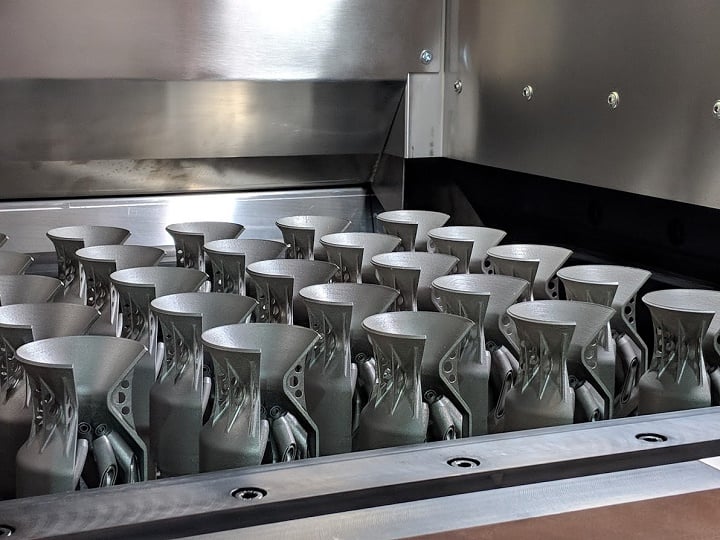
3D Systems’ latest major partnership brings a new hybrid machine and a statement about the place of additive in the manufacturing workflow.
At the company’s press conference at IMTS last week, President and CEO Vyomesh Joshi (VJ) followed up on the statements made at the massive 3D Systems event at the last IMTS. In 2016, the company introduced an expanded vision geared toward production applications across targeted verticals. On a much smaller stage this year, VJ discussed progress since that announcement of strategy.
“In my view, the exciting opportunity for 3D printing is in the manufacturing workflow. We presented the vision in 2016, and spend the next two years creating the foundation,” VJ said, naming four key success factors for the company:
-
Customer-driven innovation
-
Operational excellence
-
Partnerships
-
Our people
“Where we are going is production workflows, he continued. “The key for me is in building platforms.”
To that end, 3D Systems announced its “transformative partnership” with Georg Fischer AG’s GF Machining Solutions division. The two jointly launched the modular, scalable DMP Factory 500 hybrid machine. Set to “bring automation to the manufacturing of metals,” VJ said, the system is “not about additive or subtractive,” but about production.
Adding that 3D Systems has the broadest portfolio in 3D printing — “That is no question” — VJ noted that the technology must always offer the “right value proposition” for adoption to take root. Touching on other areas, such as the attention-grabbing Figure 4 system and the company’s work with orthodontic aligners, VJ concluded his discussion by noting that materials “are the next frontier: at the end of the day, it’s a materials game.”
For a further look into the company’s latest strategies and work toward production, I sat down with Kevin McAlea, Executive Vice President, Healthcare and Metals Business Units, for a chat about the GF partnership, manufacturing workflow, and automation.
“The partnership makes good sense from several angles,” he said. “3D printing is transitioning into advanced manufacturing with significant volume and large printers; these need to integrate with traditional manufacturing. Most processes require significant post-processing and a fairly complex process chain. Today, these handoffs are pretty awkward. With GF, we can streamline these.”
The DMP Factory 500 integrates a clamping system that allows for carrier plates to go directly from printing to a 3D printing-specific wire EDM without reestablishing the data chain, he noted, enabling traceability. GF has been “thinking ahead to optimize their operations to 3D printing,” allowing for a strong bond between the two companies in leveraging their strengths in both additive and subtractive technologies. The system will allow for automation in having parts drop into a basket following their EDM removal, and in a removable cart system that can go from printer to post-processing to avoid bottlenecks and get the next cart ready to print, reminiscent of the process for HP’s Jet Fusion 3D printers.
“GF has significant automating experience; this is something we teed up quickly to work with them on. We’re focusing on ways to merge additive and subtractive. They also have strength in knowledge and have built credibility; that’s why we co-branded the product. We also have separate sales teams that, put together, create comprehensive coverage and ultimately provide better service,” McAlea continued. “It’s a powerful combination: GF’s precision machining with our precision metal experience.”
IMTS, which offered more focus on additive manufacturing than previous years, remains the playground of traditional manufacturing. Working with a partner outside of additive brought attention to this type of technology; GF’s booth in the North Hall, not 3D Systems’ booth in the AM Pavilion in the West Hall, housed the new system. Showing the machine alongside broader traditional technologies was a nod to the fact that it is indeed at home in the general manufacturing workflow. The strategy worked, as McAlea noted a strong reception to the system during IMTS.
“The partnership has had a big response at an event like this; it’s compelling. It’s interesting to see 3D positioned here, centerstage as a manufacturing tool,” he said.
The integration with GF is one with significant potential for 3D Systems, and while the company knows where that partnership starts, “we don’t know where it ends,” McAlea noted of ongoing work together.
Also picking up is the 3D printing industry itself.
“Ten years ago, you could walk into a large company and they’d be aware of 3D printing, there would be some model shop use, but not many were seriously considering it for manufacturing. Even with hearing aids, with Align, as well known successes. Today, talk to any aerospace or large industrial company, every one has a plan for using 3D printing. Some are more ambitious, some are more mature, highly regulated industries move more slowly — but they all have plans,” McAlea told me.
“That’s what I see as remarkable, this change: they all have plans, they’re taking this technology seriously.”
Medical applications provide a strong support to his point; if 10-20% of medical devices could be 3D printed, claiming that sizable a piece of a massive global industry is “pretty incredible.”
“3D printing is becoming mainstream and even critical for building certain kinds of parts,” he added.
Looking outward, we turned the conversation to the competition.
“What’s happening in this business is more segmentation of applications. Look at green part technologies; you have Desktop Metal, Markforged, and now HP, with real opportunities for furnace processes,” he began. “What used to be a small number is bigger, and there are more segmenting opportunities — focus on part quality, on speed. None by themselves can do anything, there’s a fit in this range of opportunities.”
Previous years of hype are still having an impact on the shape of the market for 3D printing, McAlea noted.
“The fallout from hype around 2015 was bad in some ways, but also had some benefit. It unleashed new funding, new venture capital, which was very positive,” he said. “For 3D printing to grow, we need new funding, we need new ideas. Not all will survive, but it’s a fact that the level of venture capital, creativity, and technology hubs has been very healthy for the industry. It drives development internally and awareness externally.”
And the shape of increasing competition in 3D printing?
“It’s very positive, even if sometimes I personally lose sleep over announcements; overall, competition is very healthy for the industry,” he said with a smile.
We closed out our chat on a positive note, as McAlea circled back to the opportunities the new DMP Factory 500 system represents. Such a step shows that 3D Systems is “entering advanced manufacturing opportunities with the Factory 500 at just the right time,” as the differentiated technologies arising from their facility in Belgium and their work with GF “allows us to scale in new ways.”
“We’re poised to do well in the years ahead,” he said in closing.
Via 3D Systems
[All photos: Fabbaloo]