![RAL colors available from DyeMansion [Image: Fabbaloo]](https://fabbaloo.com/wp-content/uploads/2020/05/IMG_20181116_132505_img_5eb0a256519e9.jpg)
The future is bright — and brightly colored — for post-processing 3D prints.
DyeMansion has been working to enhance the variety of finishes possible, and the company’s new VaporFuse Surfacing (VFS) process and widening spectrum of color matches highlight new possibilities in post-processing. During formnext, I appreciated the chance to catch up with the company as R&D Chemist Dr. Alena Folger, who developed the process, walked me through VFS.
“We use vapor to condense on the part, which is cooler than the vapor. A thin layer of liquid solvent then dissolves at only the surface, reducing the surface energy to get a system with lower energy. Then we just remove the solvent and the polymer hardens again,” she explained.
![Dr. Alena Folger standing in the blue-outlined footprint of the VFS system [Image: Fabbaloo]](https://fabbaloo.com/wp-content/uploads/2020/05/IMG_20181116_131937_img_5eb0a256e985e.jpg)
Parts thus reach a better density, as well as a smoother surface — smoother even than that achieved with DyeMansion’s PolyShot Surfacing (PSS). Compared to PSS, which offers a matte glossy look with high resistance to scratching, VFS leaves parts with a high-gloss, water-repellent surface. PSS is a mechanical process, while VFS is chemical-based and rivals injection molding in finish, fulfilling DyeMansion’s recent hint at their next introduction.
A side-by-side comparison highlighted the differences in finished part properties as well as look and feel of the different techniques: below is the same part 3D printed in PA12 material (left to right) unfinished, dyed, processed with PSS, and processed with VFS.
![[Image: Fabbaloo]](https://fabbaloo.com/wp-content/uploads/2020/05/IMG_20181116_131502_img_5eb0a25797277.jpg)
The solvent used with VFS is safer for use than the acids and solvents traditionally used in post-processing, and VFS was developed with an expansion in material handling in mind. Existing solutions, Pia Harlaß, DyeMansion’s Head of Marketing, noted, were “not quite enough for flexible materials” and the new process is able to be used with more diverse options, including soft materials like TPU, in addition to the harder polymers (e.g., PA11, PA12) in the PSS workflow.
VFS is still in development now, and the company is looking for beta customers to get the solution closer to market.
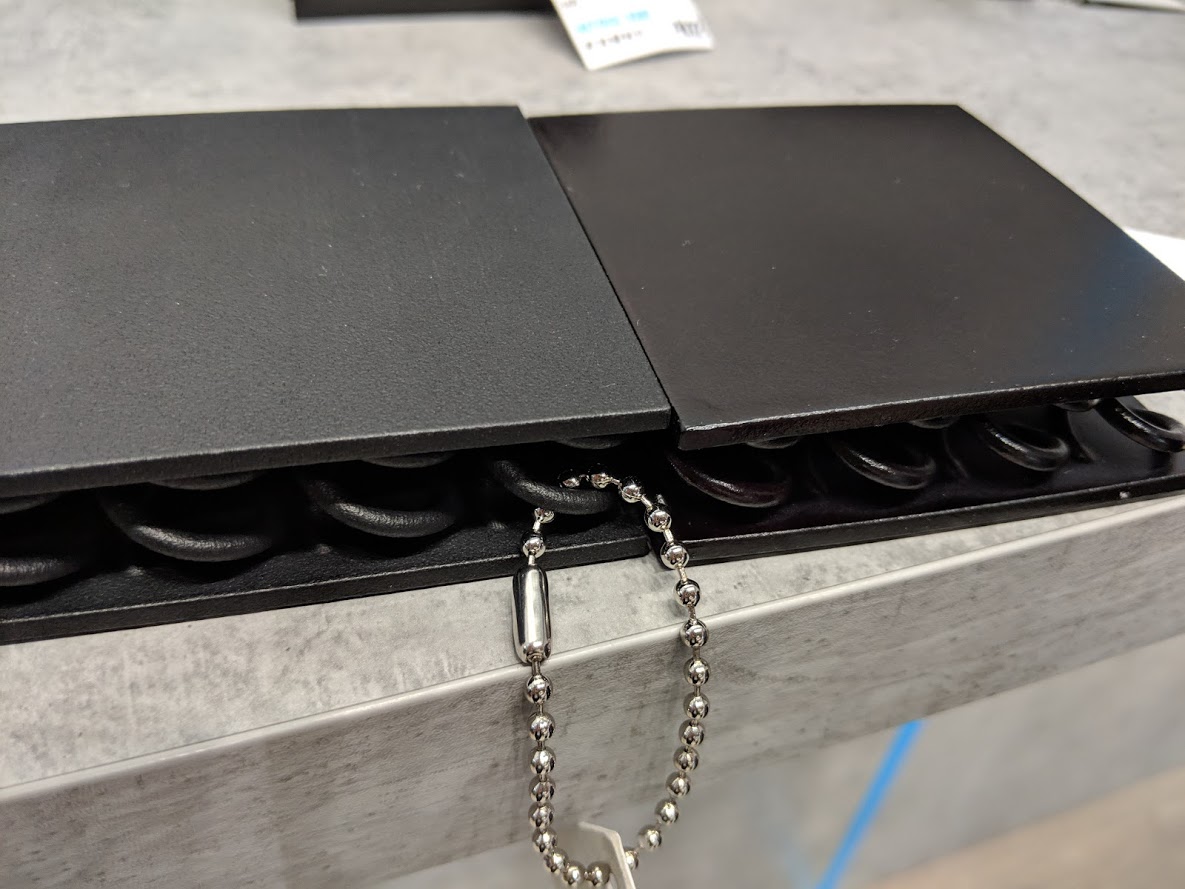
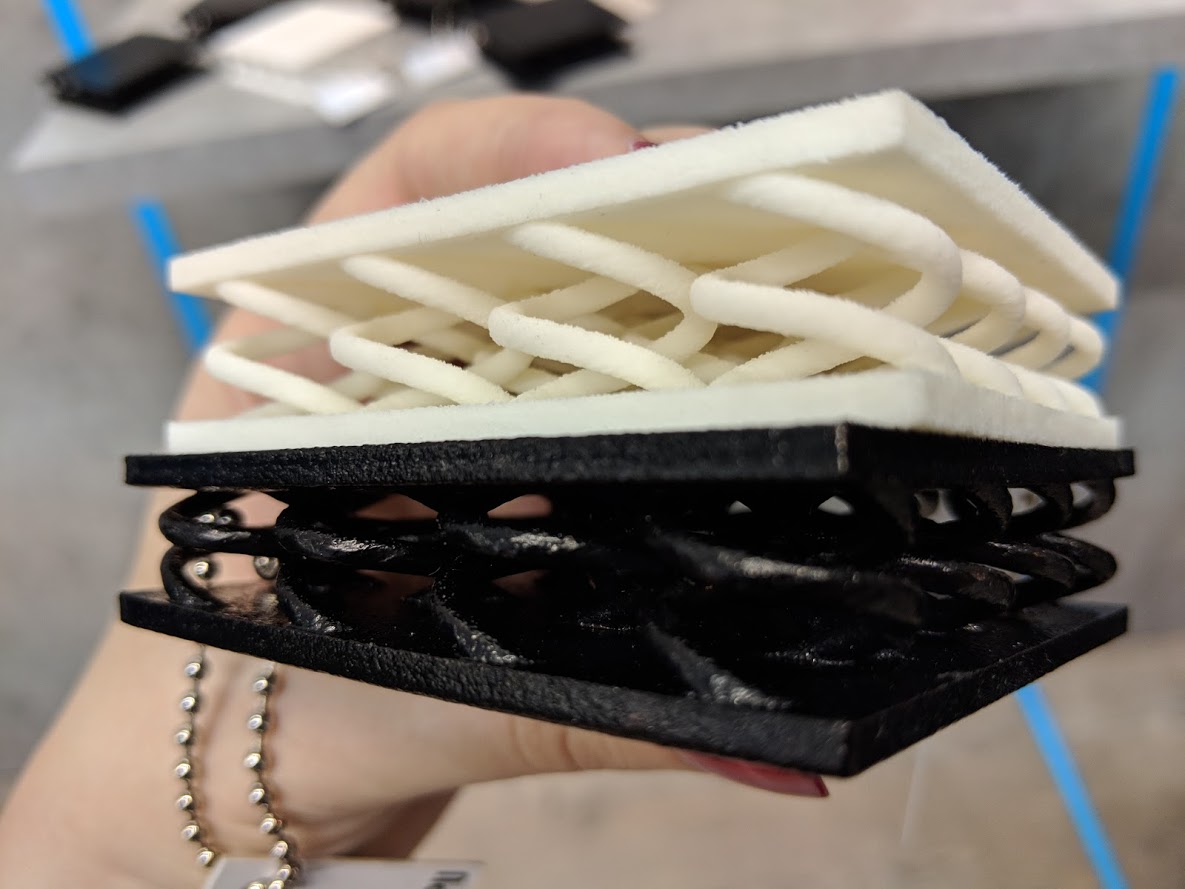
We turned our attention as well to other finishing options, as DyeMansion continues to focus as well on color. Color is, after all, a key attribute and is ever more in focus for 3D printing as the technology settles into our technicolor world.
Standardizing colors and consistently achieving them is key, and DyeMansion is able to offer nearly the entire RAL range of color (a range we explored recently here). The shades missing from DyeMansion’s wall are metallics and more varieties of whites and blacks — though there are many greys.
![[Image: Fabbaloo]](https://fabbaloo.com/wp-content/uploads/2020/05/IMG_20181116_132509_img_5eb0a25925439.jpg)
“We’re working to provide more options like users would expect from traditional manufacturing, to provide the ‘perfect’ finish for every application,” Harlaß said with air quotes around “perfect.”
For DyeMansion, she continued, “Color is the true freedom of design” in 3D printing — it’s not just about the unique geometries possible.
“We are always working closely with big manufacturers to be compatible. We work with HP, voxeljet, Farsoon, 3D Systems, Sintratec, EOS, Prodways, and many more,” she added.
![[Image: Fabbaloo]](https://fabbaloo.com/wp-content/uploads/2020/05/IMG_20181116_132256_img_5eb0a259775f4.jpg)
Helping in this color freedom is a new white powder HP is working on for its Multi Jet Fusion systems, which will help dyes show better than on a dark base material. Use of a lighter base is significant in expanding color ranges and ensuring true color matches.
With the expansions in its post-processing capabilities and range of solutions, DyeMansion is working toward an ambition of leadership in the finishing space — and, having felt the quality they’re hitting, their way ahead seems clear as the talented team continue to advance.
![[Image: Fabbaloo]](https://fabbaloo.com/wp-content/uploads/2020/05/IMG_20181116_133509_img_5eb0a25a06da3.jpg)
Via DyeMansion
Some thoughts about the ongoing dilemma of obtaining good surface quality on production parts made using additive manufacturing.