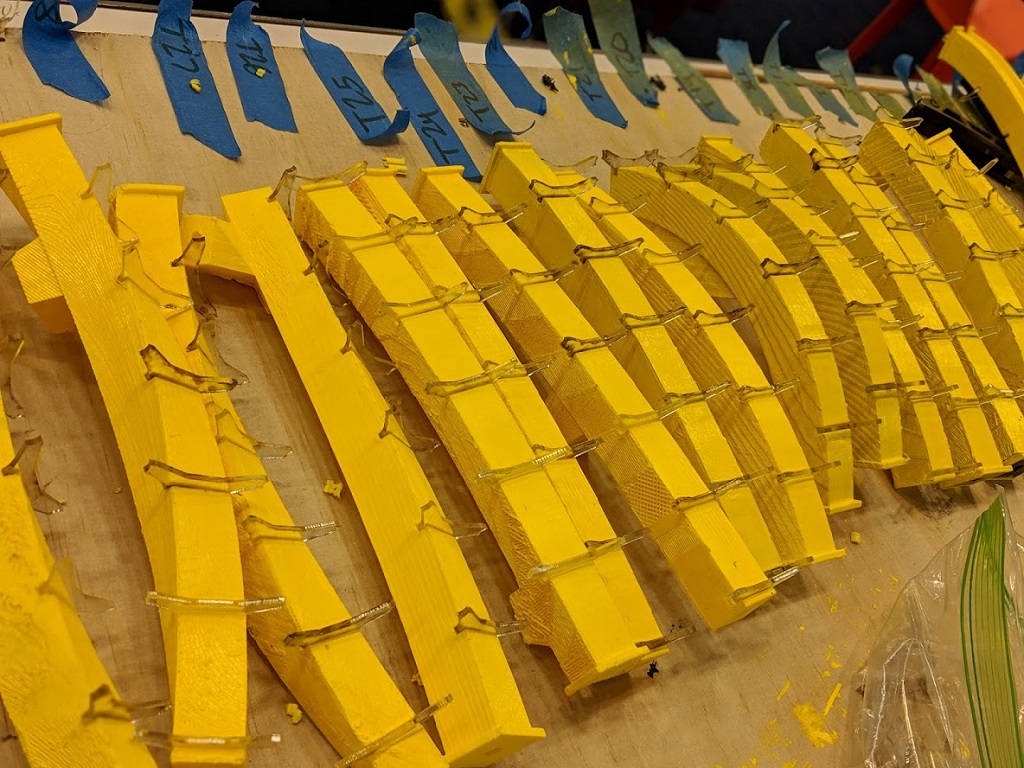
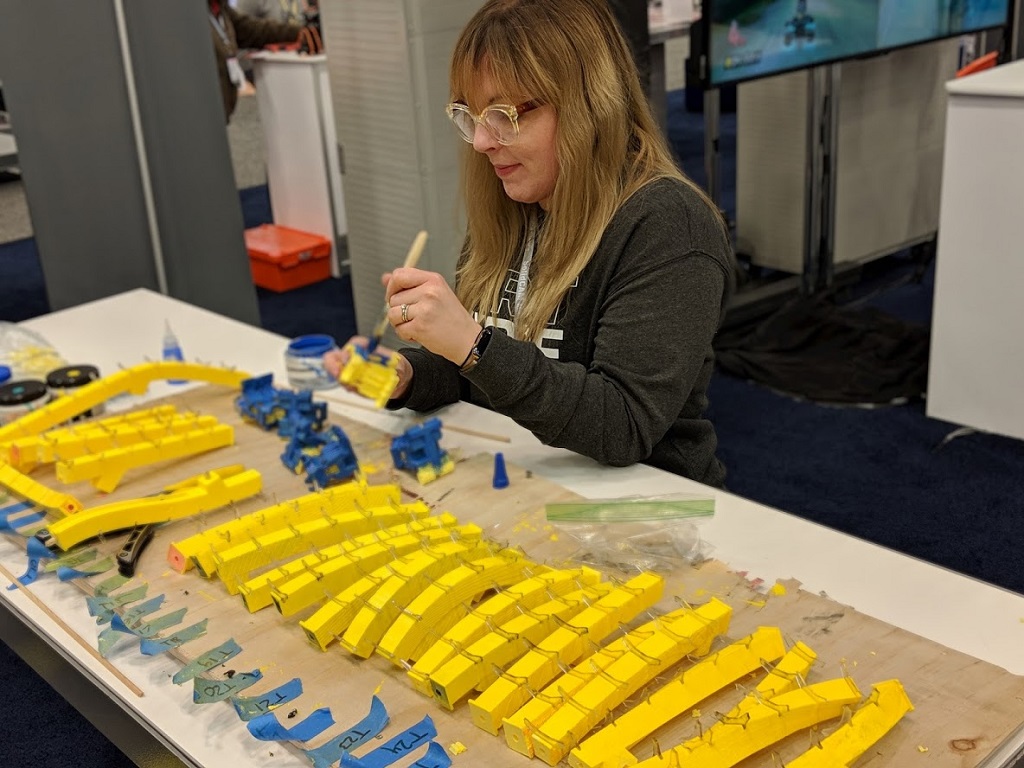
The Batman model took a while to 3D print: with 88 track sections, each taking about four hours of print time, and more than 128 supports each at about one hour, the part creation took about 400 hours. The spines were laser cut. Then came assembly. At SWW, Schmotzer’s wife Heidi, introduced as an expert painter, was doing a beautiful job painting the pieces to match the real Batman the Ride look. Once ready, the coaster was assembled on-site at SWW, though without the electronics or trains for this display.
The 3D printed model was a popular draw in the Game Lounge section of SWW, and no surprise. Schmotzer’s work has drawn plenty of attention as the engineering behind the fun of a running roller coaster is itself involved and highlights the creativity behind entertainment.
![Track progress on day two of SWW [Image: Fabbaloo]](https://fabbaloo.com/wp-content/uploads/2020/05/matt5_img_5eb09ca94c07a.jpg)
This week’s selection is a 3D printed Coronavirus!