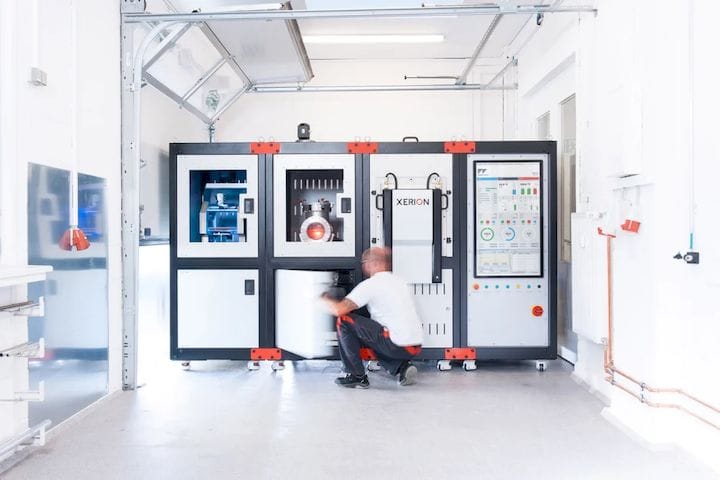
Given the relative newness of metal 3D printing, many in the industry anticipate a continued evolution of the technology that will see it increase in quality and decrease in cost.
At formnext, German furnace manufacture Xerion demonstrated this possibility with the introduction of its Fusion Factory, a modular system for 3D printing, debinding and sintering metal and ceramic parts.
To learn more about the technology, engineering.com spoke to Xerion CEO Uwe Lohse, who was able to shed light on how the Fusion Factory fits into the larger 3D printing market.
From Furnaces to Fusion Factory
Xerion was founded 20 years ago with a focus on designing and manufacturing electrical furnaces, mostly those that use high temperature and inert gas. According to Lohse, the company began receiving requests from customers in the additive manufacturing industry a few years ago. In response, Xerion began looking into both producing the furnaces and a complete production line.
The Fusion Factory is made up of four units representing three technological steps and a control unit. The first begins with 3D printing unique metal or ceramic filaments made up of a combination of metal or ceramic powder and a binder. Within this module is an industrial 3D printer featuring a specially designed steel nozzle and feed mechanism capable of processing the filaments.
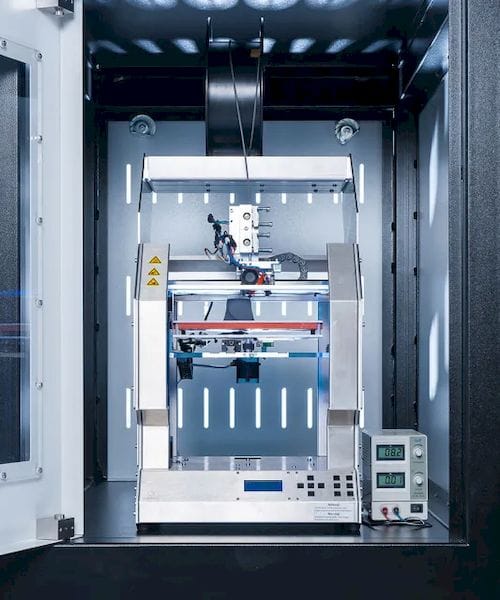
Once the green part is printed, it is placed into a heated debinding station, which automatically uses an acetone/isopropyl alcohol solvent to wash out the binder within a nitrogen gas atmosphere. The resulting component is a fragile, porous structure, now that the binder has been removed.
The part is then placed into the third module, an electric furnace capable of reaching temperatures of up to 1,550° Celsius within a nitrogen or hydrogen atmosphere, depending on the material. For 17-4 PH and 316L stainless steels—the metals on which Xerion is currently focused—the gas is hydrogen. For over 10 hours, the component is heated to the point that the metal or ceramic particles are fused together, producing a part with 98 to 99 percent density.
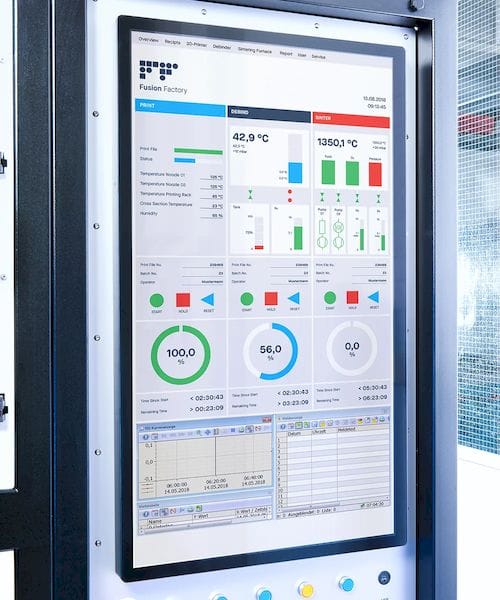
All of this is managed with a control unit, consisting of a large touchscreen used to oversee and monitor each of the production steps. Built into Fusion Factory is a database management system that stores preprogrammed “recipes” that streamline the production process by applying the proper controls to each module. The software also compensates for shrinkage that occurs during the sintering process and can generate reports used for documentation purposes.
The Advantages of Filament
Anyone familiar with the process of metal injection molding (MIM) will recognize the above steps. In fact, anyone who has been following the metal 3D printing industry should recognize those steps by now. Beyond ExOne, which uses binder jetting to deposit a binder onto metal particles to create green parts, both Markforged and Desktop Metal have introduced 3D printing technologies similar to MIM.
Xerion may be the first company in Europe to offer a complete, integrated solution for 3D printing and processing metal parts. It may be the first firm globally to use that same MIM-inspired process for ceramic components, though there are other companies using different technologies for ceramics.
Lohse pointed out how the use of filament to make metal parts differs from powder bed fusion 3D printing. “You don’t have the problems with powder handling. Of course, filament is easy and convenient to handle. You have filament spools that you can swap out very quickly,” Lohse said.“Of course, investment [in the Fusion Factory] is not as high as in a [powder bed fusion] system.”
With powder bed systems, powder must be managed carefully, with parts removed from the print bed in specialty handling stations. Not only is the powder extremely flammable, but it can be inhaled, potentially causing lung damage. Additionally, due to the sophisticated nature of the technology, powder bed systems can cost half a million dollars.
Possibly the least expensive powder bed fusion machine is produced by Xact Metal,which has a price of $120,000 and features a build volume of only 127 mm x 127 mm x 127 mm. This compares to the Fusion Factory’s €250,000 ($283,000) price tag and build volume of 245 mm x 230 mm x 200 mm.
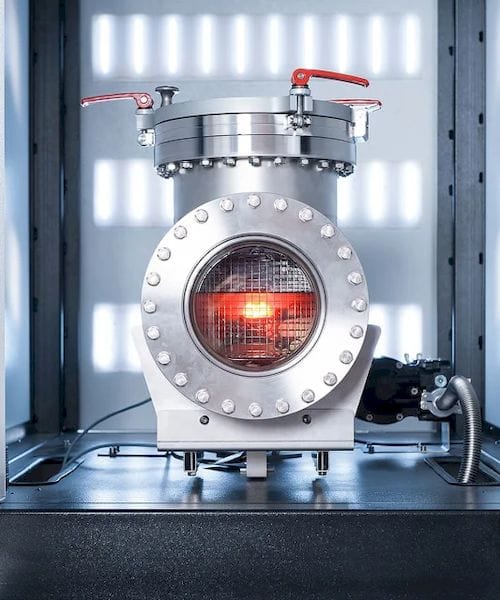
“The printer also features a dual extruder, which means that it can print with two different filaments at the same time, which opens up the possibility of mixing the filaments to produce parts made up of metal and ceramic compounds.”
Material combinations are still in the research and development phase, but Lohse believes that it may be possible to coat a metal part in ceramic in order to add friction and chemical resistance for potential use in the oil and gas industry. So far, the company has successfully printed 17-4 PH stainless steel with zirconium. The greater difficulty may be sintering these blended materials because the process would require that they have the same shrinkage rate and thermal expansion coefficient.
In some cases, differences in the physical responses of materials to the production process may actually lead to uniquely beneficial properties. For instance, if two materials sinter at different rates, one may end up being more porous than the other, resulting in a component that is partially dense and partially porous for some experimental application.
This ties into yet another benefit that filament may have over powder bed fusion. Due to the nature of laser sintering, parts cannot feature internal voids, lest the unsintered powder get trapped within the part. With filament, however, hollow infill patterns such as a honeycomb structure can be printed to create strong, lightweight parts.
Read more at ENGINEERING.com
An inventive designer has developed a method for producing 3D paper objects using recycled paper and 3D printed molds.